Aluminum and molybdenum high-temperature-resistant nodular cast iron containing chromium and copper elements and preparation method thereof
A technology of ductile iron and high temperature resistance, applied in the field of aluminum molybdenum high temperature ductile iron, can solve the problems of high temperature resistance, high manufacturing cost and high cost, achieve good preparation formability and comprehensive mechanical properties, improve high temperature performance and high temperature Antioxidant ability, the effect of broad commercial application prospects
- Summary
- Abstract
- Description
- Claims
- Application Information
AI Technical Summary
Problems solved by technology
Method used
Examples
Embodiment 1
[0019] An aluminum-molybdenum high-temperature-resistant ductile iron containing chromium and copper elements, the weight percentage of each component is: C 1.4%, Si 5.2%, Al 2.0%, Mo 0.9%, Cr 0.5%, Cu 1.5%; impurity element Mg≦ 0.06%, impurity element S≦0.06%, impurity element P≦0.15%, impurity element Mn≦0.7%, and the rest is Fe. Its concrete preparation steps are:
[0020] a. Batching smelting, configure the alloy according to the above target components, add 150 kg of cast iron and 150 kg of scrap steel into an intermediate frequency induction furnace with a standard capacity of 500 kg, and after the metal is melted, add industrial ferrosilicon, industrial ferromolybdenum, and ferrochrome 1. The copper wire reaches the above design composition, and the industrial pure aluminum ingot is added through the bell jar pressing method. During the smelting process of the ingredients, it is considered that about 5% of C will be burned, and the subsequent inoculation process will in...
Embodiment 2
[0025] An aluminum-molybdenum high-temperature-resistant ductile iron containing chromium and copper elements, the weight percentage of each component is: C 3.6%, Si 1.5%, Al9.0%, Mo 0.3%, Cr 0.5%, Cu 0.3%; impurity element Mg≦ 0.06%, impurity element S≦0.06%, impurity element P≦0.15%, impurity element Mn≦0.7%, and the rest is Fe. Its concrete preparation steps are:
[0026] a. Batching smelting, configure the alloy according to the above target components, add 150 kg of cast iron and 150 kg of scrap steel into an intermediate frequency induction furnace with a standard capacity of 500 kg, and after the metal is melted, add industrial ferrosilicon, industrial ferromolybdenum, and ferrochrome 1. The copper wire reaches the above design composition, and the industrial pure aluminum ingot is added through the bell jar pressing method. During the smelting process of the ingredients, it is considered that about 5% of C will be burned, and the subsequent inoculation process will inc...
Embodiment 3
[0031] An aluminum-molybdenum high-temperature-resistant ductile iron containing chromium and copper elements, the weight percentage of each component is: C 3.0%, Si 3.8%, Al 5.0%, Mo 3.0%, Cr 2.5%, Cu 1.5%; impurity element Mg≦ 0.06%, impurity element S≦0.06%, impurity element P≦0.15%, impurity element Mn≦0.7%, and the rest is Fe. Its concrete preparation steps are:
[0032] a. Batching smelting, configure the alloy according to the above target components, add 150 kg of cast iron and 150 kg of scrap steel into an intermediate frequency induction furnace with a standard capacity of 500 kg, and after the metal is melted, add industrial ferrosilicon, industrial ferromolybdenum, and ferrochrome 1. The copper wire reaches the above design composition, and the industrial pure aluminum ingot is added through the bell jar pressing method. During the smelting process of the ingredients, it is considered that about 5% of C will be burned, and the subsequent inoculation process will in...
PUM
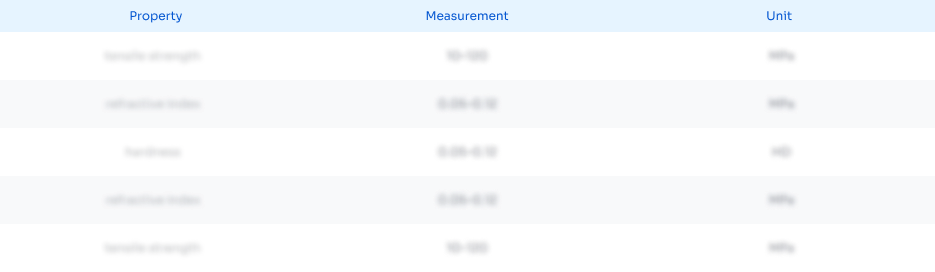
Abstract
Description
Claims
Application Information

- Generate Ideas
- Intellectual Property
- Life Sciences
- Materials
- Tech Scout
- Unparalleled Data Quality
- Higher Quality Content
- 60% Fewer Hallucinations
Browse by: Latest US Patents, China's latest patents, Technical Efficacy Thesaurus, Application Domain, Technology Topic, Popular Technical Reports.
© 2025 PatSnap. All rights reserved.Legal|Privacy policy|Modern Slavery Act Transparency Statement|Sitemap|About US| Contact US: help@patsnap.com