Manufacturing process of hard alloy replaceable tool
A cemented carbide and manufacturing process technology, applied in the field of tool manufacturing, can solve the problems of complex production process, low cutting finish, waste of raw materials, etc., and achieve the effect of simple process, good toughness, and reduced danger and pollution
- Summary
- Abstract
- Description
- Claims
- Application Information
AI Technical Summary
Problems solved by technology
Method used
Image
Examples
Embodiment 1
[0025] A manufacturing process of a cemented carbide replaceable tool, comprising the following steps:
[0026] (1) Prepare raw materials: 60 parts of tungsten carbide, 10 parts of tungsten boride, 6 parts of vanadium pentoxide, 4 parts of chromium powder, 3 parts of cobalt powder, 2.5 parts of nickel powder, 1.7 parts of rhenium powder, 2.5 parts of zirconium dioxide, titanium dioxide 1.5 parts, 4 parts of triglyceride vegetable oil, 2.5 parts of rubber powder, 1.5 parts of surfactant;
[0027] (2) Add the above-mentioned raw materials into a stirring ball mill, and add 200 parts of absolute ethanol, and stir and grind for 4 hours to obtain a slurry;
[0028] (3) The above-mentioned slurry is dried and sieved, then 50 parts of fully refined paraffin wax is added and fully stirred to obtain material granules, and then 4.5 parts of zinc stearate are added to the material granules to carry out molding, extrusion, and injection molding;
[0029] (4) Place the formed blank in a v...
Embodiment 2
[0032] A manufacturing process of a cemented carbide replaceable tool, comprising the following steps:
[0033] (1) Prepare raw materials: 62 parts of tungsten carbide, 11 parts of tungsten boride, 7 parts of vanadium pentoxide, 5 parts of chromium powder, 3 parts of cobalt powder, 2.6 parts of nickel powder, 1.7 parts of rhenium powder, 2.8 parts of zirconium dioxide, titanium dioxide 1.7 parts, 4 parts of triglyceride vegetable oil, 2.9 parts of rubber powder, 1.8 parts of surfactant;
[0034] (2) Add the above raw materials into a stirring ball mill, and add 210 parts of absolute ethanol, and stir and grind for 4 hours to obtain a slurry;
[0035] (3) The above-mentioned slurry is dried and sieved, and then 52 parts of fully refined paraffin wax are added and fully stirred to obtain pellets, which are then molded, extruded, and injection molded after adding 4.8 parts of zinc stearate to the pellets;
[0036] (4) Place the formed blank in a vacuum sintering integrated furna...
Embodiment 3
[0039] A manufacturing process of a cemented carbide replaceable tool, comprising the following steps:
[0040] (1) Prepare raw materials: 65 parts of tungsten carbide, 13 parts of tungsten boride, 7 parts of vanadium pentoxide, 5 parts of chromium powder, 4 parts of cobalt powder, 2.7 parts of nickel powder, 1.7 parts of rhenium powder, 2.9 parts of zirconium dioxide, titanium dioxide 1.7 parts, 6 parts of triglyceride vegetable oil, 4 parts of rubber powder, 1.6 parts of surfactant;
[0041] (2) Add the above-mentioned raw materials into a stirring ball mill, and add 220 parts of absolute ethanol, and stir and grind for 4 hours to obtain a slurry;
[0042] (3) The above-mentioned slurry is dried and sieved, then 55 parts of fully refined paraffin wax are added and fully stirred to obtain material granules, and then 5.2 parts of zinc stearate are added to the material granules to carry out molding, extrusion, and injection molding;
[0043] (4) Place the formed blank in a va...
PUM
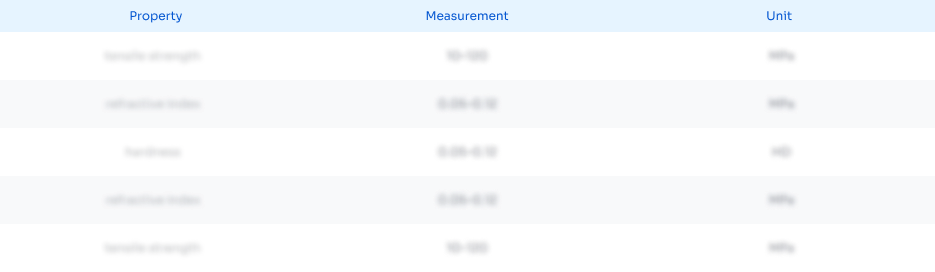
Abstract
Description
Claims
Application Information

- R&D
- Intellectual Property
- Life Sciences
- Materials
- Tech Scout
- Unparalleled Data Quality
- Higher Quality Content
- 60% Fewer Hallucinations
Browse by: Latest US Patents, China's latest patents, Technical Efficacy Thesaurus, Application Domain, Technology Topic, Popular Technical Reports.
© 2025 PatSnap. All rights reserved.Legal|Privacy policy|Modern Slavery Act Transparency Statement|Sitemap|About US| Contact US: help@patsnap.com