Palladium mesh alloy wire without plating thereon and method for manufacturing the same
A manufacturing method and alloy wire technology, which are applied in semiconductor/solid-state device manufacturing, semiconductor/solid-state device parts, semiconductor devices, etc., can solve the problems of insufficient neck strength above solder balls, unstable flow, and increased manufacturing costs, etc. Achieve the best fusing current density and anti-oxidation effect, and reduce the effect of wire metallurgical segregation
- Summary
- Abstract
- Description
- Claims
- Application Information
AI Technical Summary
Problems solved by technology
Method used
Image
Examples
Embodiment Construction
[0015] The purpose of the present invention and its structural and functional advantages will be described with specific embodiments according to the following drawings, so as to have a more in-depth and specific understanding of the present invention.
[0016] At first, the non-plated palladium mesh alloy wire of the present invention is applicable to the package wire of the electronic industry parts such as IC package, LED package; Its manufacturing method of specific embodiment 1 is to plate the palladium layer of 5nm-120nm thickness on the surface of a silver baseline Afterwards, it is heated to a temperature of 600-800° C., and the temperature is continued for at most 4 hours, so that the palladium element is completely thermally diffused into the silver baseline grain boundary grid, thereby forming a palladium-containing grain boundary zone, so that the non-coated palladium of the present invention Mesh alloy wire is composed of silver base and palladium-containing grid g...
PUM
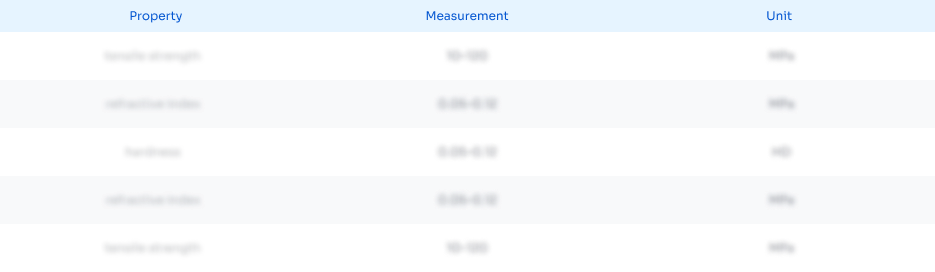
Abstract
Description
Claims
Application Information

- R&D Engineer
- R&D Manager
- IP Professional
- Industry Leading Data Capabilities
- Powerful AI technology
- Patent DNA Extraction
Browse by: Latest US Patents, China's latest patents, Technical Efficacy Thesaurus, Application Domain, Technology Topic, Popular Technical Reports.
© 2024 PatSnap. All rights reserved.Legal|Privacy policy|Modern Slavery Act Transparency Statement|Sitemap|About US| Contact US: help@patsnap.com