Formed catalyst for directly catalyzing N2O to decompose and manufacturing method thereof
A catalyst, direct technology, applied in physical/chemical process catalysts, separation methods, chemical instruments and methods, etc., can solve the problems of easy sintering and insufficient thermal stability of transition metal composite oxides, and achieve high mechanical strength, N2O The effect of wide concentration and strong antioxidant properties
- Summary
- Abstract
- Description
- Claims
- Application Information
AI Technical Summary
Problems solved by technology
Method used
Image
Examples
Embodiment 1
[0028] (1) Preparation of composite material carrier
[0029] 500g special pseudo-boehmite, 30gZrO 2 powder, 5g of scallop powder are mixed evenly, and then the powder is kneaded with 12g of nitric acid, 24g of acetic acid, and 350g of tap water to become a plastic body, and then extruded into a 5mm cylinder on an extruder to become a plastic body, the material is aged for 2 hours, and then Extruded into a 5mm cylinder on the extruder, then dewatered at low temperature for 12 hours, then dried at 100°C for 24 hours, and then put it into a muffle furnace for temperature-programmed roasting, the heating rate was 1°C / min, and the roasting temperature was 550°C. The calcination time is 4 hours, and the composite material carrier S1 is obtained by naturally cooling to room temperature in the furnace.
[0030] (2) Preparation of active ingredient solution
[0031] Weigh 87.2gZn(NO 3 ) 2 .6H 2 O solid, 6.4gNi(NO 3 ) 2 .6H 2 O solid, 9.6gCu(NO 3 )2.3H 2 O solid, water 14g...
Embodiment 2
[0037] (1) Preparation of composite material carrier
[0038] Mix 500g of special pseudo-boehmite and 5g of quince powder evenly, then knead the powder with 18g of 65-68wt% nitric acid, 24g of 99.5wt% acetic acid, 350g of water, and 317.8g of zinc nitrate to form a plastic body. Aged for 2 hours, then extruded into a 5mm cylinder on the extruder, then dewatered at low temperature for 12 hours, then dried at 100°C for 24 hours, then put into a muffle furnace for programmed temperature rise and roasting, the heating rate was 1°C / min, the roasting temperature Calcined at 550°C for 4 hours, and naturally cooled to room temperature in the furnace to obtain the composite material carrier S2.
[0039] (2) Preparation of active ingredient solution
[0040] Weigh 62.7gZn(NO 3 ) 2 .6H 2 O solid, 8gNi(NO 3 ) 2 .6H 2 O solid, 12.2gCu(NO 3 ) 2 .3H 2 O solid, water 18g, prepared into a solution.
[0041] (3) Impregnation and roasting of active components
[0042] Impregnate 60g ...
Embodiment 3
[0046] (1) Preparation of composite material carrier
[0047] Mix 500g of special pseudo-boehmite and 5g of fenugreek powder evenly, then knead the powder with 18g of 65-68wt% nitric acid, 24g of 99.5wt% acetic acid, 350g of tap water, and 317.8g of zinc nitrate to form a plastic body. Aged for 2 hours, then extruded into a 5mm cylinder on the extruder, then dewatered at low temperature for 12 hours, then dried at 100°C for 24 hours, then put into a muffle furnace for programmed temperature rise and roasting, the heating rate was 1°C / min, the roasting temperature The temperature is 550°C, the calcination time is 4h, and it is naturally cooled to room temperature in the furnace to obtain the composite material carrier S3.
[0048] (2) Preparation of active ingredient solution
[0049] Weigh 62.4gZn(NO 3 ) 2 .6H 2 O solid, 6.57gNi(NO 3 ) 2 .6H 2 O solid, water 22g, prepared into a solution.
[0050] (3) Impregnation and roasting of active components
[0051] Impregn...
PUM
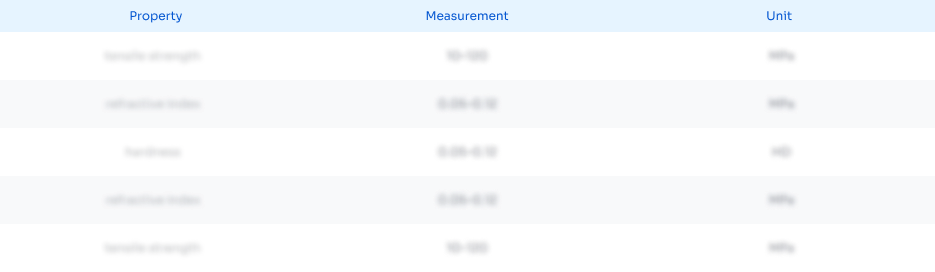
Abstract
Description
Claims
Application Information

- R&D
- Intellectual Property
- Life Sciences
- Materials
- Tech Scout
- Unparalleled Data Quality
- Higher Quality Content
- 60% Fewer Hallucinations
Browse by: Latest US Patents, China's latest patents, Technical Efficacy Thesaurus, Application Domain, Technology Topic, Popular Technical Reports.
© 2025 PatSnap. All rights reserved.Legal|Privacy policy|Modern Slavery Act Transparency Statement|Sitemap|About US| Contact US: help@patsnap.com