Heat shield resistant to extreme high temperature and strong impact and manufacturing method thereof
A high-heat, high-endurance technology, applied in the field of thermal management, can solve the problems of short endurance time, low temperature of phase change point, latent heat of phase change and not too high heat capacity, etc., to achieve a slow increase in temperature, increase heat transfer thermal resistance, The effect of large latent heat of phase change
- Summary
- Abstract
- Description
- Claims
- Application Information
AI Technical Summary
Problems solved by technology
Method used
Image
Examples
Embodiment 1
[0042] 20 g of stearic acid and 1.3 g of sodium dodecyl methyl sulfate were mixed, added to 160 ml of deionized water, and magnetically stirred at 80° C. for 1 hour to make the mixture uniform to form A solution. Then add 12ml of MTMS (methyltrimethoxysilane) and 12ml of TEOS ethyl orthosilicate to mix with an appropriate amount of anhydrous ethanol, and then add dilute hydrochloric acid to condition the pH to make the solution pH between 2 and 3, and at 80 ° C Magnetic stirring was carried out at 400 rpm for 30 min to form B solution. The A solution was added dropwise to the B solution and stirred magnetically at 400 rpm for 2 hours at 80°C. Then, ultrasonically vibrate the mixed solution for 30 min, filter and dry to obtain a white phase-change setting material; mix the obtained phase-change setting material, expanded perlite, and halloysite nanotubes in a ratio of 7:2:1 to obtain Inorganic particles containing shape-setting phase change material; gum arabic, hydroxymethyl ...
Embodiment 2
[0044]TEOS (ethyl orthosilicate) was mixed with purified water in a molar ratio of 2:3, and magnetically stirred at 400 rpm for 30 min at 30 °C. After that, add dilute hydrochloric acid to condition the pH to make the solution pH between 2 and 3. Then an appropriate amount of CTAB (hexadecyltrimethylammonium bromide), deionized water and absolute ethanol were added in sequence. And stirred at 13000rpm for 10min. After that, an appropriate amount of 25wt% ammonia water was added, and after 10 hours of reaction, it was taken out for filtration, and after freeze-drying, a white phase change material was obtained; the obtained phase change material and silica aerogel were subjected to a 2:1 ratio The proportions are mixed evenly to obtain inorganic particles containing the shape-setting phase change material; gum arabic, hydroxymethyl cellulose and water-soluble phenolic resin are mixed uniformly in a ratio of 1:1:2 to form a mixed resin adhesive; then 59 % mass fraction of inor...
PUM
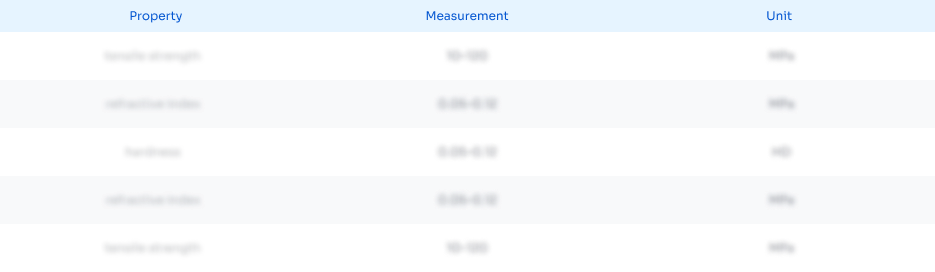
Abstract
Description
Claims
Application Information

- R&D Engineer
- R&D Manager
- IP Professional
- Industry Leading Data Capabilities
- Powerful AI technology
- Patent DNA Extraction
Browse by: Latest US Patents, China's latest patents, Technical Efficacy Thesaurus, Application Domain, Technology Topic, Popular Technical Reports.
© 2024 PatSnap. All rights reserved.Legal|Privacy policy|Modern Slavery Act Transparency Statement|Sitemap|About US| Contact US: help@patsnap.com