Aluminum alloy sacrificial anode material capable of improving protection effect of water/gas interface of sewage storage tank and preparation method thereof
A technology of interface protection and sacrificial anode, which is applied in the field of metal corrosion and protection, can solve the problems of undetected protection effect of Al-Zn-In aluminum alloy, peeling off of the anode surface, and poor protection effect, so as to improve the electrochemical performance. performance, reduced current efficiency, uniform effect of surface corrosion and dissolution
- Summary
- Abstract
- Description
- Claims
- Application Information
AI Technical Summary
Problems solved by technology
Method used
Image
Examples
preparation example Construction
[0032] The preparation method of the aluminum alloy sacrificial anode material comprises the following steps:
[0033] 1) During the whole process of continuously feeding inert gas for protection, put an aluminum ingot with a purity of 99.99% into a graphite crucible for melting, and heat it up to a predetermined temperature to completely melt it to obtain liquid aluminum;
[0034] 2) After melting and holding for 30 to 35 minutes, add Zn to the molten aluminum according to the ratio, melt and stir evenly, then add other alloying elements In, Mg and Sn in turn until completely melted, stir gently, then remove slag, and keep warm;
[0035] 3) Finally, cast into a mold and cool to room temperature, so as to prepare the aluminum alloy casting.
[0036] In step (1), the inert gas is nitrogen. The melting temperature is 770°C to 790°C.
[0037] In step (2), the holding time after slag removal is 2-2.5 hours.
[0038] In step (3), the pouring temperature is 710°C to 730°C.
Embodiment 1
[0040]First put high-purity aluminum ingots (purity 99.99%) into a graphite crucible melting furnace, raise the temperature to 780°C to melt it into molten aluminum, and then add 3.7% Zn, 0.03% In, 0.45 %Mg, 0.065% Sn, stir evenly, and keep warm for 30min after the temperature rises to 780°C. Then stir and remove the slag. After fully stirring, keep it warm at 780°C for 2 hours to make it uniform. Finally, the melt is poured into the mold at a pouring temperature of 710°C. After the casting is cooled to room temperature, the aluminum alloy casting can be prepared; during the whole smelting process, an inert gas nitrogen is used to protect the melt to reduce the burning loss of alloying elements. After the smelting is completed, the alloy composition of the sample is detected by inductively coupled plasma emission spectrometer (ICP), and the actual chemical composition is basically the same as the design composition.
Embodiment 2
[0042] First, put the high-purity aluminum ingot (purity 99.99%) into the graphite crucible melting furnace, raise the temperature to 770°C to melt it into molten aluminum, and then add 3.0% Zn, 0.01% In, 0.4 %Mg, 0.01% Sn, stir evenly, and keep warm for 30min after the temperature rises to 770°C. Then stir and remove the slag. After fully stirring, keep it warm at 770°C for 2.2h to make it uniform. Finally, the melt is poured into the mold, and the pouring temperature is 715°C. After the casting is cooled to room temperature, the aluminum alloy casting can be prepared; during the whole smelting process, an inert gas nitrogen is used to protect the melt to reduce the burning loss of alloying elements. After the smelting is completed, the alloy composition of the sample is detected by inductively coupled plasma emission spectrometer (ICP), and the actual chemical composition is basically the same as the design composition.
PUM
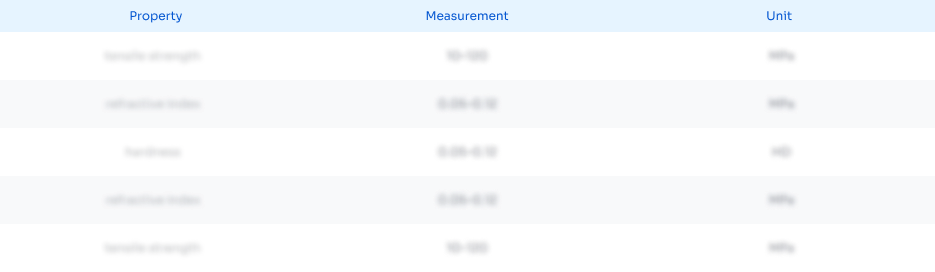
Abstract
Description
Claims
Application Information

- R&D Engineer
- R&D Manager
- IP Professional
- Industry Leading Data Capabilities
- Powerful AI technology
- Patent DNA Extraction
Browse by: Latest US Patents, China's latest patents, Technical Efficacy Thesaurus, Application Domain, Technology Topic, Popular Technical Reports.
© 2024 PatSnap. All rights reserved.Legal|Privacy policy|Modern Slavery Act Transparency Statement|Sitemap|About US| Contact US: help@patsnap.com