Method for forming cutting surface in deep hole blasting
A deep hole blasting and cutting surface technology, which is applied in blasting and other directions, can solve the problems of affecting mining production efficiency, poor cutting effect on both sides of small wells, and difficult hole layout in deep holes, so as to realize integrated cutting and mining operations and simplify mining and cutting Process, the effect of improving cutting efficiency
- Summary
- Abstract
- Description
- Claims
- Application Information
AI Technical Summary
Problems solved by technology
Method used
Image
Examples
Embodiment 1
[0023] A method for forming a cutting surface in deep hole blasting. The setting of the blasting point includes a central charge hole 1, an empty hole 2, an auxiliary charge hole 3, a cutting fan hole 4, and a radiation center 5. The central charge hole 1 is located in the center of the hollow hole 2; the hollow hole 2 is parallel to the central charge hole 1; the auxiliary charge hole 3 is symmetrical about the central charge hole 1 and the two rows of cutting fan-shaped holes 4; the cutting fan-shaped hole 4 is Two rows of fan-shaped deep holes with a row spacing of 2000mm; the cutting fan-shaped holes 4 are two rows of fan-shaped blast holes, located on the left and right sides of the auxiliary charge hole 3; the radiation center 5 is located on the two radiation center points of the cutting fan hole 4 ;
[0024] In the blasting, the sequence of initiation is central charge hole 1 → auxiliary charge hole 3 → cutting fan hole 4; the cutting fan hole 4 is blasted to both sides w...
PUM
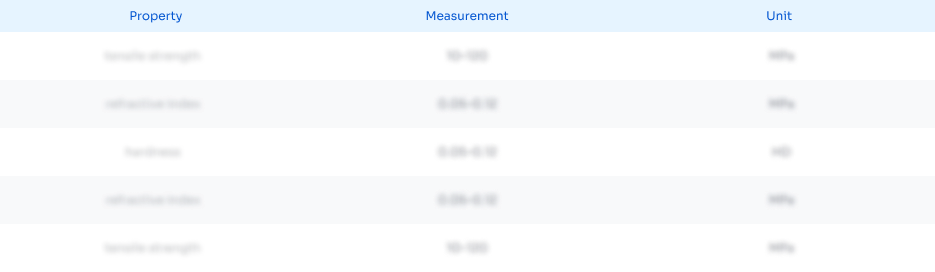
Abstract
Description
Claims
Application Information

- R&D
- Intellectual Property
- Life Sciences
- Materials
- Tech Scout
- Unparalleled Data Quality
- Higher Quality Content
- 60% Fewer Hallucinations
Browse by: Latest US Patents, China's latest patents, Technical Efficacy Thesaurus, Application Domain, Technology Topic, Popular Technical Reports.
© 2025 PatSnap. All rights reserved.Legal|Privacy policy|Modern Slavery Act Transparency Statement|Sitemap|About US| Contact US: help@patsnap.com