Method for increasing capacity of biodegradable polyester blend film
A biodegradable polyester and blending technology, which is applied in the field of compatibilization of biodegradable polyester blend films, can solve the problems of poor compatibility, seldom consider improving the compatibility of different polyesters, etc. heterosexual effect
- Summary
- Abstract
- Description
- Claims
- Application Information
AI Technical Summary
Problems solved by technology
Method used
Image
Examples
Embodiment 1
[0041] Premix: first add different materials into the high-speed mixer in sequence, and the order of addition is: PLA, talcum powder, 1501 (semi-aromatic copolyester), 1201 (PBS), isopropyl tris(dodecylbenzenesulfonyl) titanate (KR-9S), dicumyl peroxide (BIPB), ADR4368, released after mixing in a high-speed mixer. The composition ratio of the blend is shown in Table 1.
[0042] Table 1 Blend composition ratio one
[0043]
[0044] Extrusion granulation: Add the premix into the co-rotating parallel twin-screw extruder for extrusion granulation. The temperature settings are: 140-170-180-185-185-190-190-190-185-185-185-180°C.
[0045] Film blowing: Blow the film with the particles made in the above process, and the temperature of each section of the film blowing machine barrel is 140-150-160-160-160-150°C. Comparative example 1
Embodiment 2
[0050] Premix: firstly add different materials into the high-speed mixer in sequence, and the order of addition is: 1501 (semi-aromatic copolyester), heavy calcium carbonate (1250 mesh), mica powder (1000 mesh), polypropylene carbonate (PPC), monoalkoxy pyrophosphate titanate coupling agent KR- 12. Dicumyl peroxide (DCP) and 1,4-butanediol diglycidyl ether are released after being mixed uniformly in a high-speed mixer. The composition ratio of the blend is shown in Table 3.
[0051] Table 3 Blend composition ratio three
[0052]
[0053] Extrusion granulation: Add the premix into the co-rotating parallel twin-screw extruder for extrusion granulation. The temperature settings are: 120-130-140-140-140-140-140-140-140-140-135-130°C.
[0054] Film blowing: Blow the film with the particles made in the above process, and the temperature of each section of the film blowing machine barrel is 110-120-130-130-130-120 °C.
Embodiment 3
[0060] Premix: First, add different materials into the high-speed mixer in turn, and the feeding order is: polysuccinic acid-terephthalic acid-butylene glycol ester (PBST) (melting point 110-120°C, melting index 3.8g / 10min), sodium sulfate (2000 mesh), wollastonite (2000 mesh), poly 3,4-hydroxybutyrate (P3,4-HB) (melting point 160-170°C, melting index 15.5g / 10min) , di(dioctyl pyrophosphate) glycolate titanate (KR138S), 2,5-dimethyl-2,5-di-tert-butylperoxyhexane, triglycidyl isocyanurate (TGIC), in The high-speed mixer is mixed evenly and released. The composition ratio of the blend is shown in Table 5. Melt index test conditions are: 190°C, 2.16kg.
[0061] Table 5 blend composition ratio five
[0062]
[0063] Extrusion granulation: Add the premix into the co-rotating parallel twin-screw extruder for extrusion granulation. The temperature settings are: 140-150-160-160-160-160-160-160-160-160-155-150°C.
[0064] Film blowing: Blow the film with the particles made in ...
PUM
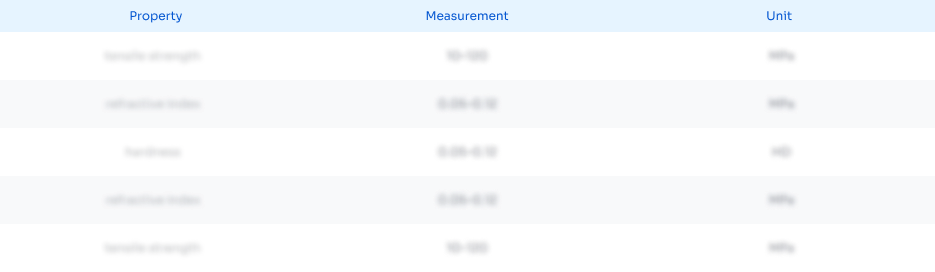
Abstract
Description
Claims
Application Information

- R&D
- Intellectual Property
- Life Sciences
- Materials
- Tech Scout
- Unparalleled Data Quality
- Higher Quality Content
- 60% Fewer Hallucinations
Browse by: Latest US Patents, China's latest patents, Technical Efficacy Thesaurus, Application Domain, Technology Topic, Popular Technical Reports.
© 2025 PatSnap. All rights reserved.Legal|Privacy policy|Modern Slavery Act Transparency Statement|Sitemap|About US| Contact US: help@patsnap.com