Preparation method of high-purity magnesium oxide
A magnesia, high-purity technology, applied in the direction of magnesia, can solve the problems of producing a large amount of carbon dioxide, high equipment requirements, low energy consumption, etc., and achieve the effects of reducing the generation of by-products, simplifying the production process, and reducing investment costs
- Summary
- Abstract
- Description
- Claims
- Application Information
AI Technical Summary
Problems solved by technology
Method used
Examples
Embodiment 1
[0033] In this example, a large-scale spray drying-heat-insulated rotary kiln is used to prepare magnesium oxide, and magnesium chloride solution is subjected to centrifugal spray drying and heat-insulated rotary kiln to obtain high-purity magnesium oxide products.
[0034] The preparation method of magnesium oxide comprises the following steps:
[0035] (1) 500g of bischofite is dissolved in distilled water to be mixed with a magnesium chloride solution with a mass fraction of 40%, and heated to 130°C;
[0036] (2) Pass the preheated solution through a centrifugal spray dryer, the air inlet temperature of the spray dryer is 650°C, the outlet air temperature is above 260°C, and the spray drying time is 20S;
[0037] (3) by secondary cyclone separator and secondary electrostatic precipitator, collect anhydrous magnesium chloride powder;
[0038] (4) The anhydrous magnesium chloride powder is fed into the heat-insulated rotary kiln by screw feeding, and water vapor is introduce...
Embodiment 2
[0041] In this embodiment, a large-scale spray drying-heat-insulated rotary kiln is used to prepare magnesium oxide. The magnesium chloride solution is subjected to centrifugal spray drying and heat-insulated rotary kiln to obtain high-purity magnesium oxide products.
[0042] The preparation method of magnesium oxide comprises the following steps:
[0043] (1) 500g of bischofite is dissolved in distilled water to prepare a magnesium chloride solution with a mass fraction of 40%, and heated to 140°C;
[0044] (2) Pass the preheated solution through a centrifugal spray dryer, the air inlet temperature of the spray dryer is 650°C, the outlet air temperature is above 260°C, and the spray drying time is 25S;
[0045] (3) by secondary cyclone separator and secondary electrostatic precipitator, collect anhydrous magnesium chloride powder;
[0046] (4) The anhydrous magnesium chloride powder is fed into the heat-insulated rotary kiln through screw feeding, and water vapor is introdu...
Embodiment 3
[0049] In this embodiment, a large-scale spray drying-heat-insulated rotary kiln is used to prepare magnesium oxide. The magnesium chloride solution is subjected to centrifugal spray drying and heat-insulated rotary kiln to obtain high-purity magnesium oxide products.
[0050] The preparation method of magnesium oxide comprises the following steps:
[0051] (1) 500g of bischofite is dissolved in distilled water to be mixed with a magnesium chloride solution with a mass fraction of 40%, and heated to 150°C;
[0052] (2) Pass the preheated solution through a centrifugal spray dryer, the air inlet temperature of the spray dryer is 650°C, the outlet air temperature is above 260°C, and the spray drying time is 40S;
[0053] (3) by secondary cyclone separator and secondary electrostatic precipitator, collect anhydrous magnesium chloride powder;
[0054] (4) Anhydrous magnesium chloride powder enters the heat-insulated rotary kiln through screw feeding, and feeds water vapor. The fr...
PUM
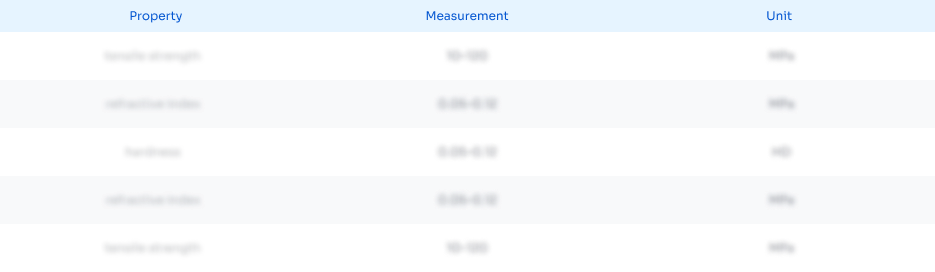
Abstract
Description
Claims
Application Information

- R&D
- Intellectual Property
- Life Sciences
- Materials
- Tech Scout
- Unparalleled Data Quality
- Higher Quality Content
- 60% Fewer Hallucinations
Browse by: Latest US Patents, China's latest patents, Technical Efficacy Thesaurus, Application Domain, Technology Topic, Popular Technical Reports.
© 2025 PatSnap. All rights reserved.Legal|Privacy policy|Modern Slavery Act Transparency Statement|Sitemap|About US| Contact US: help@patsnap.com