Preparation method of polypropylene composite material with high strength and high toughness
A composite material and high toughness technology, which is applied in the fields of fine chemical engineering and chemical engineering, can solve the problems of loss of strength, strength drop, failure to play, etc., and achieve the effects of improving impact toughness, shortening molding cycle, and improving tensile toughness
- Summary
- Abstract
- Description
- Claims
- Application Information
AI Technical Summary
Problems solved by technology
Method used
Image
Examples
preparation example Construction
[0011] The preparation method of polypropylene composite material of the present invention comprises the following steps:
[0012] (1) Put the various materials listed above into the high-speed mixer after weighing in proportion, and fully mix them at a speed of 1000r / min, and release the materials after two minutes for use;
[0013] (2) Put the mixed material into the hopper of the twin-screw extruder, and extrude the material into composite material particles according to the listed process parameters.
[0014] The extrusion process parameters of the polypropylene composite material of the present invention are shown in Table 1.
[0015]
[0016] Table 1
Embodiment 1
[0018] (1) Homopolypropylene (T30S) 0.42Kg, copolymerized polypropylene (K8303) 0.21Kg, copolymerized polypropylene (7726) 0.21Kg, ethylene-octene copolymer (POE) 0.10Kg, polypropylene reinforced toughened modified 0.05Kg of agent, 2g of nucleating agent (SKC-Y5988), 5g of antioxidant (1010), and 3g of oxidized polyethylene wax were put into a high-speed mixer, fully mixed at a speed of 1000r / min, and the material was released after two minutes. standby;
[0019] (2) Put the mixed material into the twin-screw extruder hopper, extrude the material into composite material granules according to the above process parameters, and then inject the material into a standard test sample, in 23 / 50 standard environment ( 23 / 50 is the code name of the standard environment stipulated by the state, which means that the mechanical properties are tested after being placed in a temperature of 23 degrees and a humidity of 50) for 24 hours. The results of the mechanical properties are shown in Ta...
Embodiment 2
[0021] (1) Homopolypropylene (T30S) 0.35Kg, copolymerized polypropylene (K8303) 0.25Kg, copolymerized polypropylene (7726) 0.17Kg, ethylene-octene copolymer (POE) 0.12Kg, reinforced toughened modified polypropylene 0.10Kg of agent, 2.5g of nucleating agent (SKC-Y5988), 4.5g of antioxidant (1010), and 3g of oxidized polyethylene wax were put into the high-speed mixer, fully mixed at a speed of 1000r / min, and released after two minutes material, ready for use;
[0022] (2) Put the mixed material into the twin-screw extruder hopper, extrude the material into composite material granules according to the above process parameters, and then inject the material into a standard test sample, in 23 / 50 standard environment ( 23 / 50 is the code name of the standard environment stipulated by the state, which means that the mechanical properties are tested after being placed in a temperature of 23 degrees and a humidity of 50) for 24 hours. The results of the mechanical properties are shown i...
PUM
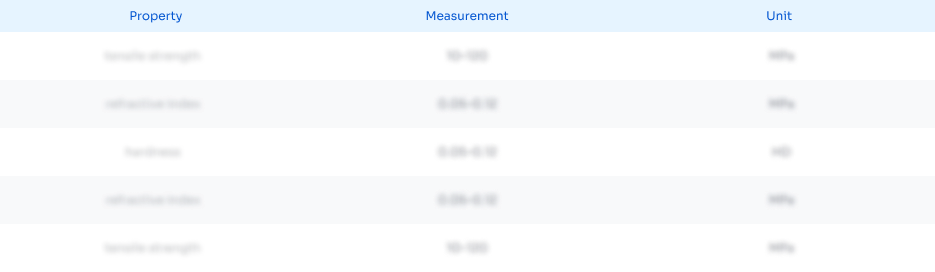
Abstract
Description
Claims
Application Information

- Generate Ideas
- Intellectual Property
- Life Sciences
- Materials
- Tech Scout
- Unparalleled Data Quality
- Higher Quality Content
- 60% Fewer Hallucinations
Browse by: Latest US Patents, China's latest patents, Technical Efficacy Thesaurus, Application Domain, Technology Topic, Popular Technical Reports.
© 2025 PatSnap. All rights reserved.Legal|Privacy policy|Modern Slavery Act Transparency Statement|Sitemap|About US| Contact US: help@patsnap.com