Composite manufacturing and stress releasing method for ceramic-coated cylinder sleeve of engine
A stress relief and cylinder liner technology, applied in the manufacture of tools, liquid chemical plating, furnaces, etc., can solve the problems of limited wear resistance and denaturation resistance, insufficient stability of the surface, poor lubrication conditions, etc., and achieve no cracks and peeling off of ceramics , improve lubricity, excellent comprehensive performance effect
- Summary
- Abstract
- Description
- Claims
- Application Information
AI Technical Summary
Problems solved by technology
Method used
Image
Examples
Embodiment
[0028] Step 1. Finish the pure copper with an outer diameter of 130mm, an inner diameter of 110mm, and a height of 145mm, and cooperate with the 38CrMoAl steel sleeve to reserve solder to fill the gap;
[0029] Step 2. Fill the silver-copper solder into the gap between the steel sleeve and the pure copper, and closely match the copper sleeve and the steel sleeve. After there is no obvious dislocation, put it in a vacuum furnace, and set a slow temperature rise curve (first, heat up at 10°C / min. to 680°C, keep warm for 30min; then raise the temperature to 860°C at 3°C / min), perform vacuum brazing at 860°C, keep warm for 20min, and then set a slow cooling curve (first cool down to 500°C at 2°C / min, Then air cool);
[0030] Step 3, finishing the workpiece welded in step 2, and thinning the copper layer to 0.8mm;
[0031] Step 4, after performing electroless nickel plating on silicon nitride ceramics;
[0032] Step 5. Put it into the steel sleeve, fill the gap with silver-copper...
Embodiment 2
[0035] Step 1. Finish the 4J29 Kovar alloy with an outer diameter of 130mm, an inner diameter of 110mm, and a height of 145mm, and cooperate with a 38CrMoAl steel sleeve to reserve solder to fill the gap;
[0036] Step 2. Fill the silver-copper solder into the gap between the steel sleeve and the Kovar alloy layer, and closely match the Kovar alloy layer and the steel sleeve. After there is no obvious dislocation, put it in a vacuum furnace, and set a slow temperature rise curve (first, 10 ℃ / min to 680°C, keep warm for 30min; then heat up to 880°C at 3°C / min), vacuum brazing at 880°C, keep warm for 25min, and then set a slow cooling curve (first cool down at 2°C / min to 500°C, then air cooled);
[0037] Step 3, finishing the workpiece welded in step 2, and thinning the Kovar alloy layer to 1 mm;
[0038] Step 4, after performing electroless nickel plating on silicon carbide ceramics;
[0039] Step 5. Put it into the steel sleeve, fill the gap with silver-copper-indium solder,...
PUM
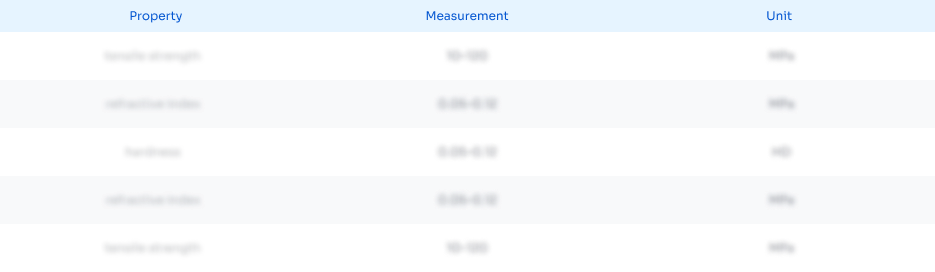
Abstract
Description
Claims
Application Information

- R&D Engineer
- R&D Manager
- IP Professional
- Industry Leading Data Capabilities
- Powerful AI technology
- Patent DNA Extraction
Browse by: Latest US Patents, China's latest patents, Technical Efficacy Thesaurus, Application Domain, Technology Topic, Popular Technical Reports.
© 2024 PatSnap. All rights reserved.Legal|Privacy policy|Modern Slavery Act Transparency Statement|Sitemap|About US| Contact US: help@patsnap.com