Adhesiveless Copper Clad Laminates And Method For Manufacturing Thereof
a technology of adhesiveless copper clad laminates and adhesives, which is applied in the direction of superimposed coating process, metal adhesion improvement of insulating substrates, transportation and packaging, etc., can solve the problems of trouble and time, limit in narrowing the pitch of the wiring portion on the insulating substrate, and too wide wire pitch width, so as to reduce heat-resisting peel strength, corrosion resistance, and improve insulation reliability
- Summary
- Abstract
- Description
- Claims
- Application Information
AI Technical Summary
Benefits of technology
Problems solved by technology
Method used
Examples
example 1
[0082] A polyimide film (a product name: “Kapton 150EN” manufactured by Du Pont-Toray Co., Ltd.) having a thickness of 38 μm was cut out with a size of 12 cm×12 cm, a Cr—Mo—Ni alloy target in which a Cr ratio is 4 weight % and an Mo ratio is 20 weight % (manufactured by Sumitomo Metal Mining Co., Ltd) was used as a first layer of a base metal layer on one plane of the polyimide film, and a Cr—Mo—Ni alloy base metal layer in which a Cr ratio is 4 weight % and an Mo ratio is 20 weight % was formed by a direct-current sputtering method. When a film thickness of a part of the film formed under the same conditions was separately measured by using a transmission electron microscope (TEM: manufactured by Hitachi Ltd.), it was 20 nm. A copper film layer with a thickness of 200 nm was further formed as a second layer on the film having the Cr—Mo—Ni film formed thereon based on the sputtering method using a Cu target (manufactured by Sumitomo Metal Mining Co., Ltd), and electroplating was use...
example 2
[0085] A raw base metal for evaluation was obtained like Example 1 except that a Cr—Mo—Ni alloy target in which a Cr ratio is 22 weight % and an Mo ratio is 20 weight % (manufactured by Sumitomo Metal Mining Co., Ltd.) was used as a first layer of a base metal layer to form a film of a Cr—Mo—Ni alloy base metal layer in which a Cr ratio is 22 weight % and an Mo ratio is 20 weight % by the direct-current sputtering method.
[0086] When a film thickness of a part of the film formed under the same conditions was separately measured by a transmission electron microscope (TEM: manufactured by Hitachi Ltd.), it was 20 nm. A lead of 1 mm for the peel strength evaluation and a comb-tooth test piece having a 30 μm pitch for the HHBT were formed from this base material by the subtracting method.
[0087] Initial peel strength of the obtained adhesiveless copper clad laminates was 623 N / m. Heat-resisting peel strength after being left in the oven at 150° C. for 168 hours was 597 N / m without a con...
example 3
[0089] A raw base metal for evaluation was obtained like Example 1 except that a Cr—Mo—Ni alloy target in which a Cr ratio is 4 weight % and an Mo ratio is 5 weight % (manufactured by Sumitomo Metal Mining Co., Ltd.) was used as a first layer of a base metal layer to form a film of a Cr—Mo—Ni alloy base metal layer in which a Cr ratio is 4 weight % and an Mo ratio is 5 weight % by the direct-current sputtering method.
[0090] When a film thickness of a part of the film formed under the same conditions was separately measured by a transmission electron microscope (TEM: manufactured by Hitachi Ltd.), it was 20 nm. A lead of 1 mm for the peel strength evaluation and a comb-tooth test piece having a 30 μm pitch for the HHBT were formed from this base material by the subtracting method.
[0091] Initial peel strength of the obtained adhesiveless copper clad laminates was 631 N / m. Heat-resisting peel strength after being left in the oven at 150° C. for 168 hours was 505 N / m without a conside...
PUM
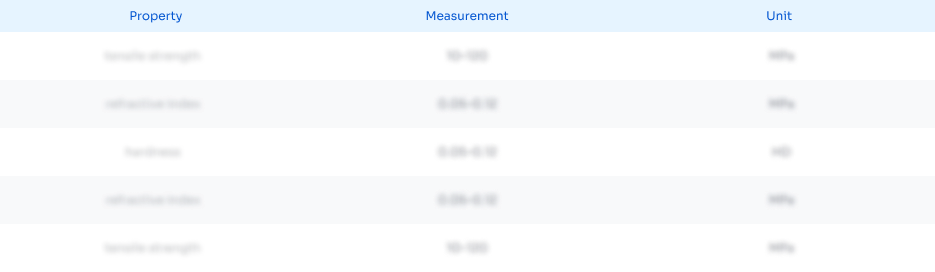
Abstract
Description
Claims
Application Information

- R&D
- Intellectual Property
- Life Sciences
- Materials
- Tech Scout
- Unparalleled Data Quality
- Higher Quality Content
- 60% Fewer Hallucinations
Browse by: Latest US Patents, China's latest patents, Technical Efficacy Thesaurus, Application Domain, Technology Topic, Popular Technical Reports.
© 2025 PatSnap. All rights reserved.Legal|Privacy policy|Modern Slavery Act Transparency Statement|Sitemap|About US| Contact US: help@patsnap.com