Aluminum-silicon-copper-yttrium solder for silicon carbide particle reinforced aluminum matrix composite soldering and preparation method for aluminum-silicon-copper-yttrium solder
A silicon carbide particle-reinforced aluminum-based technology, applied in welding equipment, welding/cutting media/materials, welding media, etc., can solve problems such as high stress at the joint, continuity of the split alloy matrix, and loose brazing seam structure, etc., to achieve Increase the ductility of the alloy, avoid welding difficulties, and improve the wettability effect
- Summary
- Abstract
- Description
- Claims
- Application Information
AI Technical Summary
Problems solved by technology
Method used
Image
Examples
Embodiment 1
[0031] Put 32g of pure Al and 42.5g of Al-20Si alloy in the crucible of a vacuum induction melting furnace, vacuumize and fill it with high-purity argon; then heat it up to 750°C rapidly to completely melt the alloy in the crucible, and then pass through the induction furnace The feeding device adds 25g of pure Cu into the molten Al-Si alloy liquid to form an Al-Si-Cu alloy; after melting evenly, add 0.5g of Al-10Y alloy through the feeding device to make it mix Fully react, add magnetic stirring, keep warm at 600°C for 20-30min, then let stand for about 3 minutes, pour into metal mold, cool and solidify in argon atmosphere; Evenly spread, and finally cast into rods.
Embodiment 2
[0033] Put 31.5g of pure Al and 42.5g of Al-20Si alloy in the crucible of a vacuum induction melting furnace, vacuumize and fill it with high-purity argon; then heat it up to 750°C rapidly to completely melt the alloy in the crucible, and then pass through the induction furnace Add 25g of pure Cu into the molten Al-Si alloy liquid to form Al-Si-Cu alloy; after melting evenly, add 1g of Al-10Y alloy through the feeding device to make it melt with Al-Si-Cu alloy The solution is fully reacted, stirred by magnetic force, kept at 600°C for 30-40 minutes, then left to stand for about 3 minutes, poured into a metal mold, cooled and solidified in an argon atmosphere; after taking it out, remelt twice in the same way to make each The components spread evenly and are finally cast into rods.
Embodiment 3
[0035] Put 28.5g of pure Al and 42.5g of Al-20Si alloy in the crucible of a vacuum induction melting furnace, vacuumize and fill it with high-purity argon; then heat it up to 750°C rapidly to completely melt the alloy in the crucible, and then pass through the induction furnace Add 25g of pure Cu into the molten Al-Si alloy liquid to form Al-Si-Cu alloy; after melting evenly, add 4g of Al-10Y alloy through the feeding device to make it melt with Al-Si-Cu alloy The solution is fully reacted, stirred by magnetic force, kept at 600°C for 20-30 minutes, then left to stand for about 3 minutes, poured into a metal mold, cooled and solidified in an argon atmosphere; after taking out the skin, remelt twice in the same way to make The components spread evenly and are finally cast into rods.
PUM
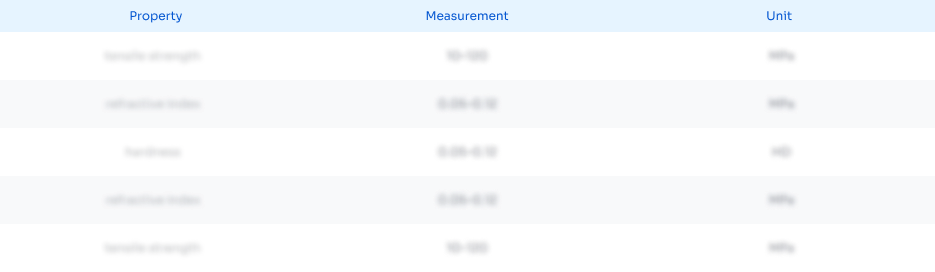
Abstract
Description
Claims
Application Information

- Generate Ideas
- Intellectual Property
- Life Sciences
- Materials
- Tech Scout
- Unparalleled Data Quality
- Higher Quality Content
- 60% Fewer Hallucinations
Browse by: Latest US Patents, China's latest patents, Technical Efficacy Thesaurus, Application Domain, Technology Topic, Popular Technical Reports.
© 2025 PatSnap. All rights reserved.Legal|Privacy policy|Modern Slavery Act Transparency Statement|Sitemap|About US| Contact US: help@patsnap.com