Foam aluminum metallurgy connecting method
A metallurgical connection and foamed aluminum technology, applied in welding equipment, metal processing equipment, non-electric welding equipment, etc., can solve the problems of complex operation, insufficient bonding strength, and difficulty in eliminating mutual infiltration of brazing materials, so as to achieve a simple and reliable process, suitable for Effects of engineering and scale processing
- Summary
- Abstract
- Description
- Claims
- Application Information
AI Technical Summary
Problems solved by technology
Method used
Examples
Embodiment 1
[0024] A metallurgical connection method for aluminum foam, specifically comprising the following steps:
[0025] (1) Remove the oxide layer of the foamed aluminum butt joint or lap joint surface by mechanical grinding (grinding with sandpaper), and increase the surface roughness;
[0026] (2) Place the foamed aluminum to be connected in the zinc-aluminum alloy melt for immersion plating, and form a uniform immersion coating on the butt joint or overlapping surface of the foamed aluminum. The zinc-aluminum alloy is a zinc-aluminum alloy with an aluminum mass fraction of 5%. It also contains trace amounts of Cu, Ag and other alloying elements;
[0027] (3) Lay the galvanized foamed aluminum butt joints or overlapping surfaces together, and hot press. The hot pressing conditions are: electric heating to 20°C above the melting point of the zinc-aluminum alloy, and applying a pressure of 0.05 MPa and holding the pressure for 3 minutes. Ultrasonic vibration is applied for 1 minute...
Embodiment 2
[0029] A metallurgical connection method for aluminum foam, specifically comprising the following steps:
[0030] (1) Remove the oxide layer of the foamed aluminum butt joint or lap joint surface by chemical method (pickling), and increase the surface roughness;
[0031] (2) Place the foamed aluminum to be connected in the zinc-aluminum alloy melt for immersion plating, and form a uniform immersion coating on the butt joint or overlapping surface of the foamed aluminum. The zinc-aluminum alloy is a zinc-aluminum alloy with an aluminum mass fraction of 15%. It also contains trace amounts of Cu, Ag and other alloying elements;
[0032] (3) Lay the butt joint or overlapping surface of the dipped aluminum foam and hot press. The hot pressing conditions are: the flame is heated to 50°C above the melting point of the zinc-aluminum alloy, and a pressure of 0.15 MPa is applied and kept for 20 minutes. Ultrasonic vibration is applied for 3 minutes during the hot pressing process, whic...
Embodiment 3
[0034] A metallurgical connection method for aluminum foam, specifically comprising the following steps:
[0035] (1) Remove the oxide layer of the foamed aluminum butt or overlapping surface by mechanical grinding (grinding with steel balls), and increase the surface roughness;
[0036] (2) Place the foamed aluminum to be connected in the zinc-aluminum alloy melt for immersion plating, and form a uniform immersion coating on the butt joint or overlapping surface of the foamed aluminum. The zinc-aluminum alloy is a zinc-aluminum alloy with an aluminum mass fraction of 35%. It also contains trace amounts of Cu, Ag and other alloying elements;
[0037] (3) Lay the butt joint or overlapping surface of the galvanized aluminum foam, hot press, and the hot pressing conditions are: induction heating to 80°C above the melting point of the zinc-aluminum alloy, and applying a pressure of 0.2 MPa and holding the pressure for 25 minutes. High-frequency vibration is applied for 5 minutes ...
PUM
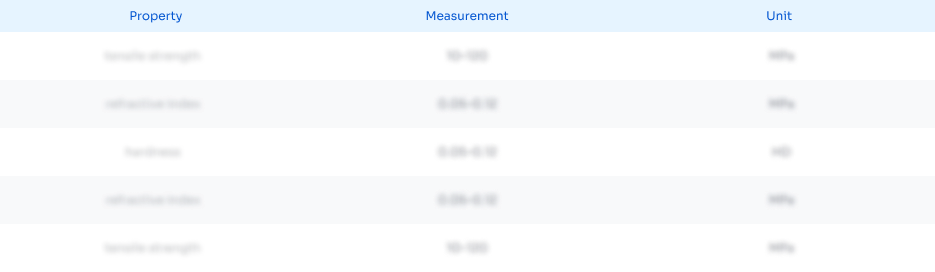
Abstract
Description
Claims
Application Information

- R&D Engineer
- R&D Manager
- IP Professional
- Industry Leading Data Capabilities
- Powerful AI technology
- Patent DNA Extraction
Browse by: Latest US Patents, China's latest patents, Technical Efficacy Thesaurus, Application Domain, Technology Topic, Popular Technical Reports.
© 2024 PatSnap. All rights reserved.Legal|Privacy policy|Modern Slavery Act Transparency Statement|Sitemap|About US| Contact US: help@patsnap.com