Method for recycling organic matters of paste and slurry-shaped waste by a multi-hearth furnace coupling gas stripping pyrolysis method
A process heat, multi-hearth furnace technology, applied in the direction of combustion methods, incinerators, lighting and heating equipment, etc., can solve the problems of combustion unit shutdown, shutdown, and "dramatic increase in area" to achieve the effect of reducing hot spots
- Summary
- Abstract
- Description
- Claims
- Application Information
AI Technical Summary
Problems solved by technology
Method used
Image
Examples
Embodiment
[0072] The method for recovering the organic matter of paste waste by pyrolysis method in the multi-hearth furnace coupling gas stripping process of this embodiment is carried out according to the following steps, and the process flow chart is as follows figure 1 Shown:
[0073] (1) Homogenize the slurry-like waste material in a homogenizing tank;
[0074] (2) Send the homogenized slurry-like waste into the feeder with a mud cake delivery pump;
[0075] (3) Send the homogenized paste-like waste into the multi-furnace pyrolysis treatment system through a feeder;
[0076] (4) Provide heat for the multi-furnace pyrolysis treatment system through the fireplace burner and external burner. There are at least six layers of furnaces in the multi-furnace pyrolysis treatment system; the homogenized paste-like waste passes through from top to bottom The first layer of furnace, the second layer of furnace, the third layer of furnace, the fourth layer of furnace, the fifth layer of furna...
PUM
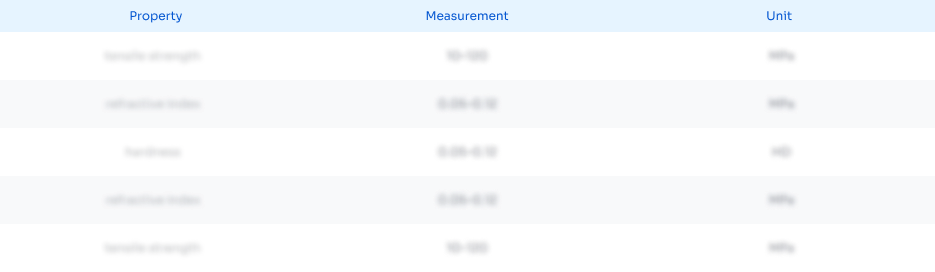
Abstract
Description
Claims
Application Information

- R&D Engineer
- R&D Manager
- IP Professional
- Industry Leading Data Capabilities
- Powerful AI technology
- Patent DNA Extraction
Browse by: Latest US Patents, China's latest patents, Technical Efficacy Thesaurus, Application Domain, Technology Topic, Popular Technical Reports.
© 2024 PatSnap. All rights reserved.Legal|Privacy policy|Modern Slavery Act Transparency Statement|Sitemap|About US| Contact US: help@patsnap.com