Heat-resistant magnesium alloy as well as preparation method and application thereof
A magnesium alloy and heat-resistant technology, applied in the field of heat-resistant magnesium alloys and their preparation, can solve the problems of difficulty in regulating the composition of reinforcement phases, complex interaction of elements, difficult control of components, etc., to achieve enhanced mechanical properties, excellent hardness, and improved resistance. thermal effect
- Summary
- Abstract
- Description
- Claims
- Application Information
AI Technical Summary
Problems solved by technology
Method used
Image
Examples
preparation example Construction
[0050] An embodiment of the present invention also provides a method for preparing a heat-resistant magnesium alloy, including the following steps S10-S20.
[0051] Step S10, providing raw materials for preparation according to the stoichiometric ratio of the above-mentioned heat-resistant magnesium alloy, and making a cast magnesium alloy.
[0052] Step S20, performing solution treatment on the as-cast magnesium alloy obtained in step S10 at 420°C-520°C for 5h-10h, and then performing aging treatment at 200°C-225°C for 10h-30h to obtain a heat-resistant magnesium alloy.
[0053] Preferably, in step S20, the solution treatment includes the following steps:
[0054] The first solid solution treatment is carried out at 470°C to 520°C for 5h to 8h, and then the temperature in the furnace is lowered to 420°C to 460°C for 15min to 80min for the second solid solution treatment.
[0055] Further, after the solution step and before the aging treatment step, a step of quenching the so...
Embodiment 1
[0094] (1) According to the composition of the magnesium alloy: 10.0wt% Gd, 3.0wt% Y, 3.0wt% Sm, 0.5wt% Ag, 0.5wt% Zr, the balance is Mg, and the preparation raw materials are provided: metal Mg, metal Ag, Mg -Gd alloy, Mg-Y alloy, Mg-Sm alloy, Mg-Zr alloy.
[0095] (2) Preheat the crucible, Mg-Sm alloy, Mg-Y alloy, Mg-Gd alloy, and metal Mg to 200°C, and heat the Mg-Sm alloy, Mg-Y alloy, Mg-Gd alloy, and metal Mg according to the melting point Put them into the crucible in turn; when the temperature of the melting furnace rises to 670°C, put the crucible with raw materials and use SF 6 +Ar 2 Then heat up to 740°C and keep warm for melting. After the raw materials are completely melted, skim off the surface scum and mechanically stir for 3 minutes, then add metal Ag and Mg-Zr alloy in turn, and skim off the surface scum after melting. Stir mechanically for 3 minutes; continue to keep warm for 15 minutes, then add refining agent (JDMJ), mechanically stir and refine for 3 minu...
Embodiment 2
[0101] Embodiment 2 is substantially the same as Embodiment 1, and the difference is only that the steps of step (3) are as follows:
[0102] The as-cast magnesium alloy alloy obtained in step (2) was subjected to primary solution treatment at 480°C for 5.5 hours, then gradually lowered to 460°C at a cooling rate of 5°C / min, and subjected to secondary solution treatment for 60 minutes, followed by chamber Warm water quenching, aging the quenched magnesium alloy at 210°C for 20 hours, cooling to obtain Mg-10Gd-3Y-3Sm-0.5Ag-0.5Zr magnesium alloy, the total content of impurity elements is less than 0.03wt%. The composition of the magnesium alloy is shown in Table 1.
[0103] Other steps and processing parameter are identical with embodiment 1.
[0104] The electron micrograph of the magnesium alloy that embodiment 2 obtains, as image 3 Shown: In the microstructure of the magnesium alloy, there are a large number of dispersed precipitates in the grain boundary and in the grain,...
PUM
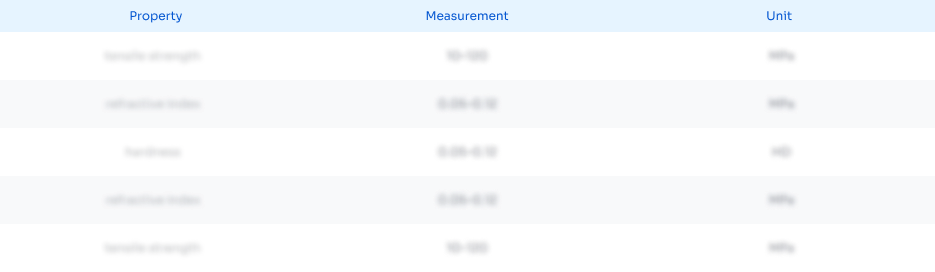
Abstract
Description
Claims
Application Information

- R&D
- Intellectual Property
- Life Sciences
- Materials
- Tech Scout
- Unparalleled Data Quality
- Higher Quality Content
- 60% Fewer Hallucinations
Browse by: Latest US Patents, China's latest patents, Technical Efficacy Thesaurus, Application Domain, Technology Topic, Popular Technical Reports.
© 2025 PatSnap. All rights reserved.Legal|Privacy policy|Modern Slavery Act Transparency Statement|Sitemap|About US| Contact US: help@patsnap.com