Ion implantation combined with in situ or ex situ heat treatment for improved field effect transistors
a field effect transistor and heat treatment technology, applied in the field of complementary metal oxide semiconductor (cmos) circuits, can solve the problems of increasing difficulty in maintaining trend, difficult to implant the desired concentration of certain dopant species in the s/d region without amorphizing the entire soi layer, and high defect in s/d recrystallization, so as to avoid or reduce ion implant-induced amorphization and ion implant-induced plastic relaxation
- Summary
- Abstract
- Description
- Claims
- Application Information
AI Technical Summary
Benefits of technology
Problems solved by technology
Method used
Image
Examples
example 1
[0080] The example shows that in situ heating during ion implantation can prevent the amorphization of SOI layers that would occur if the same implants were performed at room temperature. SOI layers 28 nm in thickness were implanted at 26, 150, or 300° C. with 3×1015 / cm2 50 keV As+, an implant that has an average projected range (Rp) of about 340 Å and would ordinarily completely amorphize the SOI layer. The reflectance vs. wavelength data of FIG. 6 indicates that the SOI layer has indeed been amorphized in the 26 and 150° C. samples (curves B and C, respectively), but remains crystalline (with a reflectance curve nearly identical to curve A of the unimplanted control sample) for the 300° C. implant (curve D). The sheet resistance (Rs) measurements of Table I corroborate these results: after annealing in N2 at 900° C. for 1 min, the 26 and 150° C. samples have Rs in the range of 8-11 kohm / square, consistent with a recrystallization of the amorphous SOI layer to polycrystalline Si; i...
example 2
[0082] In the second example; we show how one may use the dependence of amorphization depth on implant dose to calculate an optimum implementation of the DDAB technique in a semiconductor-on-insulator layer disposed on a buried oxide (box). SOI layers 160 nm in thickness were implanted at room temperature with 100 keV As+ (Rp about 71 nm) at doses of 1.25, 2.5, and 5.0×1015 / cm2 to produce surface amorphous layers having thicknesses of 91, 111, and 117 nm respectively. None of these doses were sufficient to amorphize the entire 160 nm thickness of the SOI layer. However, SOI layers thinner than about 110 nm in thickness would be expected to totally amorphize at doses higher than 2.5×1015 / cm2, form polycrystalline Si upon activation annealing. Dividing the 2.5×1015 / cm2 dose into two doses of 1.25×1015 / cm2 would leave a residual crystalline layer between the 91 nm amorphization depth and the top of the box after each implant. Annealing between the implants allows the crystallinity of t...
example 3
[0083] In the third example, we show how the hot implant and DDAB techniques may be used to preserve the strain in pseudomorphic SiGe layers grown on Si. FIGS. 7-9 show high resolution x-ray diffraction (HRXR-D) (004) rocking curves (RCs) of a structure comprised by 40-nm-thick Si0.70Ge03.0 layers epitaxially grown on (100) Si substrate, taken before and after implantation with As+ to a dose below the amorphization threshold dose. In FIGS. 7-9, the ordinate represents the intensity of diffracted x-ray in counts / second and the abscissa represents delta rocking angle omega in unity of seconds of degree, having the scale origin set at the Si substrate diffraction peak. The SiGe peak (at negative angles in FIGS. 7-9) typically comprises a main peak bordered by weaker satellite peaks (thickness fringes or Pendellosung oscillations) whose spacing allows a precise estimate of the SiGe thickness. The intensities of the main peak and the satellite peaks are highest when the SiGe is perfectly...
PUM
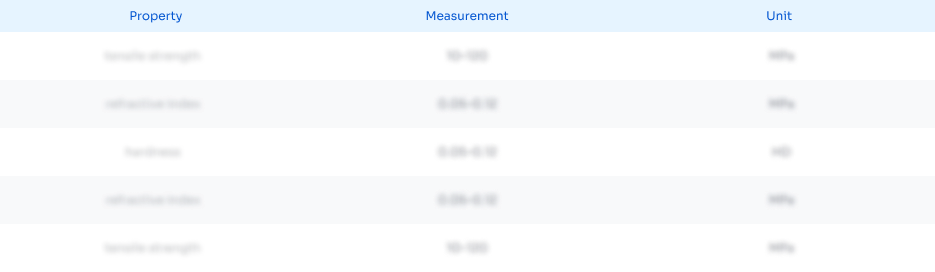
Abstract
Description
Claims
Application Information

- R&D
- Intellectual Property
- Life Sciences
- Materials
- Tech Scout
- Unparalleled Data Quality
- Higher Quality Content
- 60% Fewer Hallucinations
Browse by: Latest US Patents, China's latest patents, Technical Efficacy Thesaurus, Application Domain, Technology Topic, Popular Technical Reports.
© 2025 PatSnap. All rights reserved.Legal|Privacy policy|Modern Slavery Act Transparency Statement|Sitemap|About US| Contact US: help@patsnap.com