Preparation method for hollow microspheres
A hollow microsphere and spherical technology, which is applied in the field of preparation of hollow microspheres, can solve the problems of difficult control of product quality, single preparation method, and difficulty in the thickness of the microsphere shell, and achieve the effect of easy industrial production and simple preparation process
- Summary
- Abstract
- Description
- Claims
- Application Information
AI Technical Summary
Problems solved by technology
Method used
Examples
preparation example Construction
[0024] The embodiment of the present invention provides a method for preparing hollow microspheres, which is a general method for preparing composite hollow microspheres of metals and their oxides. The method includes:
[0025] Spherical alloy powder A x B (1-x) As raw materials, A and B components are metals, A component can use: a combination of one or more metals in lithium, sodium, potassium, magnesium, calcium, strontium, barium, zinc, cadmium, B component Available: magnesium, calcium, strontium, barium, titanium, zirconium, molybdenum, cobalt, tantalum, manganese, iron, nickel, palladium, copper, silver, platinum, zinc, cadmium, aluminum, silicon, gallium, indium, germanium, tin , lead, bismuth, lanthanum, cerium, praseodymium, neodymium, samarium, europium, gadolinium, terbium, dysprosium, holmium, erbium, thulium, ytterbium, lutetium, and the B component is not limited to these Metals, such as tungsten, vanadium, ruthenium are also all possible; 0.4≤xx B (1-x) Calc...
Embodiment 1
[0036] The embodiment of the present invention provides a method for preparing composite hollow microspheres of metals and their oxides, which is a method for preparing composite hollow microspheres of aluminum, aluminum oxide and zinc oxide, which specifically includes the following steps:
[0037] Prepared by atomization method: the component is Zn 0.93 al 0.07 The spherical zinc-aluminum alloy powder is used as the precursor, and 4g of the above raw materials (Zn 0.93 al 0.07 ) on the bottom of the corundum crucible, after high temperature oxidation treatment at 200°C for 5 minutes, transfer to the muffle furnace, calcined at 950°C for 1 hour, take out the crucible, cool to room temperature naturally, and separate the white zinc oxide whiskers on the upper part , metal aluminum and Al can be obtained at the bottom of the crucible 2 o 3 and ZnO composite hollow microspheres. Moreover, the by-product zinc oxide whisker in this embodiment is also a high-performance materi...
Embodiment 2
[0039] The embodiment of the present invention provides a method for preparing metal hollow microspheres, which is a method for preparing nickel hollow microspheres, which specifically includes the following steps:
[0040] Prepared by atomization method: the component is Zn 0.89 Ni 0.11 The spherical zinc-nickel alloy powder is used as the precursor, and 5g of the above raw materials (Zn 0.89 Ni 0.11 ) on the bottom of the corundum crucible, oxidized at 200°C for 5min, then transferred to a muffle furnace, calcined at 1500°C for 1h, took out the crucible, cooled naturally to room temperature, and separated the white zinc oxide whiskers on the upper part. Metal nickel hollow microspheres containing a small amount of zinc oxide can be obtained at the bottom of the crucible;
[0041] The hollow microsphere material prepared by the above method is placed in a 30% NaOH aqueous solution, soaked for 1 hour, filtered and dried to obtain metallic Ni hollow microspheres.
PUM
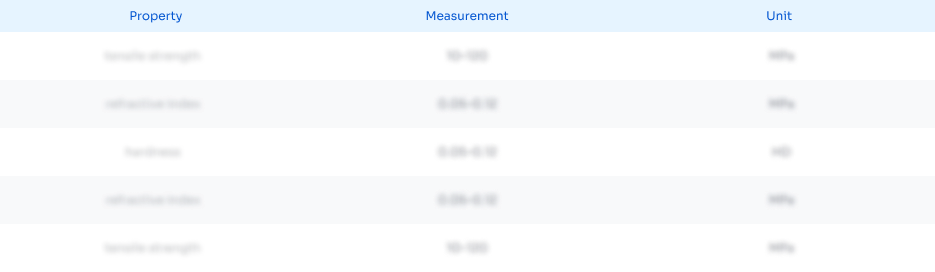
Abstract
Description
Claims
Application Information

- R&D
- Intellectual Property
- Life Sciences
- Materials
- Tech Scout
- Unparalleled Data Quality
- Higher Quality Content
- 60% Fewer Hallucinations
Browse by: Latest US Patents, China's latest patents, Technical Efficacy Thesaurus, Application Domain, Technology Topic, Popular Technical Reports.
© 2025 PatSnap. All rights reserved.Legal|Privacy policy|Modern Slavery Act Transparency Statement|Sitemap|About US| Contact US: help@patsnap.com