A preparing method of heavy-duty anticorrosion coating
A heavy-duty anti-corrosion and coating technology, which is applied in the direction of anti-corrosion coatings, powder coatings, epoxy resin coatings, etc., can solve problems such as insufficient dispersion, surface color separation, and sickness of paint films, so as to improve mechanical properties and corrosion resistance. The effect of interlayer adhesion and simple preparation process
- Summary
- Abstract
- Description
- Claims
- Application Information
AI Technical Summary
Problems solved by technology
Method used
Image
Examples
Embodiment 1
[0023] A preparation method for heavy-duty coating, comprising the following steps:
[0024] (1) Mixing
[0025] Add resin, pigments and fillers, graphene, solvents and additives into the disperser in proportion. During the feeding process, the dispersing disc of the dispersing machine keeps rotating at a speed of 400-500r / min. After the materials are put in, adjust the rotating speed of the dispersing disc to 1800 -2000r / min, stop after 1h.
[0026] In this step, the mass percentage of each component in the step (1) is: resin 20-45%, pigment and filler 30-55%, graphene 0.5-1%, solvent 5-25%, additive 0.5-2% %.
[0027] In this step, the resin is any one of normal temperature curing novolak epoxy resin F-44, epoxy resin E-20, epoxy resin E-44, fluorocarbon resin JF-2x, acrylic resin or alkyd resin . Wherein, when the resin is solid, the solid resin needs to be crushed into powder before use, and the size of the powder is not limited, as long as it can be quickly dissolved ...
Embodiment 2
[0036] A preparation method for heavy-duty coating, comprising the following steps:
[0037] (1) Mixing
[0038] The mass percentage is 39% room temperature curing novolak epoxy resin F-44, 12% sericite, 19% iron red, 5% ultrafine talcum powder, 9% aluminum tripolyphosphate, 4% poly Zinc phosphate, 5% of VT600, 1% of organic bentonite, 0.5% of intrinsic graphene, 4% of xylene, 1% of n-butanol and 0.5% of dispersant are added to the disperser. During the feeding process, the dispersion The dispersing disc of the machine keeps rotating at a speed of 400r / min. After the material is put in, adjust the rotating speed of the dispersing disc to 1800r / min, and stop after keeping it for 1h.
[0039] (2) grinding
[0040] Replace the dispersing disk with a sanding disk, and make the sanding disk grind the material at 2800r / min. During the grinding process, stop the machine every 2 hours to check the fineness until the fineness reaches 40um, stop the machine to discharge the material, ...
Embodiment 3
[0042] A preparation method for heavy-duty coating, comprising the following steps:
[0043] (1) Mixing
[0044] The mass percentage is 20% epoxy resin E-44, 14% sericite, 16% iron red, 16% superfine talcum powder, 8% aluminum tripolyphosphate, 1% organic bentonite, 1% Intrinsic state graphene, 12.8% xylene, 10% n-butanol, 1% dispersant, 0.2% defoamer are added to the disperser, and during the feeding process, the dispersing disc of the disperser maintains 500r / min After the material is put in, adjust the speed of the dispersing disc to 2000r / min, keep it for 1h and then stop.
[0045] (2) grinding
[0046] Replace the dispersing disk with a sanding disk, and make the sanding disk grind the material at 2000r / min. During the grinding process, stop the machine every 2 hours to check the fineness until the fineness reaches 40um, stop the machine to discharge the material, and filter to remove impurities to obtain the finished paint.
PUM
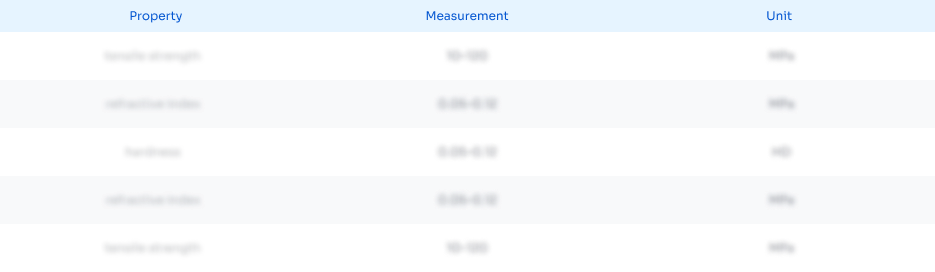
Abstract
Description
Claims
Application Information

- R&D Engineer
- R&D Manager
- IP Professional
- Industry Leading Data Capabilities
- Powerful AI technology
- Patent DNA Extraction
Browse by: Latest US Patents, China's latest patents, Technical Efficacy Thesaurus, Application Domain, Technology Topic, Popular Technical Reports.
© 2024 PatSnap. All rights reserved.Legal|Privacy policy|Modern Slavery Act Transparency Statement|Sitemap|About US| Contact US: help@patsnap.com