Preparation method of ceramic-metal composite material
A metal composite material and ceramic technology, which is applied in metal processing equipment, ceramic molding machines, manufacturing tools, etc., can solve the limited use conditions of mechanical connection and adhesive connection process, the complex solid phase diffusion connection process, and the processing of connection equipment. The requirements are very high, and the signal shielding characteristics and the metal ductility are good, the interface is tight, and the mirror effect is good.
- Summary
- Abstract
- Description
- Claims
- Application Information
AI Technical Summary
Problems solved by technology
Method used
Image
Examples
Embodiment 1
[0020] The domestic 316L stainless steel powder and binder were added to an open-close mixer with a powder loading of 45.5% and mixed for 2 hours. After crushing in a crusher, they were poured into an extruder for extrusion and granulation. The domestic black zirconia powder and binder are added to the open-close mixer according to the powder loading of 50% and mixed for 2 hours. The mixing temperature is 190°C. into the extruder for extrusion and granulation. First inject 316L stainless steel feed material, the injection temperature is 195°C, the injection pressure is 100MPa, the injection filling speed is 100mm / s, and the mold temperature is 120°C. Then the injection blank is cut out with a laser cutting machine to cut off the cut piece including the gate. Place the cut piece on the mold, and then inject the black zirconia feed material to fill the cut-off part of the laser cutting. The injection temperature is 195°C, the injection pressure is 65MPa, the injection filling s...
Embodiment 2
[0022] The domestic 316L stainless steel powder and binder were added to an open-close mixer with a powder loading of 46.4% and mixed for 2 hours. After crushing in a crusher, they were poured into an extruder for extrusion and granulation. The domestic black zirconia powder and binder are added to the open-close mixer according to the powder loading of 50% and mixed for 2 hours. The mixing temperature is 190°C. into the extruder for extrusion and granulation. First inject 316L stainless steel feed material, the injection temperature is 190°C, the injection pressure is 150MPa, the injection filling speed is 120mm / s, and the mold temperature is 130°C. Then use black zirconia feed to inject the remaining parts of the product. During injection, the injection temperature is 190°C, the injection pressure is 120MPa, the injection filling speed is 90mm / s, and the mold temperature is 140°C. In this way, an injection blank with metal-wrapped ceramics, a certain strength interface and ...
PUM
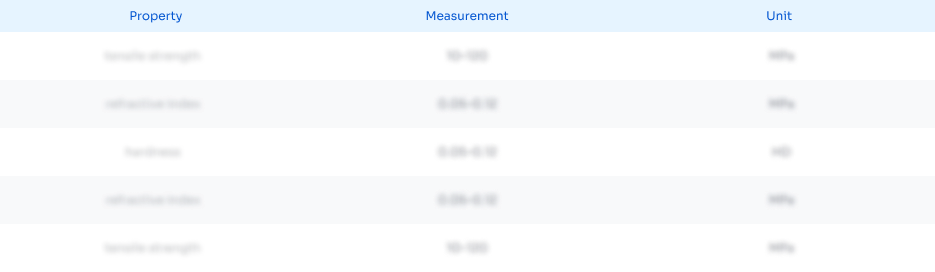
Abstract
Description
Claims
Application Information

- R&D
- Intellectual Property
- Life Sciences
- Materials
- Tech Scout
- Unparalleled Data Quality
- Higher Quality Content
- 60% Fewer Hallucinations
Browse by: Latest US Patents, China's latest patents, Technical Efficacy Thesaurus, Application Domain, Technology Topic, Popular Technical Reports.
© 2025 PatSnap. All rights reserved.Legal|Privacy policy|Modern Slavery Act Transparency Statement|Sitemap|About US| Contact US: help@patsnap.com