Manufacturing method for high-performance 12Cr2Mo1 forgings
A 12cr2mo1, manufacturing method technology, applied in the field of metallurgical manufacturing, can solve the problems that 12Cr2Mo1R steel cannot be explained, the low-temperature impact toughness of the material has not been studied, and the energy is not saved, so as to optimize the temperature and holding time, eliminate the influence of element segregation, and avoid grains The effect of growing up
- Summary
- Abstract
- Description
- Claims
- Application Information
AI Technical Summary
Problems solved by technology
Method used
Image
Examples
Embodiment 1
[0043] A method for manufacturing a high-performance 12Cr2Mo1 forging, comprising the steps of:
[0044] (1) Electric furnace smelting: adding pig iron, slag making, slag removal, molten pool stirring, dephosphorization and desulfurization to obtain molten steel;
[0045](2) Refining outside the furnace: refining and adjusting the chemical composition of the molten steel obtained in step (1), 0.12% of carbon element, 0.01% of silicon element, 0.50% of manganese element, 0.002% of phosphorus element, 0.001% of sulfur element, and 0.20% of nickel element %, molybdenum element 1.00%, and the content of other chemical components shall be determined according to NB / T47008-2017;
[0046] (3) Vacuum degassing: vacuum pumping, vacuum degree 20Pa, casting to obtain steel ingots;
[0047] (4) Forging: the heating and holding temperature of steel ingot is 1000℃, the forging ratio of steel ingot is 3.5, after the forging process is completed, 18% of the head of the steel ingot and 7% of ...
Embodiment 2
[0050] A method for manufacturing a high-performance 12Cr2Mo1 forging, comprising the steps of:
[0051] (1) Electric furnace smelting: adding ferromolybdenum alloy, slag making, slag removal, molten pool stirring, dephosphorization and desulfurization to obtain molten steel;
[0052] (2) Refining outside the furnace: refining and adjusting the chemical composition of the molten steel obtained in step (1), 0.15% of carbon element, 0.1% of silicon element, 0.60% of manganese element, 0.005% of phosphorus element, 0.003% of sulfur element, and 0.30% of nickel element %, molybdenum element 1.10%, and the content of other chemical components shall be determined according to NB / T47008-2017;
[0053] (3) Vacuum degassing: vacuum pumping, vacuum degree 29Pa, to obtain steel ingot forgings;
[0054] (4) Forging: Steel ingot heating and holding temperature is 1250°C, steel ingot forging ratio is 6, after the forging process is completed, the head of the steel ingot is cut off by 18%, ...
Embodiment 3
[0057] A method for manufacturing a high-performance 12Cr2Mo1 forging, comprising the steps of:
[0058] (1) Electric furnace smelting: adding ferrochromium, slag making, slag removal, molten pool stirring, dephosphorization and desulfurization to obtain molten steel;
[0059] (2) Refining outside the furnace: refining and adjusting the chemical composition of the molten steel obtained in step (1), 0.13% of carbon element, 0.05% of silicon element, 0.55% of manganese element, 0.003% of phosphorus element, 0.002% of sulfur element, and 0.25% of nickel element %, molybdenum element 1.05%, and the content of other chemical components shall be determined according to NB / T47008-2017;
[0060] (3) Vacuum degassing: vacuum pumping, vacuum degree 25Pa, to obtain steel ingot forgings;
[0061] (4) Blanking: Calculate the blanking weight according to blanking weight = forging volume × forging density + fire consumption + punching iron, wherein the fire consumption is calculated accordi...
PUM
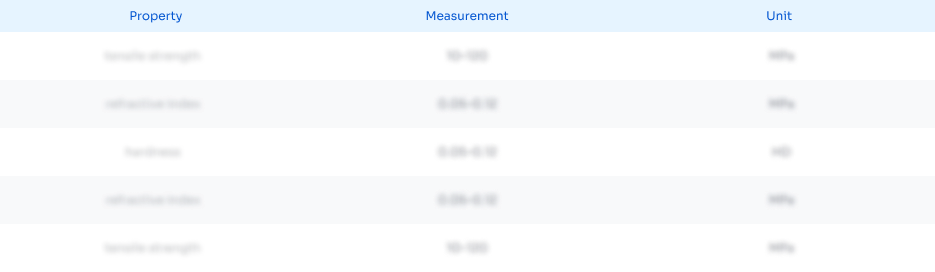
Abstract
Description
Claims
Application Information

- R&D
- Intellectual Property
- Life Sciences
- Materials
- Tech Scout
- Unparalleled Data Quality
- Higher Quality Content
- 60% Fewer Hallucinations
Browse by: Latest US Patents, China's latest patents, Technical Efficacy Thesaurus, Application Domain, Technology Topic, Popular Technical Reports.
© 2025 PatSnap. All rights reserved.Legal|Privacy policy|Modern Slavery Act Transparency Statement|Sitemap|About US| Contact US: help@patsnap.com