A method for preparing gallium nitride nanocrystals using a twin-screw extruder
A twin-screw extruder, gallium nitride nanotechnology, applied in chemical instruments and methods, nanotechnology for materials and surface science, inorganic chemistry, etc., can solve the problem of difficult to popularize large-scale industrial production of gallium nitride nanocrystals. , Precursor nanorods are not conducive to the growth of gallium nitride crystals, affecting the quality of gallium nitride nanocrystals, etc., to achieve the effects of easy promotion and large-scale production, low production technical requirements, and short synthesis time
- Summary
- Abstract
- Description
- Claims
- Application Information
AI Technical Summary
Problems solved by technology
Method used
Examples
Embodiment 1
[0025] (1) Prepare polyacrylamide and water to make a polyacrylamide aqueous solution with a concentration of 60 g / L, mix gallium nitrate powder into the polyacrylamide aqueous solution, and the amount of polyacrylamide is 12% of the amount of gallium nitrate; Stir and mix at a speed of 3000 rpm in a high-speed mixer for 20 min to obtain a mixed slurry;
[0026] (2) Pump the slurry obtained in step (1) into the feeding port of the twin-screw extruder, set the reaction temperature of the dispersing thread element section to 100°C, and pass the slurry through the dispersing thread element, so that the gallium salt is coated on the polyacrylamide In the formed hydrogel network structure; then by shearing and carbonizing the threaded element, set the reaction temperature of this section to 240°C, and carbonize the polyacrylamide molecules under shear and high temperature conditions to form a gallium salt covered by the carbon network structure ; Add 4% thermoplastic polyurethane w...
Embodiment 2
[0030](1) Prepare polyacrylic acid and water to make a polyacrylic acid aqueous solution with a concentration of 90 g / L, mix gallium chloride powder into the polyacrylic acid aqueous solution, and the amount of polyacrylic acid is 15% of the amount of gallium chloride; Stir and mix at a speed of 3500rpm for 15 min to obtain a mixed slurry;
[0031] (2) Pump the slurry obtained in step (1) into the feeding port of the twin-screw extruder, set the reaction temperature of the dispersing screw element section to 120 °C, and pass the slurry through the dispersing screw element, so that the gallium salt is coated on the polyacrylic acid to form In the hydrogel network structure; then by shearing the carbonized screw element, set the reaction temperature of this section to 200 ° C, and carbonize the polyacrylic acid molecules under shear and high temperature conditions to form a gallium salt covered by the carbon network structure; Add thermoplastic acrylic acid with an amount of 5% ...
Embodiment 3
[0035] (1) Prepare polyethylene glycol and water to make a polyethylene glycol aqueous solution with a concentration of 100 g / L, mix gallium acetate powder into the polyethylene glycol aqueous solution, and the amount of polyethylene glycol is equal to the amount of gallium acetate 18%; In a high-speed mixer, stir and mix at a speed of 4000rpm for 15 min to obtain a mixed slurry;
[0036] (2) Pump the slurry obtained in step (1) into the feed port of the twin-screw extruder, set the reaction temperature of the dispersing screw element section to 150°C, and pass the slurry through the dispersing screw element to coat the gallium salt on the polyethylene In the hydrogel network structure formed by alcohol; then by shearing and carbonizing the screw element, set the reaction temperature of this section to 200°C, and carbonize the polyethylene glycol molecules under the conditions of shearing and high temperature to form a carbon network structure-coated Gallium salt; add thermopl...
PUM
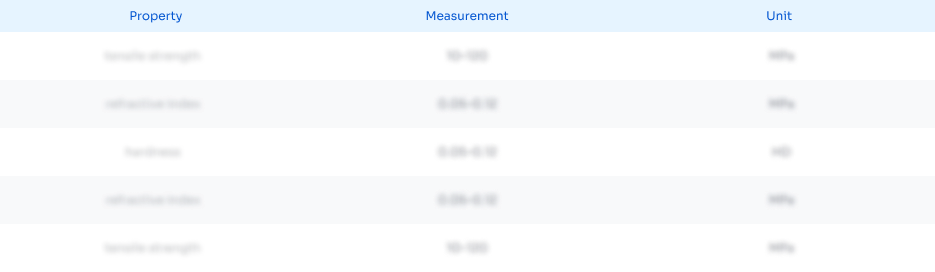
Abstract
Description
Claims
Application Information

- R&D
- Intellectual Property
- Life Sciences
- Materials
- Tech Scout
- Unparalleled Data Quality
- Higher Quality Content
- 60% Fewer Hallucinations
Browse by: Latest US Patents, China's latest patents, Technical Efficacy Thesaurus, Application Domain, Technology Topic, Popular Technical Reports.
© 2025 PatSnap. All rights reserved.Legal|Privacy policy|Modern Slavery Act Transparency Statement|Sitemap|About US| Contact US: help@patsnap.com