Method for preparing SiO2-SiC mosaic structure microporous antioxidant coating on surface of carbon/carbon composite material
A carbon composite material and anti-oxidation coating technology, which is applied in the field of carbon/carbon composite material anti-oxidation coating, can solve the problems of SiC coating failure, poor anti-oxidation performance, and no mitigation of oxide film cracking, etc., so as to inhibit cracking. , the effect of hindering the diffusion of oxygen
- Summary
- Abstract
- Description
- Claims
- Application Information
AI Technical Summary
Problems solved by technology
Method used
Image
Examples
Embodiment 1
[0041] Grind the carbon / carbon composite material with No. 400 and No. 800 sandpaper, wash it with absolute ethanol, and dry it in an oven at 70°C for 12 hours for later use; weigh 80g of silicon powder and 10g of graphite powder and place them in a turpentine ball mill jar for ball milling Mixing treatment for 5 hours, put the powder mixed by the ball mill into the graphite crucible, embed the dried carbon / carbon composite material into the mixed powder, so that the mixed powder completely covers the C / C composite material; put the graphite crucible into In the vacuum reaction furnace, after the vacuum treatment of the vacuum furnace, the argon gas is passed to normal pressure, and the furnace temperature is raised from room temperature to 2000 °C at a temperature increase rate of 5 °C / min, and the temperature is kept for 3 hours, and then the power is turned off and naturally cooled to room temperature. Argon protection was used throughout the process. Weigh 7g of silicon ca...
Embodiment 2
[0043] Grind the carbon / carbon composite material with No. 400 and No. 800 sandpaper, wash it with absolute ethanol, and dry it in an oven at 70°C for 12 hours for later use; weigh 77g of silicon powder and 15g of graphite powder and place them in a turpentine ball mill jar for ball milling Mixing treatment for 8 hours, put the powder mixed by the ball mill into the graphite crucible, embed the dried carbon / carbon composite material into the mixed powder, so that the mixed powder completely covers the C / C composite material; put the graphite crucible into In the vacuum reaction furnace, after the vacuum treatment of the vacuum furnace, the argon gas is passed to the normal pressure, and the furnace temperature is raised from room temperature to 2050 °C at a heating rate of 7 °C / min, and the temperature is kept for 2 hours, and then the power is turned off and naturally cooled to room temperature. Argon protection was used throughout the process. Weigh 8g of silicon carbide pow...
Embodiment 3
[0045] Grind the carbon / carbon composite material with No. 400 and No. 800 sandpaper, wash it with absolute ethanol, and dry it in an oven at 70°C for 12 hours for later use; weigh 70g of silicon powder and 13g of graphite powder and place them in a turpentine ball mill jar for ball milling Mixing treatment for 8 hours, put the powder mixed by the ball mill into the graphite crucible, embed the dried carbon / carbon composite material into the mixed powder, so that the mixed powder completely covers the C / C composite material; put the graphite crucible into In the vacuum reaction furnace, after the vacuum treatment of the vacuum furnace, the argon gas was passed to normal pressure, and the furnace temperature was raised from room temperature to 2100 °C at a heating rate of 9 °C / min, and kept for 1 hour, and then the power was turned off and naturally cooled to room temperature. Argon protection was used throughout the process. Weigh 9g of silicon carbide powder and 1g of silicon...
PUM
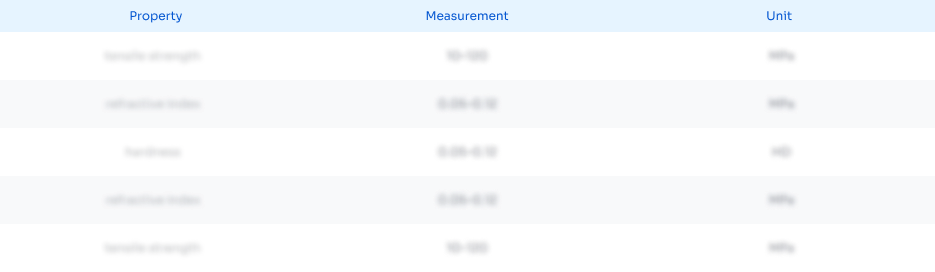
Abstract
Description
Claims
Application Information

- R&D Engineer
- R&D Manager
- IP Professional
- Industry Leading Data Capabilities
- Powerful AI technology
- Patent DNA Extraction
Browse by: Latest US Patents, China's latest patents, Technical Efficacy Thesaurus, Application Domain, Technology Topic, Popular Technical Reports.
© 2024 PatSnap. All rights reserved.Legal|Privacy policy|Modern Slavery Act Transparency Statement|Sitemap|About US| Contact US: help@patsnap.com