One-step acid washing activating plating pre-processing technique for magnesium alloy surface
A technology of pickling activation and treatment process, applied in hot dip plating process, metal material coating process, liquid chemical plating and other directions, can solve the problems of high waste liquid treatment cost, complicated and complicated process, etc. Simplify the process flow and improve the effect of economic benefits
- Summary
- Abstract
- Description
- Claims
- Application Information
AI Technical Summary
Problems solved by technology
Method used
Examples
Embodiment 1
[0037] The test material is AZ91D magnesium alloy
[0038] 1. Polishing
[0039] Grind the AZ91D magnesium alloy sample with a polishing machine or use a 300 # , 600 # , 1500 # Sandpaper for manual grinding, washing.
[0040] 2. Ultrasonic degreasing
[0041] Put the sample into a container filled with acetone, and then put the container together with the ultrasonic cleaner at room temperature
[0042] Wash for 10 minutes.
[0043] 3. Alkaline washing and degreasing
[0044] The sample was taken out and washed three times with tap water, and further degreased with alkaline solution. The components of the alkaline solution are listed as follows: Sodium hydroxide: 50g dm -3 , sodium phosphate: 10g·dm -3 , and the balance is water, wash with alkali at 75°C for 8 minutes.
[0045] 4. One-step pickling activation
[0046] Take the sample out and wash it three times with tap water and then with distilled water, then put it into the pickling activation solution for picklin...
Embodiment 2
[0062] Mechanical grinding and polishing→ultrasonic degreasing→alkaline cleaning and degreasing→one-step pickling activation→zinc dipping→pre-nickel plating. The one-step pickling activation solution is: sodium phosphate: 32g dm -3 , Potassium permanganate: 15g·dm -3 , zinc sulfate 1g·dm -3 , Phosphoric acid: 31g·dm -3 , solution pH 6.0, room temperature, time: 3min. The test pretreatment steps before pre-nickel plating are the same as in Example 1, and the test results are shown in Table 2.
Embodiment 3
[0064] Mechanical grinding and polishing→ultrasonic degreasing→alkaline cleaning and degreasing→one-step pickling activation→zinc dipping→pre-nickel plating. The one-step pickling activation solution is: sodium phosphate: 43g dm -3 , Potassium permanganate: 20g·dm -3 , zinc sulfate: 0.5g·dm -3 , Phosphoric acid: 41g·dm -3 , solution pH 5, room temperature, time: 3min. Other pretreatment steps of the test are the same as in Example 1, and the test results are shown in Table 2.
PUM
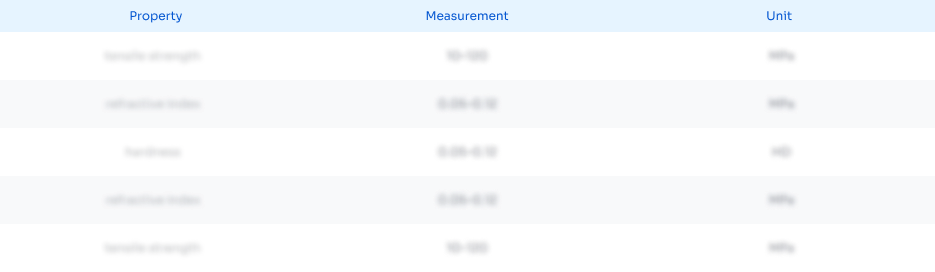
Abstract
Description
Claims
Application Information

- R&D
- Intellectual Property
- Life Sciences
- Materials
- Tech Scout
- Unparalleled Data Quality
- Higher Quality Content
- 60% Fewer Hallucinations
Browse by: Latest US Patents, China's latest patents, Technical Efficacy Thesaurus, Application Domain, Technology Topic, Popular Technical Reports.
© 2025 PatSnap. All rights reserved.Legal|Privacy policy|Modern Slavery Act Transparency Statement|Sitemap|About US| Contact US: help@patsnap.com