A method for recovering vanadium and iron from acid solution containing tetravalent vanadium and divalent iron
A technology of ferrous iron and tetravalent vanadium, which is applied in the field of wet vanadium extraction, can solve the problems of large amount of washing water, reduce the amount of resin adsorption, and clogging the resin, so as to avoid the introduction of purifying agents, high resource recovery rate, and simplified The effect of the purification operation
- Summary
- Abstract
- Description
- Claims
- Application Information
AI Technical Summary
Problems solved by technology
Method used
Image
Examples
Embodiment 1
[0075] Present embodiment provides a kind of method that reclaims vanadium and iron from pickling solution, as figure 1 Shown, main element concentration is V1.68g / L in described stone coal pickling solution, Fe 8.96g / L, Al 12.39g / L, described method comprises the steps:
[0076] (1) Control the temperature of the stone coal acid leaching solution to 90°C, add sodium hydroxide to adjust the pH of the acid leaching solution to 2.5, then add iron oxyhydroxide crystal seeds, and the solid-liquid ratio of iron oxyhydroxide crystal seeds to the acid leaching solution kg / m 3 It is 2:1, stirring (stirring speed is 60r / min, stirring time is 30min) to obtain pretreatment liquid after seed crystal uniform distribution, main element concentration is V 1.65g / L in the pretreatment liquid, Fe 8.97g / L, Al 12.43g / L;
[0077] (2) add oxygenant sodium perchlorate to step (1) pretreatment liquid and carry out oxidation treatment, the oxygenant consumption is ferrous iron and tetravalent vanadiu...
Embodiment 2
[0085] This embodiment provides a method for reclaiming vanadium and iron from the acid leaching solution. The concentration of main elements in the acid leaching solution for stone coal is V 1.68g / L, Fe 8.96g / L, and Al 12.39g / L. Said method comprises the steps:
[0086] (1) Control the temperature of the stone coal acid leaching solution at 95°C, add sodium carbonate, potassium carbonate, sodium bicarbonate, potassium bicarbonate, ammonium carbonate, ammonium bicarbonate, magnesium carbonate, aluminum carbonate, ferrous carbonate, iron carbonate and carbonic acid Calcium adjusts the pH of the acid leaching solution to be 2. After solid-liquid separation, the filtrate is added with iron oxyhydroxide crystal seeds, and the solid-liquid ratio of iron oxyhydroxide crystal seeds to the acid leaching solution is kg / m 3 1.8:1, stirring (stirring speed is 50r / min, and stirring time is 60min) to obtain pretreatment liquid after seed crystal even distribution, main element concentratio...
Embodiment 3
[0095] This embodiment provides a method for reclaiming vanadium and iron from the acid leaching solution. The concentration of main elements in the acid leaching solution for stone coal is V 1.68g / L, Fe 8.96g / L, and Al 12.39g / L. Said method comprises the steps:
[0096] (1) Control the temperature of the stone coal acid leaching solution at 35°C, add sodium hydroxide, potassium hydroxide, ammonia water, magnesium hydroxide, calcium hydroxide, ferrous hydroxide, ferric hydroxide and aluminum hydroxide to adjust the temperature of the acid leaching solution The pH is 1.7, after solid-liquid separation, the filtrate is added with ferric oxyhydroxide seeds, and the liquid-solid ratio of ferric oxyhydroxide seeds to the pickling solution is kg / m 3 is 0.08:1, stirring (stirring speed is 300r / min, and stirring time is 10min) to obtain pretreatment liquid after seed crystal is evenly distributed, and main element concentration is V1.63g / L in the pretreatment liquid, Fe 24.82g / L, Al ...
PUM
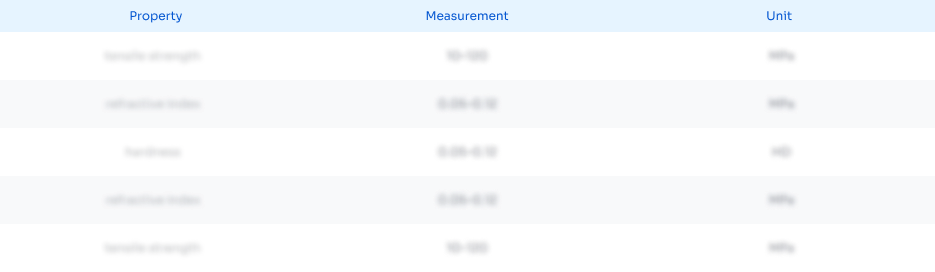
Abstract
Description
Claims
Application Information

- Generate Ideas
- Intellectual Property
- Life Sciences
- Materials
- Tech Scout
- Unparalleled Data Quality
- Higher Quality Content
- 60% Fewer Hallucinations
Browse by: Latest US Patents, China's latest patents, Technical Efficacy Thesaurus, Application Domain, Technology Topic, Popular Technical Reports.
© 2025 PatSnap. All rights reserved.Legal|Privacy policy|Modern Slavery Act Transparency Statement|Sitemap|About US| Contact US: help@patsnap.com