Method for purifying industrial silicon for preparing solar grade silicon
A solar-grade, industrial silicon technology, applied in chemical instruments and methods, silicon compounds, inorganic chemistry, etc., can solve the problem of insufficient contact between oxidizing gas and liquid silicon material, and the purity of silicon material cannot meet the requirements of silicon for solar cells. Requirements, difficult to recycle by-products and other issues, to achieve the effect of low cost, low energy consumption and high production efficiency
- Summary
- Abstract
- Description
- Claims
- Application Information
AI Technical Summary
Problems solved by technology
Method used
Image
Examples
Embodiment 1
[0049] Using industrial silicon as raw material, the main impurity components are Fe content 4731ppmw, Al content 3472ppmw, Ca content 291ppmw, Cu content 89ppmw, B content 19ppmw, P content 33ppmw, Ni content 31ppmw.
[0050]After the raw material is preliminarily crushed and pretreated, industrial silicon with a size of 10mm is used, placed on the hearth of a high-temperature solid-phase reaction furnace with a mesh or hole structure, and heated to a temperature of 1380°C in the high-temperature solid-phase reaction furnace. Add chlorine gas to react for 6 hours, and the vacuum degree during gas-solid reaction is 0.1*10 4 Pa, let the impurities inside the crystalline silicon fully diffuse to the surface, and react with chlorine gas to form compounds. After the treatment, the crystalline silicon is cleaned with hydrochloric acid and sodium hydroxide to remove the compounds on the surface, and then tested, the purity is 99.9991%; Place the cleaned crystalline silicon in a vacu...
Embodiment 2
[0053] Using industrial silicon as raw material, the main impurity components are Fe content 4023ppmw, Al content 3721ppmw, Ca content 134ppmw, Cu content 71ppmw, B content 23ppmw, P content 33ppmw, Ni content 41ppmw.
[0054] After the raw material is preliminarily crushed and pretreated, industrial silicon with a size of 10mm is used, placed on the hearth of a high-temperature solid-phase reaction furnace with a mesh or hole structure, and heated to a temperature of 1380°C in the high-temperature solid-phase reaction furnace. Add hydrogen chloride gas to react for 8 hours, and the vacuum degree during gas-solid reaction is 0.8*10 5 Pa, let the impurities inside the crystalline silicon fully diffuse to the surface, and react with hydrogen chloride gas to form compounds. After the treatment, the crystalline silicon is cleaned with hydrofluoric acid and ammonia water to remove the compounds on the surface, and then tested, the purity is 99.9993%; Place the cleaned crystalline s...
Embodiment 3
[0057] Using industrial silicon as raw material, the main impurity components are Fe content 4323ppmw, Al content 3218ppmw, Ca content 287ppmw, Cu content 93ppmw, B content 30ppmw, P content 38ppmw, Ni content 25ppmw.
[0058] After the raw material is preliminarily crushed and pretreated, industrial silicon with a size of 10mm is used, placed on the hearth of a high-temperature solid-phase reaction furnace with a mesh or hole structure, and heated to a temperature of 1380°C in the high-temperature solid-phase reaction furnace. Add hydrogen chloride and chlorine gas (1:2) to react for 6 hours, and the vacuum degree during the gas-solid reaction is 1.2*10 5 Pa, let the impurities inside the crystalline silicon fully diffuse to the surface, and react with hydrogen chloride and chlorine gas to form compounds. After the treatment, the crystalline silicon is cleaned with nitric acid and ammonia water to remove the compounds on the surface, and then tested, the purity is 99.9993% ; ...
PUM
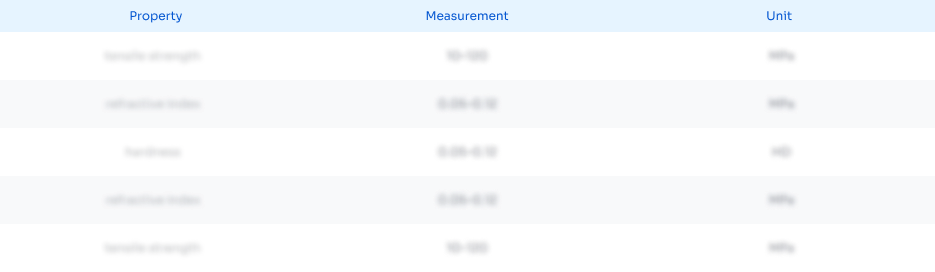
Abstract
Description
Claims
Application Information

- Generate Ideas
- Intellectual Property
- Life Sciences
- Materials
- Tech Scout
- Unparalleled Data Quality
- Higher Quality Content
- 60% Fewer Hallucinations
Browse by: Latest US Patents, China's latest patents, Technical Efficacy Thesaurus, Application Domain, Technology Topic, Popular Technical Reports.
© 2025 PatSnap. All rights reserved.Legal|Privacy policy|Modern Slavery Act Transparency Statement|Sitemap|About US| Contact US: help@patsnap.com