Process for producing cation polyacrylamide
A technology of polyacrylamide and production process, which is applied in the field of production process of cationic polyacrylamide, can solve the problems of increasing production cost and equipment investment cost, affecting product performance stability, complicated production control, etc., and achieves reduction of production cost and Equipment investment cost, deodorization and elimination of some harmful bacteria, and the effect of easy control of the reaction
- Summary
- Abstract
- Description
- Claims
- Application Information
AI Technical Summary
Problems solved by technology
Method used
Image
Examples
Embodiment 1
[0015] The raw materials of each raw material are calculated by mass percentage:
[0016] Acrylamide 10.0
[0017] Acryloyloxyethyltrimethylammonium chloride 5.05
[0018] Redox agent (potassium persulfate: trimethylamine=1:1) 0.4
[0019] Azobisisobutyronitrile 0.03
[0020] Urea 0.5
[0022] Deionized water 84.0
[0023] The operation steps are: add deionized water into the reactor, feed nitrogen gas until the oxygen saturation is ≤5%, add acrylamide, acryloyloxyethyltrimethylammonium chloride, urea and sodium formate in sequence, and adjust the pH value to 6.0, by injecting nitrogen and keeping the oxygen saturation ≤ 5%, add redox agent, react under nitrogen protection conditions for 43 minutes, then add azobisisobutyronitrile, continue to react for 60 minutes, then react again at 60°C After 4 hours, the copolymer colloid was obtained, cooled to room temperature, granulated, and dried at 60-70°C to obtain cationic polyacrylamide. Its per...
Embodiment 2
[0025] The raw materials of each raw material are calculated by mass percentage:
[0026] Acrylamide 25.0
[0027] Acryloyloxyethyltrimethylammonium chloride 6.98
[0028] Redox agent (potassium persulfate: dimethyloctylamine = 1: 1) 0.02
[0029] Azobisamidinopropane 0.15
[0030] Urea 2.2
[0031] Sodium propionate 0.15
[0032] Deionized water 65.5
[0033] The operation steps are: add deionized water into the reactor, feed nitrogen until the oxygen saturation is ≤5%, add acrylamide, acryloyloxyethyltrimethylammonium chloride, urea and sodium propionate in sequence to adjust the pH value to 6.5, by feeding nitrogen and keeping the oxygen saturation ≤ 5%, adding a redox agent, reacting under the condition of nitrogen protection for 45 minutes, then adding azobisamidinopropane, continuing the reaction for 50 minutes, at 50 ° C React for another 4.5 hours to obtain copolymer colloid, cool to room temperature, granulate, and dry at 60-70°C to obtain cationic polyacrylamid...
Embodiment 3
[0035] The raw materials of each raw material are calculated by mass percentage:
[0036] Acrylamide 14.5
[0037] Acryloyloxyethyltrimethylammonium chloride 10.0
[0038] Redox agent (potassium persulfate: triethanolamine=1:1) 0.3
[0039] 2. 2-azobis(2-amidinopropane) 0.1
[0040] Urea 5.0
[0042] Deionized water 70.0
[0043] The operation steps are: add deionized water into the reactor, feed nitrogen until the oxygen saturation is ≤5%, add acrylamide, acryloyloxyethyltrimethylammonium chloride, urea and sodium butyrate in sequence, adjust When the pH value reaches 7, enter nitrogen and keep the oxygen saturation ≤ 5%, add a redox agent, react for 47 minutes under the condition of nitrogen protection, then add 2,2 azobis(2-amidinopropane) to continue the reaction After 60 minutes, react at 40°C for another 5 hours to obtain copolymer colloid, cool to room temperature, granulate, and dry at 60-70°C to obtain cationic polyacrylamide. Its p...
PUM
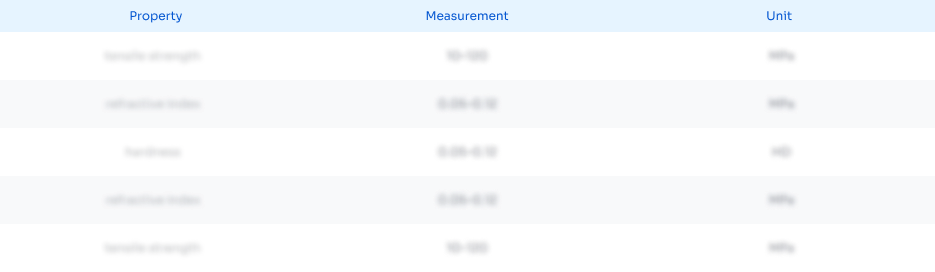
Abstract
Description
Claims
Application Information

- Generate Ideas
- Intellectual Property
- Life Sciences
- Materials
- Tech Scout
- Unparalleled Data Quality
- Higher Quality Content
- 60% Fewer Hallucinations
Browse by: Latest US Patents, China's latest patents, Technical Efficacy Thesaurus, Application Domain, Technology Topic, Popular Technical Reports.
© 2025 PatSnap. All rights reserved.Legal|Privacy policy|Modern Slavery Act Transparency Statement|Sitemap|About US| Contact US: help@patsnap.com