Microalloying method capable of improving performance of steel for large heat input welding
A high-energy-energy welding and micro-alloying technology, which is applied in the field of low-alloy steel manufacturing, can solve the problems of restricting the refinement of the structure of the heat-affected zone and promoting the formation of intragranular acicular ferrite and other problems, so as to achieve low production costs. , Refine grain, control simple effect
- Summary
- Abstract
- Description
- Claims
- Application Information
AI Technical Summary
Problems solved by technology
Method used
Image
Examples
Embodiment 1
[0040] A kind of Mo-Nb-Mg-Ti microalloying method that improves the performance of steel for high heat input welding, specifically as follows:
[0041] The process of smelting high-energy-input welding steel is 120t top-bottom combined blowing converter-120tLF ladle furnace refining-continuous casting.
[0042] Conditions of molten iron: molten iron [P]≤0.090%, [S]≤0.045%.
[0043] Converter: end target [C]=0.04~0.06%, [P]≤0.015%, [S]≤0.030%, [O]=500~800ppm, tapping temperature 1685℃, adding ferromolybdenum and manganese during tapping Iron, ferrosilicon, ferroniobium, ferroaluminum.
[0044] LF: The refining time is 40 minutes, and the net blowing time of argon after calcium treatment is 8 minutes. During the net blowing, the liquid surface of molten steel should not be exposed. The temperature of molten steel entering the station is 1585°C for the first furnace and 1580°C for the continuous pouring furnace. After entering the station, the feeding amount of the aluminum wi...
Embodiment 2
[0048] A kind of Mo-Nb-Mg-Ti microalloying method that improves the performance of steel for high heat input welding, specifically as follows:
[0049] The process of smelting high-energy-input welding steel is 120t top-bottom combined blowing converter-120tLF ladle furnace refining-continuous casting.
[0050] Conditions of molten iron: molten iron [P]≤0.090%, [S]≤0.045%.
[0051] Converter: end target [C]=0.04~0.06%, [P]≤0.015%, [S]≤0.030%, [O]=500~800ppm, tapping temperature 1680℃, adding ferromolybdenum and manganese during tapping Iron, ferrosilicon, ferroniobium, ferroaluminum.
[0052] LF: The refining time is 45 minutes, and the net blowing time of argon after calcium treatment is 10 minutes. During the net blowing, the liquid surface of molten steel should not be exposed. The temperature of molten steel entering the station is 1580°C for the first furnace and 1575°C for the continuous pouring furnace. After entering the station, the feeding amount of the aluminum w...
Embodiment 3
[0056] A kind of Mo-Nb-Mg-Ti microalloying method that improves the performance of steel for high heat input welding, specifically as follows:
[0057] The process of smelting high-energy-input welding steel is 120t top-bottom combined blowing converter-120tLF ladle furnace refining-continuous casting.
[0058] Conditions of molten iron: molten iron [P]≤0.090%, [S]≤0.045%.
[0059] Converter: end target [C]=0.04~0.06%, [P]≤0.015%, [S]≤0.030%, [O]=500~800ppm, tapping temperature 1670℃, adding ferromolybdenum and manganese during tapping Iron, ferrosilicon, ferroniobium, ferroaluminum.
[0060] LF: The refining time is 42 minutes, and the net blowing time of argon after calcium treatment is 6 minutes. During the net blowing, the liquid surface of molten steel should not be exposed. The temperature of molten steel entering the station is 1590°C for the first furnace and 1585°C for the continuous pouring furnace. After entering the station, the feeding amount of the aluminum wi...
PUM
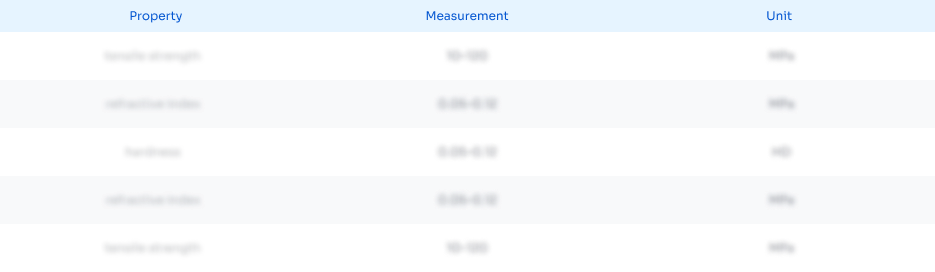
Abstract
Description
Claims
Application Information

- R&D Engineer
- R&D Manager
- IP Professional
- Industry Leading Data Capabilities
- Powerful AI technology
- Patent DNA Extraction
Browse by: Latest US Patents, China's latest patents, Technical Efficacy Thesaurus, Application Domain, Technology Topic, Popular Technical Reports.
© 2024 PatSnap. All rights reserved.Legal|Privacy policy|Modern Slavery Act Transparency Statement|Sitemap|About US| Contact US: help@patsnap.com