Preparation method for upper nozzle used for continuous casting
A technology of continuous casting and raw materials, which is applied in the field of preparation of upper nozzles for continuous casting. It can solve problems such as poor corrosion resistance of quartz nozzles, difficulty in meeting casting process requirements, and infiltration of molten steel into non-metallic inclusions, so as to prevent poor steel flow. Effects of even clogging, excellent slag resistance, and stable air permeability
- Summary
- Abstract
- Description
- Claims
- Application Information
AI Technical Summary
Problems solved by technology
Method used
Examples
Embodiment 1
[0018] A method for preparing an upper nozzle for continuous casting, the upper nozzle is composed of inner and outer layers, and the raw materials of the inner layer are composed of the following raw materials in parts by weight: 76 parts of -200 mesh aluminum titanate, 14 parts of -200 mesh silicon nitride , 6 parts of -200 mesh aluminum nitride, 6 parts of phenolic resin; The raw material of outer layer is made up of following raw material by weight: 20-200 mesh porous mullite ceramic particles 30 parts, -200 mesh mullite fine powder 46 Parts, -200 mesh zircon mullite fine powder 6 parts, -200 mesh Cr 2 o 3 5 parts of fine powder, 4 parts of -200 mesh clay fine powder, 3 parts of -200 mesh activated α-alumina micropowder, 3 parts of silica sol, and the preparation method comprises the following steps:
[0019] 1) Mixing: mix and stir the inner layer and outer layer raw materials in the mixer according to the above ratio, and then granulate;
[0020] 2) Forming: isostatic ...
Embodiment 2
[0023] A method for preparing an upper nozzle for continuous casting. The upper nozzle is composed of two layers, an inner layer and an inner layer. The raw materials of the inner layer are composed of the following raw materials in parts by weight: 80 parts of -200 mesh aluminum titanate, 12 parts of -200 mesh silicon nitride , 8 parts of -200 mesh aluminum nitride, 4 parts of phenolic resin; The raw material of outer layer is made up of following raw material by weight: 20-200 mesh porous mullite ceramic particles 34 parts, -200 mesh mullite fine powder 42 8 parts, -200 mesh zircon mullite fine powder, -200 mesh Cr 2 o 3 3 parts of fine powder, 6 parts of -200 mesh clay fine powder, 1 part of -200 mesh activated α-alumina micropowder, 5 parts of silica sol, and the preparation method includes the following steps:
[0024] 1) Mixing: mix and stir the inner layer and outer layer raw materials in the mixer according to the above ratio, and then granulate;
[0025] 2) Forming:...
Embodiment 3
[0028] A method for preparing an upper nozzle for continuous casting, the upper nozzle is composed of two layers inside and outside, and the raw materials of the inner layer are composed of the following raw materials in parts by weight: 78 parts of -200 mesh aluminum titanate, 13 parts of -200 mesh silicon nitride , 7 parts of -200 mesh aluminum nitride, 5 parts of phenolic resin; The raw material of outer layer is made up of following raw material by weight: 20-200 mesh porous mullite ceramic particles 32 parts, -200 mesh mullite fine powder 44 7 parts, -200 mesh zircon mullite fine powder, -200 mesh Cr 2 o 3 4 parts of fine powder, 5 parts of -200 mesh clay fine powder, 2 parts of -200 mesh activated α-alumina micropowder, 4 parts of silica sol, and the preparation method includes the following steps:
[0029] 1) Mixing: mix and stir the inner layer and outer layer raw materials in the mixer according to the above ratio, and then granulate;
[0030] 2) Forming: isostatic ...
PUM
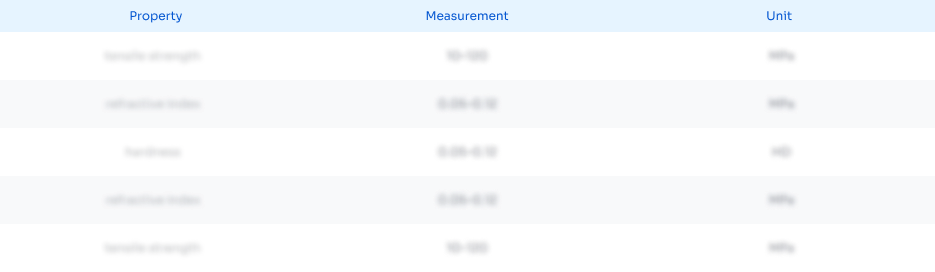
Abstract
Description
Claims
Application Information

- R&D
- Intellectual Property
- Life Sciences
- Materials
- Tech Scout
- Unparalleled Data Quality
- Higher Quality Content
- 60% Fewer Hallucinations
Browse by: Latest US Patents, China's latest patents, Technical Efficacy Thesaurus, Application Domain, Technology Topic, Popular Technical Reports.
© 2025 PatSnap. All rights reserved.Legal|Privacy policy|Modern Slavery Act Transparency Statement|Sitemap|About US| Contact US: help@patsnap.com