Metal ceramic composite material for brake pad of new energy automobile and preparation method thereof
A new energy vehicle, cermet technology, applied in the field of brake pad materials, can solve the problems of short service life, high wear rate, strong vibration, etc., achieve long service life, good wear resistance, and improve the effect of compression resistance
- Summary
- Abstract
- Description
- Claims
- Application Information
AI Technical Summary
Problems solved by technology
Method used
Image
Examples
Embodiment 1
[0034] A metal-ceramic composite material for new energy vehicle brake pads, comprising the following components in parts by weight:
[0035] 48 parts of alloy powder, 1.2 parts of titanium powder, 2.3 parts of zirconium diboride, 6 parts of titanium nitride, 10 parts of aluminum nitride, 8 parts of tungsten carbide, 6 parts of silicon carbide, 30 parts of aluminum trioxide, molybdenum disulfide 5 parts, 15 parts of graphene, 7 parts of modified acicular wollastonite, 4.6 parts of boron-cardanol modified phenolic resin, 5 parts of modified aramid fiber, 10 parts of long-chain silane coupling agent modified carbon fiber, poly 12 parts of oxyxylene, 6 parts of polystyrene, 40 parts of nitrile rubber powder, 30 parts of EPDM rubber powder, 12 parts of maleic anhydride grafted EPDM rubber.
[0036] The alloy powder includes the following elemental composition by weight:
[0037]Mn: 0.4%, Sn: 0.12%, Cu: 0.55%, Cr: 18.2%, Mo: 1.25%, Ni: 4%, Zn: 2.2%, Ta: 0.04%, C: 7.5%, Si: 4.8%, ...
Embodiment 2
[0043] A metal-ceramic composite material for new energy vehicle brake pads, comprising the following components in parts by weight:
[0044] 60 parts of alloy powder, 2.5 parts of titanium powder, 5 parts of zirconium diboride, 5.5 parts of titanium nitride, 8 parts of aluminum nitride, 5 parts of tungsten carbide, 6 parts of silicon carbide, 30 parts of aluminum oxide, molybdenum disulfide 5 parts, 13 parts of graphene, 8 parts of modified acicular wollastonite, 5 parts of boron-cardanol modified phenolic resin, 3 parts of modified aramid fiber, 6 parts of long-chain silane coupling agent modified carbon fiber, polymer 8 parts of oxyxylene, 6 parts of polystyrene, 45 parts of nitrile rubber powder, 20 parts of EPDM rubber powder, and 14 parts of maleic anhydride grafted EPDM rubber.
[0045] The alloy powder includes the following elemental composition by weight:
[0046] Mn: 0.2%, Sn: 0.26%, Cu: 0.4%, Cr: 18%, Mo: 0.8%, Ni: 2.5%, Zn: 3%, Ta: 0.04%, C: 6.5%, Si: 4.8%, Rare...
Embodiment 3
[0052] A metal-ceramic composite material for new energy vehicle brake pads, comprising the following components in parts by weight:
[0053] 55 parts of alloy powder, 1 part of titanium powder, 4 parts of zirconium diboride, 8 parts of titanium nitride, 6.5 parts of aluminum nitride, 8 parts of tungsten carbide, 10 parts of silicon carbide, 25 parts of aluminum oxide, molybdenum disulfide 4 parts, 15 parts of graphene, 10 parts of acicular wollastonite, 5 parts of boron-cardanol modified phenolic resin, 5 parts of modified aramid fiber, 8 parts of long-chain silane coupling agent modified carbon fiber, polyoxyethylene 15 parts of toluene, 10 parts of polystyrene, 30 parts of nitrile rubber powder, 26 parts of EPDM rubber powder, and 12 parts of maleic anhydride grafted EPDM rubber.
[0054] The alloy powder includes the following elemental composition by weight:
[0055] Mn: 0.5%, Sn: 0.16%, Cu: 0.4%, Cr: 20%, Mo: 1.3%, Ni: 4.5%, Zn: 1%, Ta: 0.05%, C: 6%, Si: 6.8%, Rare ear...
PUM
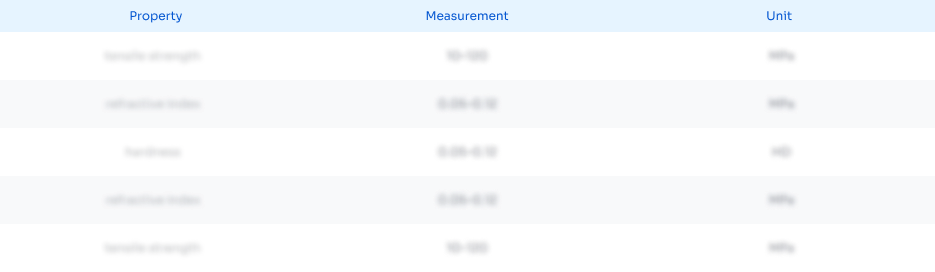
Abstract
Description
Claims
Application Information

- R&D
- Intellectual Property
- Life Sciences
- Materials
- Tech Scout
- Unparalleled Data Quality
- Higher Quality Content
- 60% Fewer Hallucinations
Browse by: Latest US Patents, China's latest patents, Technical Efficacy Thesaurus, Application Domain, Technology Topic, Popular Technical Reports.
© 2025 PatSnap. All rights reserved.Legal|Privacy policy|Modern Slavery Act Transparency Statement|Sitemap|About US| Contact US: help@patsnap.com