Preparation method of wear-resistant SBS (styrene butadiene styrene) sole material
A sole material and mixing technology, applied in the field of preparation of wear-resistant SBS sole materials, can solve the problems of poor material strength, weak matrix binding force, large specific surface energy, etc., to improve toughness and strength, improve crystallinity, combine good effect
- Summary
- Abstract
- Description
- Claims
- Application Information
AI Technical Summary
Problems solved by technology
Method used
Image
Examples
Embodiment 1
[0027] A preparation method for wear-resistant SBS sole material, comprising the following steps:
[0028] Step 1. Mix calcium carbonate, maleic anhydride, ethylene glycol, and water in a reaction kettle, stir for 4 hours at a temperature of 30°C and a stirring rate of 400r / min, then add acrylic acid and diisocyanate at a temperature of 40°C , Stirring rate is 600r / min under stirring 8h, filters, obtains modified calcium carbonate; In the step 1, the mass ratio of calcium carbonate, maleic anhydride, ethylene glycol, water, acrylic acid, diisocyanate is 1:1:2:5 :0.5:1;
[0029] Step 2: Mix the modified calcium carbonate, neodymium oxide, strontium carbonate, aluminum oxide, magnesium oxide, and absolute ethanol evenly, and ball mill for 8 hours in a ball mill with a rotating speed of 800r / min, and then calcinate in a sintering furnace with a temperature of 100°C 1h, obtain the first mixed material; In step 2, the mass ratio of modified calcium carbonate, neodymium oxide, stro...
Embodiment 2
[0043] A preparation method for wear-resistant SBS sole material, comprising the following steps:
[0044] Step 1. Mix calcium carbonate, maleic anhydride, ethylene glycol, and water in a reaction kettle, stir for 5 hours at a temperature of 40°C and a stirring rate of 500r / min, then add acrylic acid and diisocyanate at a temperature of 50°C , Stirring rate is that stirring 10h under 800r / min filters, obtains modified calcium carbonate; In step 1, the mass ratio of calcium carbonate, maleic anhydride, ethylene glycol, water, acrylic acid, diisocyanate is 1:1.5:2.5:8 :0.7:2;
[0045] Step 2: Mix the modified calcium carbonate, neodymium oxide, strontium carbonate, aluminum oxide, magnesium oxide, and absolute ethanol evenly, and ball mill for 10 hours in a ball mill with a rotating speed of 1000r / min, and then calcinate in a sintering furnace with a temperature of 120°C 1.5h, the first mixed material is obtained; the mass ratio of modified calcium carbonate, neodymium oxide, s...
Embodiment 3
[0059] A preparation method for wear-resistant SBS sole material, comprising the following steps:
[0060] Step 1. Mix calcium carbonate, maleic anhydride, ethylene glycol, and water in a reactor, stir for 6 hours at a temperature of 50°C and a stirring rate of 600r / min, then add acrylic acid and diisocyanate at a temperature of 60°C , Stirring rate is 1000r / min under stirring 12h, filters, obtains modified calcium carbonate; In the step 1, the mass ratio of calcium carbonate, maleic anhydride, ethylene glycol, water, acrylic acid, diisocyanate is 1:2:3:10 :1:3;
[0061] Step 2: Mix the modified calcium carbonate, neodymium oxide, strontium carbonate, aluminum oxide, magnesium oxide, and absolute ethanol evenly, and ball mill for 12 hours in a ball mill with a rotating speed of 1200r / min, and then calcinate in a sintering furnace with a temperature of 150°C 2h, to obtain the first mixed material; the mass ratio of modified calcium carbonate, neodymium oxide, strontium carbona...
PUM
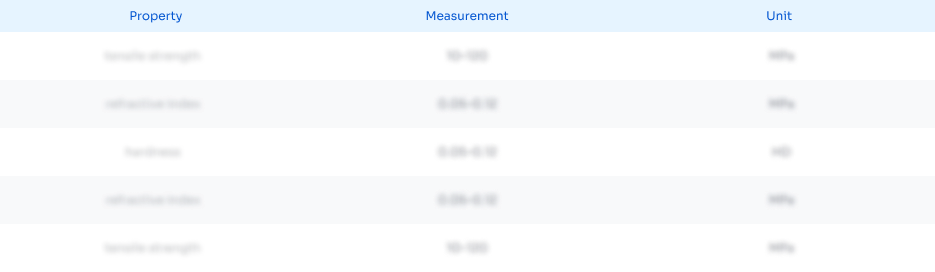
Abstract
Description
Claims
Application Information

- R&D
- Intellectual Property
- Life Sciences
- Materials
- Tech Scout
- Unparalleled Data Quality
- Higher Quality Content
- 60% Fewer Hallucinations
Browse by: Latest US Patents, China's latest patents, Technical Efficacy Thesaurus, Application Domain, Technology Topic, Popular Technical Reports.
© 2025 PatSnap. All rights reserved.Legal|Privacy policy|Modern Slavery Act Transparency Statement|Sitemap|About US| Contact US: help@patsnap.com