Beneficiation method for recovering copper in copper smelting slag and beneficiation reagent
A technology of beneficiation agent and copper smelting slag, which is applied in flotation, solid separation, etc., can solve the problems of easy oxidation and decomposition, reduced vulcanization effect, poor floatability, etc., achieve high recovery rate of copper concentrate and improve vulcanization efficiency , the effect of improving stability
- Summary
- Abstract
- Description
- Claims
- Application Information
AI Technical Summary
Problems solved by technology
Method used
Image
Examples
Embodiment 1
[0044] The grade of copper in the high-temperature smelting slag of a smelter is 1.25%, most of which co-exist in the form of copper sulfide ore and copper oxide ore, which exist in the glass body, and some are wrapped by gangue minerals. The beneficiation method of carrying out flotation recovery copper to this mineral is as follows:
[0045] (1) Grind 500g of high-temperature slag, the fineness of which is less than 0.074 mm, accounting for about 90%, inject it into the flotation machine and adjust the pulp concentration to about 35%;
[0046] (2) Add NaOH to adjust the pH value of the pulp to about 9. Add 500 g / t of sodium sulfite and sodium sulfide with a mass ratio of 2:3, 100 g / t of thiocarbamate, and 20 g / t of terpineol oil, and soak for 6 minutes to obtain roughing concentrate and roughing tailings respectively;
[0047] (3) Add 50g / t of thiocarbamate and 10g / t of terpineol oil to the roughing tailings, scrape and foam to obtain a scavenging tailings and a scavenging ...
Embodiment 2
[0052] The grade of copper in the smelting slag of a smelting furnace in a smelter is 0.83%. The beneficiation method for flotation of this mineral to recover copper is as follows:
[0053] (1) Grind 500g of high-temperature slag, the fineness of which is less than 0.074 mm, accounting for about 90%, inject it into the flotation machine and adjust the pulp concentration to about 35%;
[0054] (2) Add sodium carbonate to adjust the pH value of the pulp to around 9. Add 600g / t of sodium thiosulfate and sodium hydrosulfide with a mass ratio of 1:5, 150g / t of butyl xanthate, 15g / t of terpineol oil, and soak for 6 minutes to obtain roughing concentrate and roughing tailings respectively ;
[0055] (3) Add 75g / t of butyl xanthate and 7.5g / t of terpineol oil to the roughing tailings, scrape and foam to obtain a scavenging tailings and a scavenging concentrate, and a scavenging concentrate returns to the roughing step to form a closed loop ;
[0056] (4) Add 37.5g / t of butyl xantha...
Embodiment 3
[0060] The grade of copper in the shaft furnace smelting slag of a certain smelter is 2.05%. The beneficiation method for flotation of this mineral to recover copper is as follows:
[0061] (1) Grind 500g of high-temperature slag, the fineness of which is less than 0.074 mm, accounting for about 90%, inject it into the flotation machine and adjust the pulp concentration to about 35%;
[0062] (2) Add calcium hydroxide to adjust the pH value of the pulp to about 9. Add 770g / t of sodium lignosulfonate and sodium hydrosulfide with a mass ratio of 1:10, 120g / t of ethionate and butyl xanthate with a mass ratio of 1:1, 20g / t of pinitol oil, and scrape for 6 Minutes to obtain roughing concentrate and roughing tailings respectively;
[0063] (3) Add 60 g / t of thiocarbamate and butyl xanthate with a mass ratio of 1:1 to the roughing tailings, 10 g / t of terpineol oil, and scrape and foam to obtain a scavenging tailings and a scavenging concentrate. The sweeping concentrate returns to ...
PUM
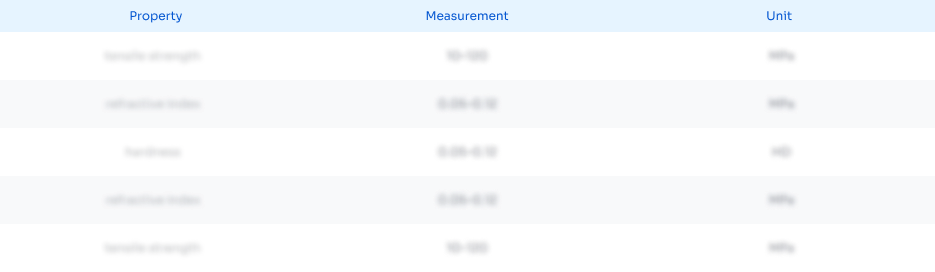
Abstract
Description
Claims
Application Information

- Generate Ideas
- Intellectual Property
- Life Sciences
- Materials
- Tech Scout
- Unparalleled Data Quality
- Higher Quality Content
- 60% Fewer Hallucinations
Browse by: Latest US Patents, China's latest patents, Technical Efficacy Thesaurus, Application Domain, Technology Topic, Popular Technical Reports.
© 2025 PatSnap. All rights reserved.Legal|Privacy policy|Modern Slavery Act Transparency Statement|Sitemap|About US| Contact US: help@patsnap.com