Preparation method of colored zirconia ceramics
A technology of zirconia ceramics and zirconia powder, which is applied in the field of preparation of doped ceramic materials, can solve the problems of increased preparation cost, poor repeatability, and limited application range, and achieves obvious mixing effect, uniform and stable color, and widened The effect of the field of application
- Summary
- Abstract
- Description
- Claims
- Application Information
AI Technical Summary
Problems solved by technology
Method used
Examples
Embodiment 1
[0030] In this embodiment, yttrium-stabilized zirconia powder with an average particle size of 500nm is used as raw material, and 100 grams of yttrium-stabilized zirconia powder is taken and dispersed in 300 ml of water by stirring to form a stable suspension; 1.2 g of magnesium chloride is dissolved in water Prepare 15ml of magnesium chloride aqueous solution, and slowly add it dropwise to the suspension of zirconia powder; then use 1mol / L sodium hydroxide solution to adjust the pH of the solution to 10; then add 30ml containing 0.8g of nickel sulfate and 0.3g of chromium chloride aqueous solution, mixed uniformly;
[0031] After filtering the above solution, put the powder in a drying oven and dry it at 80°C, then grind the dried powder finely with a mortar, and pass through an 80-mesh sieve; add 10ml of 4% poly Vinyl alcohol solution, granulated and passed through a 60-mesh sieve, and pressed into discs with a dry press. Keep warm at 350°C for 2 hours to remove the binder ...
Embodiment 2
[0033] In this example, yttrium-stabilized zirconia powder with an average particle size of 600nm is used as raw material, and 100 grams of yttrium-stabilized zirconia powder is taken and dispersed in 300 ml of aqueous solution by stirring to form a stable suspension; 1.5 g of aluminum nitrate is dissolved in Make 15ml aluminum nitrate aqueous solution in water, slowly add it dropwise to the suspension of zirconia powder, then adjust the pH value of the solution to 9.5 with 1mol / L ammonium bicarbonate solution, then add 40ml containing 0.7g cobalt sulfate, 0.4g An aqueous solution of chromium nitrate and 0.5g manganese chloride;
[0034] After filtering the above solution, put the powder in a drying oven and dry it at 80°C, then grind the dried powder finely with a mortar, and pass through an 80-mesh sieve; add 10ml of 4% poly Vinyl alcohol solution, granulated through a 60-mesh sieve, and pressed into discs with a dry press. Insulate at 350°C for 2 hours to remove the binder...
Embodiment 3
[0036] In this example, cerium-stabilized zirconia powder with an average particle size of 400nm is used as a raw material. Take 100 grams of cerium-stabilized zirconia powder and disperse it in 300 ml of aqueous solution by stirring to form a stable suspension. Then add 1.2 g of aluminum nitrate Dissolve in water to make 15ml aluminum nitrate aqueous solution, slowly add dropwise to the suspension of zirconia powder, adjust the pH value of the solution to 9.5 with 1mol / L sodium hydroxide solution, then add 30ml containing 1.2g tin sulfate and 1.5g The aqueous solution of ferric chloride, in order to better precipitate tin ions, then add 20ml 0.1mol / L ammonium sulfide solution and 20ml 0.5mol / L ammonia water to the solution dropwise to ensure that the pH value is stable at around 9.5.
[0037] After filtering the above solution, put the powder in a drying oven and dry it at 80°C, then use a mortar to grind the dried powder finely, pass through a 80-mesh sieve; add 10m14% polyethy...
PUM
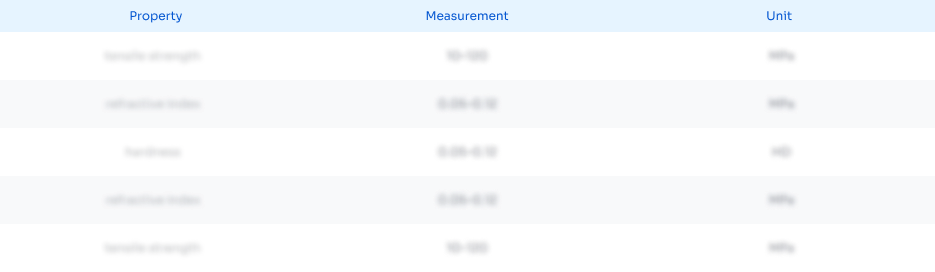
Abstract
Description
Claims
Application Information

- R&D
- Intellectual Property
- Life Sciences
- Materials
- Tech Scout
- Unparalleled Data Quality
- Higher Quality Content
- 60% Fewer Hallucinations
Browse by: Latest US Patents, China's latest patents, Technical Efficacy Thesaurus, Application Domain, Technology Topic, Popular Technical Reports.
© 2025 PatSnap. All rights reserved.Legal|Privacy policy|Modern Slavery Act Transparency Statement|Sitemap|About US| Contact US: help@patsnap.com