Multi-main-element alloy for cutter and preparation method of multi-main-element alloy
A multi-principal alloy and cutting tool technology, which is applied in the direction of improving process efficiency and energy efficiency, can solve problems such as high melting point, achieve low sintering temperature, high production efficiency, and inhibit the formation of intermetallic compounds.
- Summary
- Abstract
- Description
- Claims
- Application Information
AI Technical Summary
Problems solved by technology
Method used
Image
Examples
Embodiment 1
[0017] Weigh 0.40mol of aluminum powder, cobalt powder, copper powder, iron powder, manganese powder and nickel powder according to the chemical formula AlCoCuFeMnNi, and the purity of each pure metal powder is higher than 99.5%; Add an appropriate amount of stainless steel balls to the ball milling jar, and then seal the ball milling jar with pure metal powder under a nitrogen atmosphere; place the above sealed ball milling jar on a planetary ball mill for mixing, and the mixing speed is 250rpm , the time is 0.5h; put the powder after the above uniform mixing into the graphite mold under the protection of nitrogen gas, and then put the graphite mold into the discharge plasma sintering furnace; load an initial pre-pressure of 10MPa on the graphite mold, and then put the The furnace cavity is evacuated to below 100Pa, and the temperature is rapidly raised to 900°C, kept for 2 hours, and the sintering is completed to obtain the required multi-principal alloy.
Embodiment 2
[0019] Weigh 0.40mol of aluminum powder, cobalt powder, copper powder, iron powder, manganese powder, nickel powder and zinc powder according to the chemical formula AlCoCuFeMnNiZn, and the purity of each pure metal powder is higher than 99.5%; Put the metal powder in a ball mill jar, add an appropriate amount of stainless steel balls, and then seal the ball mill jar with pure metal powder under a nitrogen atmosphere; put the above sealed ball mill jar on a planetary ball mill for mixing. The rotation speed is 200rpm, and the time is 1.5h; put the above-mentioned uniformly mixed powder into the graphite mold under the protection of nitrogen gas, and then put the graphite mold into the discharge plasma sintering furnace; load an initial pre-set pressure of 9MPa on the graphite mold , and then evacuate the furnace cavity to below 100Pa, quickly raise the temperature to 1100°C, keep it warm for 1.5h, and sinter to obtain the required multi-principal alloy.
Embodiment 3
[0021] According to the chemical formula Al 0.6 CoCuFeMnNiZn weighs 0.24mol of aluminum powder and 0.40mol of cobalt powder, copper powder, iron powder, manganese powder, nickel powder and zinc powder respectively, and the purity of each pure metal powder is higher than 99.5%; Put the pure metal powder in a ball mill jar, add an appropriate amount of stainless steel balls, and then seal the ball mill jar with the pure metal powder in an argon atmosphere; place the sealed ball mill jar on a planetary ball mill for mixing, The mixing speed is 150rpm, and the time is 3h; put the above uniformly mixed powder into the graphite mold under the protection of nitrogen gas, and then put the graphite mold into the discharge plasma sintering furnace; load an initial pre-pressure on the graphite mold 8MPa, then evacuate the furnace cavity to below 100Pa, rapidly raise the temperature to 1200°C, keep it for 1h, and sinter to obtain the required multi-principal alloy.
PUM
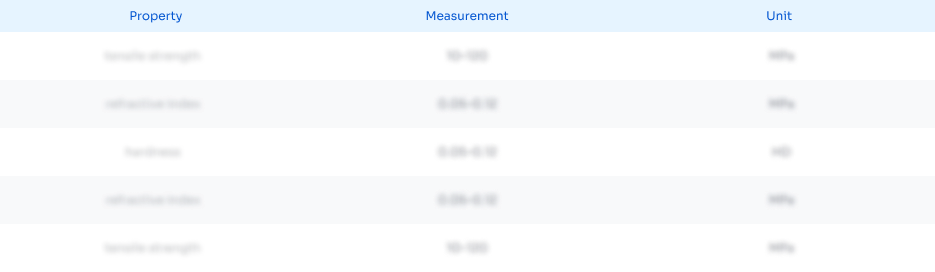
Abstract
Description
Claims
Application Information

- Generate Ideas
- Intellectual Property
- Life Sciences
- Materials
- Tech Scout
- Unparalleled Data Quality
- Higher Quality Content
- 60% Fewer Hallucinations
Browse by: Latest US Patents, China's latest patents, Technical Efficacy Thesaurus, Application Domain, Technology Topic, Popular Technical Reports.
© 2025 PatSnap. All rights reserved.Legal|Privacy policy|Modern Slavery Act Transparency Statement|Sitemap|About US| Contact US: help@patsnap.com