Alloy material flange and forging technology thereof
A technology of alloy material and flange, which is applied in the field of alloy material flange and its forging process, can solve the problems of sealing surface processing size error, inability to solve on-site solutions, enterprise shutdown and production shutdown, etc., to achieve good mechanical properties, improve room temperature and high temperature Mechanical properties, effect of eliminating shrinkage cavity
- Summary
- Abstract
- Description
- Claims
- Application Information
AI Technical Summary
Problems solved by technology
Method used
Examples
Embodiment 1
[0029] This embodiment provides a flange made of alloy material. The chemical composition of the selected alloy blank is: 12.7% nickel, 25.3% chromium, 0.1% carbon, 0.17% silicon, 0.72% manganese, 0.0015% sulfur, 2.25% molybdenum, titanium 3.25%, aluminum 3%, copper 1.25%, phosphorus 0.015%, tungsten 0.9%, boron 0.018%, niobium 0.9%, rare earth elements 0.11%, the rest is Fe and impurities; the rare earth elements include ytterbium 12%, erbium 6% , dysprosium 19%, gadolinium 26%, cerium 8%, lanthanum 14% and thorium 15%.
[0030] This embodiment also provides a forging process of an alloy material flange, including the following specific steps:
[0031] Step (1): first use a chemical analysis instrument to chemically analyze the alloy billet to ensure that its chemical composition meets the composition requirements of the above alloy materials;
[0032] Step (2): After the analysis of step (1) is qualified, a 5000Kg alloy billet is selected, and electric furnace is used for s...
Embodiment 2
[0041] This embodiment provides a flange made of alloy material. The chemical composition of the selected alloy blank is: 12.9% nickel, 25.5% chromium, 0.12% carbon, 0.19% silicon, 0.79% manganese, 0.0035% sulfur, 2.35% molybdenum, titanium 3.45%, aluminum 3.25%, copper 1.85%, phosphorus 0.017%, tungsten 1.1%, boron 0.022%, niobium 1.1%, rare earth elements 0.13%, the rest is Fe and impurities; the rare earth elements include ytterbium 12%, erbium 11% , dysprosium 19%, gadolinium 16%, cerium 8%, lanthanum 18% and thorium 16%.
[0042] This embodiment also provides a forging process of an alloy material flange, including the following specific steps:
[0043] Step (1): first use a chemical analysis instrument to chemically analyze the alloy billet to ensure that its chemical composition meets the composition requirements of the above alloy materials;
[0044] Step (2): After the analysis of step (1) is qualified, the alloy billet below 4800Kg is selected, and the electric furn...
Embodiment 3
[0053] This embodiment provides a kind of alloy material flange, selects the weight percentage chemical composition of alloy billet to be: nickel 12.8%, chromium 25.4%, carbon 0.11%, silicon 0.18%, manganese 0.76%, sulfur 0.0025%, molybdenum 2.30%, titanium 3.35%, aluminum 3.15%, copper 1.55%, phosphorus 0.016%, tungsten 1.0%, boron 0.020%, niobium 1.0%, rare earth elements 0.12%, the rest is Fe and impurities; the rare earth elements include ytterbium 12%, erbium 8% , dysprosium 21%, gadolinium 16%, cerium 8%, lanthanum 13% and thorium 22%.
[0054] This embodiment also provides a forging process of an alloy material flange, including the following specific steps:
[0055] Step (1): first use a chemical analysis instrument to chemically analyze the alloy billet to ensure that its chemical composition meets the composition requirements of the above alloy materials;
[0056] Step (2): After the analysis in step (1) is qualified, select an alloy billet below 4600Kg, use an elec...
PUM
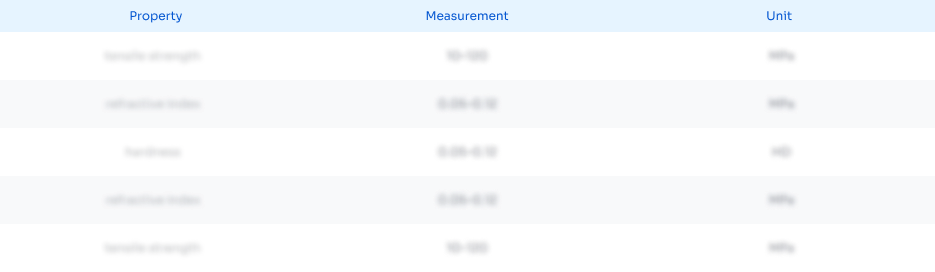
Abstract
Description
Claims
Application Information

- Generate Ideas
- Intellectual Property
- Life Sciences
- Materials
- Tech Scout
- Unparalleled Data Quality
- Higher Quality Content
- 60% Fewer Hallucinations
Browse by: Latest US Patents, China's latest patents, Technical Efficacy Thesaurus, Application Domain, Technology Topic, Popular Technical Reports.
© 2025 PatSnap. All rights reserved.Legal|Privacy policy|Modern Slavery Act Transparency Statement|Sitemap|About US| Contact US: help@patsnap.com