Semiconductor memory
a technology of semiconductors and memory, applied in the field of semiconductor memory, can solve the problems of high-speed memory, low access speed, unsuitable for forming large-capacity memory, etc., and achieve the effects of increasing the critical delamination load, enhancing the adhesive strength of chalcogenide materials, and increasing the delamination strength
- Summary
- Abstract
- Description
- Claims
- Application Information
AI Technical Summary
Benefits of technology
Problems solved by technology
Method used
Image
Examples
first embodiment
[0039] A first embodiment of the present invention will be described with reference to FIG. 12. This embodiment provides an example in which conductive adhesive layers are formed both over and under the chalcogenide material layer.
[0040] First of all, a semiconductor substrate 101 is provided, and a MOS transistor is formed on the substrate as a select transistor. Specifically, trench isolation (or device separation) oxide films 102 for isolating the MOS transistor are formed in the surface of the semiconductor substrate 101 by a known selective oxidation technique or shallow trench isolation technique. The present embodiment uses the shallow trench isolation technique, which also can planarize the surface. First, isolation trenches are formed in the substrate by a known dry etching technique. Then, after removing damage left on the sidewalls and bottoms of the trenches in the previous dry etching process, an oxide film is deposited by a known CVD technique. Then, portions of the o...
second embodiment
[0054] A second embodiment of the present invention will be described with reference to FIG. 13. This embodiment provides an example in which: a conductive adhesive layer is formed at the interface between the chalcogenide material layer and the plug; an insulative adhesive layer is formed at the interface between the chalcogenide material layer and the interlayer insulating film; and a conductive adhesive layer is formed at the interface between the chalcogenide material layer and the upper electrode.
[0055] Since the steps before and including the step of forming the tungsten plug 112 are the same as those described in connection with the first embodiment, a description of these steps is not provided herein.
[0056] There will now be described a process of forming an insulative adhesive layer 121 and a conductive adhesive layer 122 on the interlayer insulating film 111 and on the tungsten plug 112, respectively, in a self-aligned manner. First, a titanium layer is deposited on the ...
third embodiment
[0064] A third embodiment of the present invention will be described with reference to FIG. 14. This embodiment provides an example in which a protective film is formed on the sidewalls of the chalcogenide material layer. Since the steps before and including the step of forming the tungsten plug 112 are the same as those described in connection with the first embodiment, a description of these steps is not provided herein.
[0065] First, a chalcogenide material layer 114 of GeSbTe having a thickness of 100 nm and an upper electrode 116 of tungsten having a thickness of 50 nm are sequentially deposited over the entire surfaces of the interlayer insulating film 111 and the tungsten plug 112 by a known sputtering technique. After that, a silicon oxide film 117 is deposited by a known CVD technique. Then, the silicon oxide film 117, the upper electrode 116, and the chalcogenide material layer 114 are sequentially processed by a known lithographic process and dry etching process. It shoul...
PUM
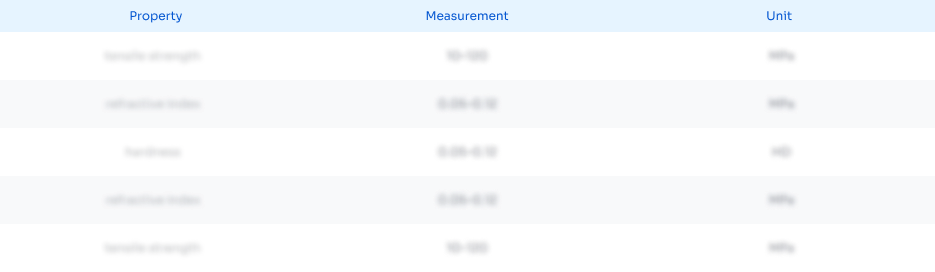
Abstract
Description
Claims
Application Information

- R&D
- Intellectual Property
- Life Sciences
- Materials
- Tech Scout
- Unparalleled Data Quality
- Higher Quality Content
- 60% Fewer Hallucinations
Browse by: Latest US Patents, China's latest patents, Technical Efficacy Thesaurus, Application Domain, Technology Topic, Popular Technical Reports.
© 2025 PatSnap. All rights reserved.Legal|Privacy policy|Modern Slavery Act Transparency Statement|Sitemap|About US| Contact US: help@patsnap.com