Difficult-separation iron ore tailing pelletizing rotary kiln magnetic roasting treatment technology
A technology of iron ore tailings and magnetization roasting, which is applied in the field of metallurgy, can solve problems such as low utilization rate, environmental pollution, resource waste, etc., and achieve the effect of improving resource utilization rate, reducing environmental pollution, and reducing grinding processes
- Summary
- Abstract
- Description
- Claims
- Application Information
AI Technical Summary
Problems solved by technology
Method used
Image
Examples
Embodiment 1
[0029] Raw materials Refractory iron ore tailings TFe grade 20.63%, SiO 2 The content is 40.35%. The iron minerals mainly exist in the form of specularite, hematite, siderite and limonite. The particle size: -200 mesh and the content is 68.3%.
[0030] The following process steps are adopted for processing:
[0031] Step 1: using a strong magnetic separator with a field strength of 0.6T to carry out magnetic separation and enrichment of iron ore tailings, the yield is 57.4%, and the enriched tailings with a TFe grade of 31.3% can be obtained;
[0032] Step 2: Mix the enriched tailings obtained in Step 1 with coal powder and clay evenly in a ratio of 100:0.5:2, dry and moisten, and then pelletize with a disc pelletizer, wherein the particle size of coal powder is:- The content of 200 mesh is 83%; the particle size of the pellets is controlled at 8-12mm, the drop strength of the pellets is ≥5 times / 0.5m, and the compressive strength is ≥10 N / ball;
[0033] Step 3: Use a grate ...
Embodiment 2
[0040] Raw materials Refractory iron ore tailings TFe grade 25.71%, SiO 2 The content is 38.26%. The iron minerals mainly exist in the form of hematite, siderite and limonite. The particle size: -200 mesh content is 30.6%.
[0041] The following process steps are adopted for processing:
[0042] Step 1: The particle size of the tailings is: -200 mesh content 30.6%, which is relatively coarse. In order to improve the effect of strong magnetic enrichment and meet the requirements of pelletizing particle size, the ore is firstly ground, and the -200 mesh content is 65% after grinding. Then use a strong magnetic separator with a field strength of 0.9T to carry out magnetic separation and enrichment of the iron ore tailings, with a yield of 62.4%, and the enriched tailings with a TFe grade of 34.6% can be obtained;
[0043] Step 2: Mix the enriched tailings obtained in Step 1 with coal powder and bentonite in a ratio of 100:1.2:3, dry and moisten the pellets with a disc pelletizer...
Embodiment 3
[0051] Raw materials Refractory iron ore tailings TFe grade 22.14%, SiO 2 The content is 39.53%. The iron minerals mainly exist in the form of specularite, hematite, siderite and limonite. The particle size: -200 mesh content is 30.6%.
[0052] The following process steps are adopted for processing:
[0053] Step 1: The particle size of the tailings is: -200 mesh content 45.3%, which is relatively coarse. In order to improve the effect of strong magnetic enrichment and meet the requirements of pelletizing particle size, the ore is firstly ground, and the -200 mesh content is 62% after grinding. Then use a strong magnetic separator with a field strength of 1.2T to carry out magnetic separation and enrichment of the iron ore tailings, with a yield of 59.2%, and the enriched tailings with a TFe grade of 32.1% can be obtained;
[0054] Step 2: Mix the enriched tailings obtained in Step 1 with coal powder and resin evenly in a ratio of 100:2:1, dry and moisten and grind, and then us...
PUM
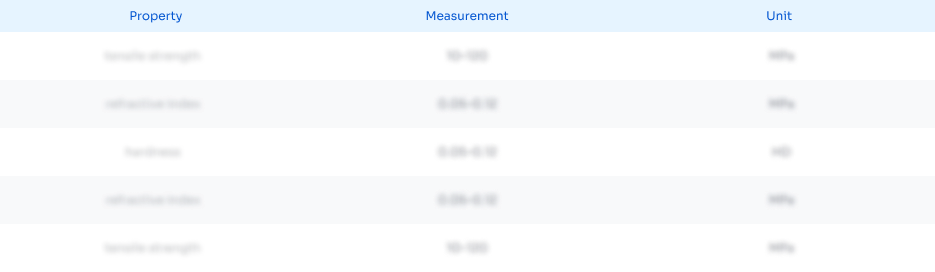
Abstract
Description
Claims
Application Information

- R&D
- Intellectual Property
- Life Sciences
- Materials
- Tech Scout
- Unparalleled Data Quality
- Higher Quality Content
- 60% Fewer Hallucinations
Browse by: Latest US Patents, China's latest patents, Technical Efficacy Thesaurus, Application Domain, Technology Topic, Popular Technical Reports.
© 2025 PatSnap. All rights reserved.Legal|Privacy policy|Modern Slavery Act Transparency Statement|Sitemap|About US| Contact US: help@patsnap.com