Radiating packaging structure and manufacturing method thereof
A technology of packaging structure and heat dissipation type, which is used in semiconductor/solid-state device manufacturing, electrical components, electric solid-state devices, etc., can solve the problems of affecting the appearance of the package, large loss of cutting tools, and increased cost, so as to avoid the problem of burrs and cutting tools. Wear problems, the effect of reducing cutting costs
- Summary
- Abstract
- Description
- Claims
- Application Information
AI Technical Summary
Problems solved by technology
Method used
Image
Examples
no. 1 example
[0052] Please refer to FIGS. 4A and 4F , which are schematic diagrams of the first embodiment of the heat-dissipating package structure and its manufacturing method of the present invention.
[0053] As shown in FIG. 4A , at first, the semiconductor chip 41 is placed and electrically connected to the chip carrier 42, and at the same time, a heat sink 44 with an interface layer 43 on the surface is connected to the heat sink 44 with one side of the heat sink 44. The surface of the semiconductor wafer 41 that is not provided for contact with the wafer carrier 42 . The planar dimension of the heat sink does not exceed the planar dimension of the semiconductor package structure to be formed.
[0054] The chip carrier 42 is, for example, a ball grid array (BGA) substrate or a land grid array (LGA) substrate, and the semiconductor chip 41 is, for example, a flip-chip semiconductor chip, and the flip-chip semiconductor chip is passed through a plurality of conductive bumps. 410 to e...
no. 2 example
[0062] Please refer to FIGS. 5A and 5B (the FIG. 5B is a top view of FIG. 5A ), which are cross-sectional and top schematic views of the second embodiment of the heat dissipation package structure of the present invention. The manufacturing method of the heat-dissipating package structure in the second embodiment of the present invention is substantially the same as the above-mentioned manufacturing method, the main difference is that when the bevel is formed on the top edge of the sealing compound 55 by means of grinding operations, etc., the sealing compound 55 is ground and stretched. to the heat sink 54 , so as to facilitate the subsequent removal of the interface layer on the surface of the heat sink and the excess encapsulant on the interface layer.
no. 3 example
[0064] Please refer to FIG. 6 , which is a schematic cross-sectional view of the third embodiment of the semiconductor package structure made with reference to the heat dissipation type package structure method of the present invention. The difference is that in the semiconductor package structure of this embodiment, the radiator 64 is attached The material of the interface layer 63 on the surface is selected so that the bonding force with the heat sink 64 is greater than the bonding force between the interface layer 63 and the encapsulant 65', such as a metal layer such as gold or nickel, so that the cutting operation is completed along the predetermined package structure size, and After the top edge of the encapsulant 65 is ground to form a bevel, the encapsulant 65' located on the interface layer 63 can be removed from the interface layer 63 during the removal operation, so that the interface layer 63 is exposed to the package. The colloid 65 allows the heat generated by the...
PUM
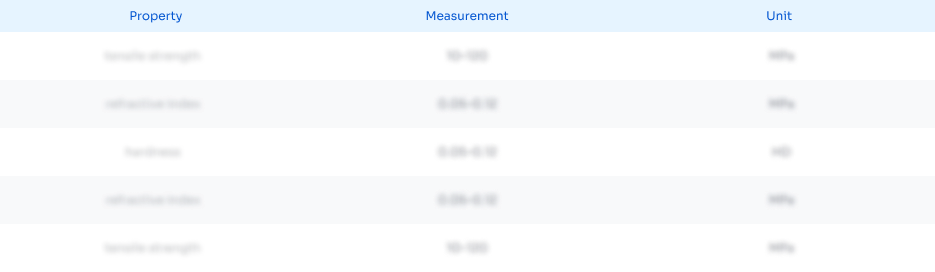
Abstract
Description
Claims
Application Information

- R&D Engineer
- R&D Manager
- IP Professional
- Industry Leading Data Capabilities
- Powerful AI technology
- Patent DNA Extraction
Browse by: Latest US Patents, China's latest patents, Technical Efficacy Thesaurus, Application Domain, Technology Topic, Popular Technical Reports.
© 2024 PatSnap. All rights reserved.Legal|Privacy policy|Modern Slavery Act Transparency Statement|Sitemap|About US| Contact US: help@patsnap.com