Water-repellent paper-surface plasterboard and preparation method thereof
A technology of paper-faced gypsum board and desulfurized gypsum powder, which is applied in the field of water-resistant paper-faced gypsum board and its preparation, can solve problems such as affecting environmental safety, increasing board weight, and difficulty in water-resistant boards, and achieves enhanced water resistance, increased stability, The effect of good temperature resistance
- Summary
- Abstract
- Description
- Claims
- Application Information
AI Technical Summary
Problems solved by technology
Method used
Examples
Embodiment 1
[0035] Step (1): Weigh each component of the emulsified wax ingredient according to the following ratio:
[0036] 100 parts by weight of paraffin wax, 8 parts by weight of microcrystalline wax, 5 parts by weight of sorbitan fatty acid ester, 1.5 parts by weight of sodium hydroxide, 10 parts by weight of polyvinyl alcohol, and 145 parts by weight of water.
[0037] Step (2): Preparation steps of emulsified wax:
[0038] Step a: heating paraffin wax and microcrystalline wax to a molten state and mixing them together;
[0039] Step b: Add emulsifier, stabilizer, and polyvinyl alcohol into hot water at 90°C, and add the blend of paraffin wax and microcrystalline wax into the colloid mill for emulsification, and then cool to room temperature to obtain stable emulsified wax .
[0040] Step (3): Preparation steps of plasterboard:
[0041] Weigh each component of the gypsum board ingredients according to the following proportions: 100 parts by weight of desulfurized gypsum powder (...
Embodiment 2
[0047] The preparation method of embodiment 2 is identical with the preparation method of embodiment 1, difference is:
[0048] Take by weighing each component of emulsified wax batching according to following proportioning:
[0049] 100 parts by weight of paraffin wax, 12 parts by weight of microcrystalline wax, 6 parts by weight of sodium abietate (an anionic surfactant with a triphenyl ring structure), 2.5 parts by weight of ammonia water, 12 parts by weight of polyvinyl alcohol, and 155 parts by weight of water.
[0050] The components of the gypsum board ingredients were weighed according to the following proportions: 100 parts by weight of desulfurized gypsum powder (same as above), 2.5 parts by weight of emulsified wax, 0.6 parts by weight of starch, 0.08 parts by weight of foaming agent, and 70 parts by weight of water. Then, prepare according to the preparation method of Example 1.
[0051]After testing, the water absorption rate of the prepared water-resistant paper...
Embodiment 3
[0053] The preparation method of embodiment 3 is basically the same as the preparation method of embodiment 1, and difference is:
[0054] Weigh each component of the emulsified wax batching according to the following proportions: 100 parts by weight of paraffin wax, 10 parts by weight of microcrystalline wax, 3 parts by weight of sorbitan fatty acid ester, 3 parts by weight of sodium rosinate, 2 parts by weight of ammonia water, poly 11 parts by weight of vinyl alcohol, and 150 parts by weight of water.
[0055] The components of the gypsum board ingredients were weighed according to the following proportions: 100 parts by weight of desulfurized gypsum powder (same as above), 2.5 parts by weight of emulsified wax, 0.6 parts by weight of starch, 0.08 parts by weight of foaming agent, and 70 parts by weight of water. Then, prepare according to the preparation method of Example 1.
[0056] After testing, the water absorption rate of the prepared water-resistant paper-faced gyps...
PUM
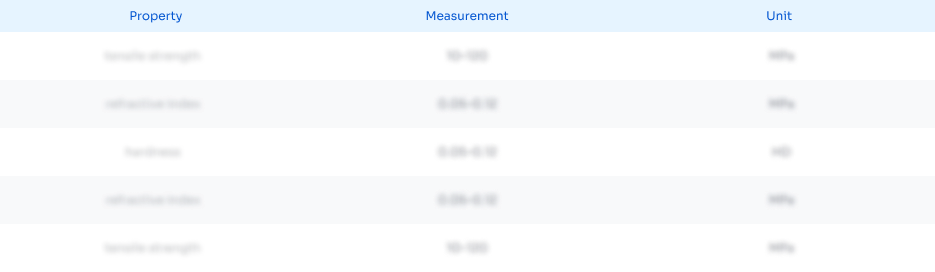
Abstract
Description
Claims
Application Information

- R&D Engineer
- R&D Manager
- IP Professional
- Industry Leading Data Capabilities
- Powerful AI technology
- Patent DNA Extraction
Browse by: Latest US Patents, China's latest patents, Technical Efficacy Thesaurus, Application Domain, Technology Topic, Popular Technical Reports.
© 2024 PatSnap. All rights reserved.Legal|Privacy policy|Modern Slavery Act Transparency Statement|Sitemap|About US| Contact US: help@patsnap.com