Selective separation and recycling method for industrial solid waste slag
A solid waste, selective technology, used in solid separation, wet separation, chemical instruments and methods, etc., can solve the problems of equipment wear, difficult to achieve magnetic separation recovery, secondary dust pollution, etc. Selective separation and reduced energy consumption
- Summary
- Abstract
- Description
- Claims
- Application Information
AI Technical Summary
Problems solved by technology
Method used
Image
Examples
Embodiment 1
[0039]Weigh 50 kilograms of blast furnace steel slag, add 100 grams of sulfuric acid, 11 grams of cetyl ammonium bromide, 100 grams of natron (45°, modulus 3.0), mix and stir for 30 minutes, and let stand for 4 hours; then start the rod mill machine, feed circulating liquid at a speed of 30 liters / min (clear water is fed in at the beginning stage), continuously add mixed slurry, overflow liquid enters three-stage magnetic separator, magnetically separated solids are mixed, dehydrated and dried; after magnetic separation, the slurry Enter the conical overflow settler, the lower sediment returns to the rod mill to continue grinding, the upper overflow flows into the precision sedimentation tank, the water channel of the sedimentation tank is divided into three sections, the residence time is 10 seconds, 50 seconds and 19 minutes respectively, the total residence time After 20 minutes, after settling, the supernatant was returned to the rod mill for recycling. The solid slurry se...
Embodiment 2
[0045] Weigh 50 kilograms of stainless steel smelting waste residue, add 100 grams of 1:1:1 nitric acid, hydrochloric acid, acetic acid mixed solution, 20 grams of 1:1:1 imidazoline, oleic acid, triethanolamine mixed solution, 1:1:1 sulfuric acid Sodium, sodium metasilicate, 100 grams of natron (45 °, modulus 3.0) mixture, mixed and stirred for 30 minutes, left standstill for 6 hours; then start the rod mill, feed the circulating clear liquid with 20 liters / minute speed ( In the initial stage, clean water is fed), and the mixed slurry is continuously added, and the overflow liquid enters the three-stage magnetic separator, and the magnetically separated solids are mixed, dehydrated and dried; after magnetic separation, the slurry enters the conical overflow settler, and the lower sediment returns to the rod The mill continues to grind, the upper overflow flows into the precision settling tank, the water channel of the settling tank is divided into four sections, the residence t...
Embodiment 3
[0052] Take by weighing 50 kilograms of metal zinc smelting waste residues, add 100 grams of 1:1:1 formic acid, acetic acid, benzoic acid mixed solution, 1:1:1 cetyl ammonium bromide, oleic acid, cationic polyacrylamide mixed solution 20 gram, 100 grams of glycerol, sodium hexametaphosphate, sodium hexametaphosphate (45 °, modulus 3.0) mixture of 1:1:1, mixed and stirred for 30 minutes, left standstill for 3 hours; then start the ball mill, with 10 liters / The circulating clear liquid is introduced at different speeds (clear water is introduced at the beginning stage), and the mixed slurry is continuously added, and the overflow liquid enters the three-stage magnetic separator, and the solids separated by magnetic separation are mixed, dehydrated and dried; after magnetic separation, the slurry enters the conical overflow Settler, the lower part of the sediment returns to the ball mill to continue grinding, the upper overflow flows into the precision settling tank, the water ch...
PUM
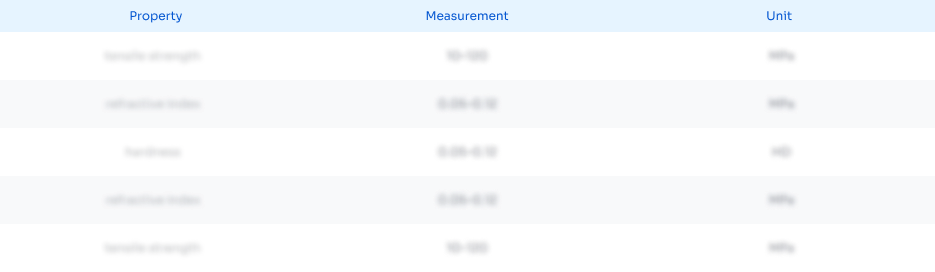
Abstract
Description
Claims
Application Information

- R&D
- Intellectual Property
- Life Sciences
- Materials
- Tech Scout
- Unparalleled Data Quality
- Higher Quality Content
- 60% Fewer Hallucinations
Browse by: Latest US Patents, China's latest patents, Technical Efficacy Thesaurus, Application Domain, Technology Topic, Popular Technical Reports.
© 2025 PatSnap. All rights reserved.Legal|Privacy policy|Modern Slavery Act Transparency Statement|Sitemap|About US| Contact US: help@patsnap.com