Machining technology of high-strength high-hardness gray pig iron
A processing technology, the technology of gray cast iron, applied in the direction of improving process efficiency, etc., can solve the problems of poor fluidity and low wear resistance, and achieve the effects of good cutting performance, simple control and superior casting performance
- Summary
- Abstract
- Description
- Claims
- Application Information
AI Technical Summary
Problems solved by technology
Method used
Examples
Embodiment Construction
[0016] The present invention will be further described below:
[0017] A processing technology for high-strength and high-hardness gray cast iron, comprising the following steps:
[0018] (1) Carry out smelting of gray iron castings with grade Q235 as scrap steel, grade as Q10 pig iron and returned charge as raw materials;
[0019] (2) First add ferromanganese and 10% pig iron with grade Q10 into the medium frequency induction furnace;
[0020] (3) Then add 3.5% recarburizer and 60% steel scrap of grade Q235 at the same time, melt until the volume of molten iron in the induction furnace is smelted to 3 / 4 of the original volume, adjust the melting temperature to 1400°C, and the melting time to 1h;
[0021] (4) adding 0.5-0.8% silicon carbide into an induction furnace whose volume of molten iron is 2 / 3 and smelting simultaneously to form former molten iron, adjusting the melting temperature to be 1400°C, and the melting time to be 1-3h;
[0022] (5) After heating the original ...
PUM
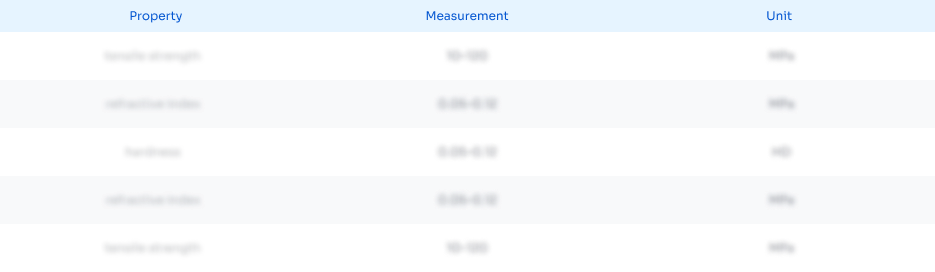
Abstract
Description
Claims
Application Information

- R&D
- Intellectual Property
- Life Sciences
- Materials
- Tech Scout
- Unparalleled Data Quality
- Higher Quality Content
- 60% Fewer Hallucinations
Browse by: Latest US Patents, China's latest patents, Technical Efficacy Thesaurus, Application Domain, Technology Topic, Popular Technical Reports.
© 2025 PatSnap. All rights reserved.Legal|Privacy policy|Modern Slavery Act Transparency Statement|Sitemap|About US| Contact US: help@patsnap.com