Low-temperature smoke denitration SCR (silicon controlled rectifier) catalyst and preparation method
An SCR catalyst, low temperature flue gas technology, applied in catalyst activation/preparation, chemical instruments and methods, physical/chemical process catalysts, etc. problems such as poor strength, to achieve the effect of favorable molding and subsequent processing, low price and high mechanical strength
- Summary
- Abstract
- Description
- Claims
- Application Information
AI Technical Summary
Problems solved by technology
Method used
Examples
Embodiment 1
[0049] 1) Preparation of the carrier
[0050] Calcinate 0.3mm rod-shaped glass fiber in a muffle furnace at 600°C for 2h, take it out, acidify it with a sulfuric acid solution with a mass concentration of 30% for 2h, wash it with distilled water until neutral, dry it at 100°C, and grind it with Machine crushed it to 60 mesh powder.
[0051] 2) Catalyst loading
[0052] The glass fiber powder is placed in the mixed solution of manganese nitrate and cerium nitrate, soaked for 12 hours, and then dried in a water bath to complete the loading by dipping. Then it was dried at 120°C for 12h, and finally calcined at 350°C for 5h under the protection of nitrogen atmosphere to obtain the catalyst. Mn and Ce in the catalyst account for 30% and 5% of the overall mass of the catalyst including glass fibers, respectively.
[0053] 3) Activity test
[0054] The activity experiment was carried out on a fixed-bed reactor, the loading amount of the catalyst was 2ml, and the particle size wa...
Embodiment 2
[0056] 1) Preparation of the carrier
[0057] Directly use diatomaceous earth as the carrier.
[0058] 2) Catalyst loading
[0059] After dissolving manganese nitrate and cobalt nitrate, diatomaceous earth was placed in it to soak for 24 hours, and then dried in a water bath to complete the loading by impregnation. Then dry at 100° C. for 24 hours, and finally calcinate at 450° C. in air for 4 hours to obtain a catalyst. Mn and Co in the catalyst account for 40% and 10% of the overall mass of the catalyst including diatomaceous earth, respectively.
[0060] 3) Activity test
[0061] The activity experiment was carried out on a fixed-bed reactor, the loading amount of the catalyst was 2ml, and the particle size was 40-60 mesh. The initial gas concentration is: NO and NH 3 Both are 1000ppm, O 2 3%, the rest is N 2 . The reaction space velocity is 60000h -1 , when the reaction temperature is 120°C, the denitrification efficiency is 85.2%, and when the reaction temperatur...
Embodiment 3
[0063] 1) Preparation of the carrier
[0064] Calcinate the granular glass fiber in a muffle furnace at 600°C for 2 hours, take it out, acidify it with a 20% hydrochloric acid solution for 6 hours, wash it with distilled water until neutral, dry it at 120°C, and crush it with a pulverizer Crush to 40 mesh.
[0065] The diatomite is used directly, wherein the mass ratio of diatomite / (diatomite+glass fiber) is 60%.
[0066] 2) Catalyst loading
[0067] After dissolving manganese nitrate, place diatomaceous earth and glass fiber in it to soak for 24 hours, and then carry out water bath drying to complete the loading by dipping method. Then it was dried at 100°C for 24 hours, and finally calcined at 450°C in air for 4 hours to obtain the catalyst. Mn in the catalyst accounts for 20% of the overall mass of the catalyst including the carrier.
[0068] 3) Activity test
[0069] The activity experiment was carried out on a fixed-bed reactor with a catalyst loading of 2ml and part...
PUM
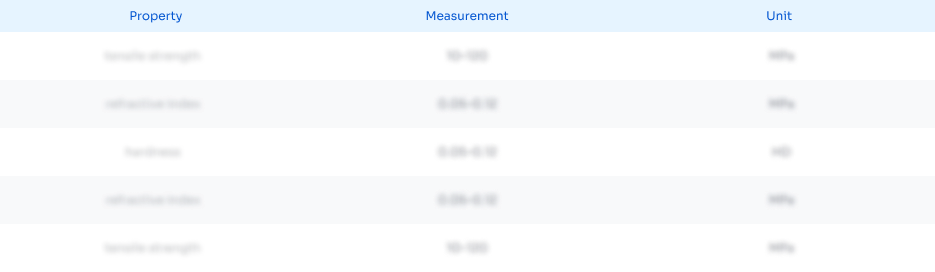
Abstract
Description
Claims
Application Information

- Generate Ideas
- Intellectual Property
- Life Sciences
- Materials
- Tech Scout
- Unparalleled Data Quality
- Higher Quality Content
- 60% Fewer Hallucinations
Browse by: Latest US Patents, China's latest patents, Technical Efficacy Thesaurus, Application Domain, Technology Topic, Popular Technical Reports.
© 2025 PatSnap. All rights reserved.Legal|Privacy policy|Modern Slavery Act Transparency Statement|Sitemap|About US| Contact US: help@patsnap.com