A low-cost method for preparing gallium nitride crystals
A gallium nitride, low-cost technology, applied in the direction of chemical instruments and methods, crystal growth, from chemically reactive gases, etc., can solve the problems of long cycle, reduced crystal quality, low safety factor, etc., to achieve increased reaction rate, reaction The effect of lowering the temperature and lowering the reaction temperature
- Summary
- Abstract
- Description
- Claims
- Application Information
AI Technical Summary
Problems solved by technology
Method used
Examples
Embodiment 1
[0024] (1) Grinding 50 parts by weight of sodium montmorillonite and 50 parts by weight of hectorite, passing through a 200-1000 mesh sieve, and set aside;
[0025] (2) Prepare 1 part by weight of alkyl polyoxyethylene ether into aqueous solution A with a mass fraction of 20%; prepare 5 parts by weight of sodium edetate into aqueous solution B with a mass fraction of 15%;
[0026] (3) Add the inorganic layered minerals ground in step (1) into aqueous solution A, stir and mix in a mixer at a speed of 3000 rpm for 5 h at room temperature, filter, and wash until no surfactant is precipitated to obtain modified Inorganic layered minerals; then add the modified inorganic layered minerals into aqueous solution B, stir and mix in a mixer at a speed of 800 rpm for 2 h at room temperature, filter and wash to obtain organically modified inorganic layered minerals, and wait for use;
[0027] (4) Put the organically modified inorganic layered minerals obtained in step (3) into a reaction...
Embodiment 2
[0031](1) Grind 100 parts by weight of expanded vermiculite, pass through a 200-1000 mesh sieve, and set aside;
[0032] (2) 1 part by weight of fatty alcohol polyoxyethylene ether is formulated into an aqueous solution A with a mass fraction of 20%; 10 parts by weight of sodium edetate is formulated into an aqueous solution B with a mass fraction of 20%;
[0033] (3) Add the inorganic layered minerals ground in step (1) into aqueous solution A, stir and mix in a mixer at a speed of 3000 rpm for 8 h at room temperature, filter, and wash until no surfactant is precipitated to obtain modified Inorganic layered minerals; then add the modified inorganic layered minerals into the aqueous solution B, stir and mix in a mixer at a speed of 1000 rpm for 1 h at room temperature, filter and wash to obtain organically modified inorganic layered minerals, and wait for use;
[0034] (4) Put the organically modified inorganic layered minerals obtained in step (3) into a reaction kettle and ...
Embodiment 3
[0038] (1) Grind 100 parts by weight of palygorskite, pass through a 200-1000 mesh sieve, and set aside;
[0039] (2) 5 parts by weight of fatty acid polyoxyethylene esters are formulated into an aqueous solution A with a mass fraction of 30%; 10 parts by weight of sodium edetate are formulated into an aqueous solution B with a mass fraction of 25%;
[0040] (3) Add the inorganic layered minerals ground in step (1) into aqueous solution A, stir and mix in a mixer at a speed of 1000 rpm for 10 h at room temperature, filter, wash until no surfactant is precipitated, and obtain modified Inorganic layered minerals; then add the modified inorganic layered minerals into aqueous solution B, stir and mix in a mixer at a speed of 800 rpm for 2 h at room temperature, filter and wash to obtain organically modified inorganic layered minerals, and wait for use;
[0041] (4) Put the organically modified inorganic layered minerals obtained in step (3) into a reaction kettle and add water to...
PUM
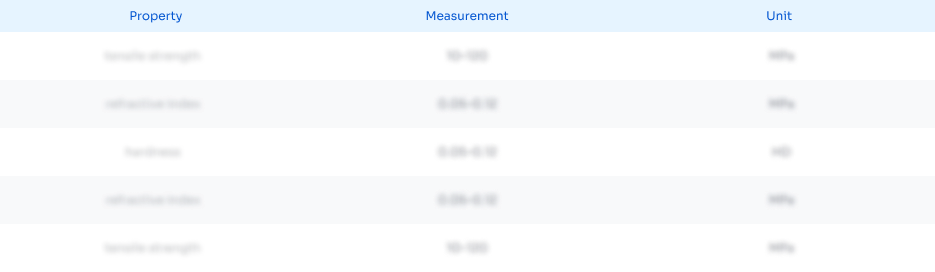
Abstract
Description
Claims
Application Information

- R&D
- Intellectual Property
- Life Sciences
- Materials
- Tech Scout
- Unparalleled Data Quality
- Higher Quality Content
- 60% Fewer Hallucinations
Browse by: Latest US Patents, China's latest patents, Technical Efficacy Thesaurus, Application Domain, Technology Topic, Popular Technical Reports.
© 2025 PatSnap. All rights reserved.Legal|Privacy policy|Modern Slavery Act Transparency Statement|Sitemap|About US| Contact US: help@patsnap.com