Ultra-heat-resistant high-temperature-resistant coating for exhaust equipment
A technology for high-temperature resistant coatings and exhaust equipment, applied in the direction of fire-resistant coatings, epoxy resin coatings, coatings, etc., can solve the problems of low compatibility and reduced comprehensive performance of materials, and achieve high coating rate and easy construction , good dispersion effect
- Summary
- Abstract
- Description
- Claims
- Application Information
AI Technical Summary
Problems solved by technology
Method used
Examples
Embodiment Construction
[0013] A super-heat-resistant and high-temperature-resistant coating for exhaust equipment, prepared from the following raw materials in parts by weight (kg): magnesia fine powder 2.8, phenolic epoxy resin F5130, bisphenol epoxy resin 50, n-butanol 15 , modified aliphatic curing agent 22802, nano-chitin 2.2, tributyl citrate 4, glycerol 2, asbestos powder 3, waste ceramic powder 1.5, fly ash 18, dimethyl siloxane 0.7, sea foam Stone wool 3, aluminum powder 8, sodium tripolyphosphate 1, styrene 12, azobisisobutyronitrile 1.2, rare earth coupling agent 0.2, palmitic acid 0.3, styrene-acrylic emulsion 8, butyl methacrylate 1, polyethylene Alcohol 0.6, benzoyl peroxide 0.2, absolute ethanol amount.
[0014] The super-heat-resistant and high-temperature-resistant coating for the exhaust equipment is prepared by the following specific steps:
[0015] (1) Calcinate the fly ash at 600°C for 3 hours, then soak it in deionized water for 8 hours while it is hot, filter and dry it, then ...
PUM
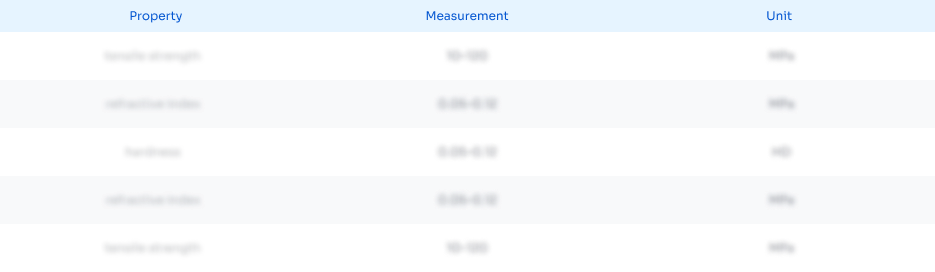
Abstract
Description
Claims
Application Information

- R&D Engineer
- R&D Manager
- IP Professional
- Industry Leading Data Capabilities
- Powerful AI technology
- Patent DNA Extraction
Browse by: Latest US Patents, China's latest patents, Technical Efficacy Thesaurus, Application Domain, Technology Topic, Popular Technical Reports.
© 2024 PatSnap. All rights reserved.Legal|Privacy policy|Modern Slavery Act Transparency Statement|Sitemap|About US| Contact US: help@patsnap.com