Flexing-resistant nylon material for cable jacket and preparation method of flexing-resistant nylon material
A technology of resistance to tortuosity and cable protection, which is applied in the field of polymer material processing, can solve the problem that the resistance to tortuosity cannot meet the needs of the market, etc., to improve wear resistance and aging resistance, improve flame retardant performance, and improve mechanical properties. Effect
- Summary
- Abstract
- Description
- Claims
- Application Information
AI Technical Summary
Problems solved by technology
Method used
Image
Examples
Embodiment Construction
[0012] A twist-resistant nylon material for cable sheath, made of the following raw materials (kg): nylon 1139, thermoplastic polyurethane elastomer 28, styrene-isoprene-butadiene terpolymer 20, nano-diamond 22. Aluminum basic sodium carbonate 12, brominated epoxy resin 19, isocetyl palmitate 4, N,N-dimethyl p-toluenesulfonamide 7, tri(butoxyethyl) phosphate 12, Magnesium oleate 4, stannous fluoroborate 3, barium molybdate 6, aramid pulp 11, additive 3.5;
[0013] The preparation method of described auxiliary agent is as follows: a, get the raw material of following weight (kg): superfine ice skating powder 18, cerium isooctanoate 2.5, triisopropylsilyl acrylate 6, hexamethylphosphoric acid triamide 10, 1,3-Propyl sultone 7, polyoxypropylene dipivalate 4.5, nano-titanium nitride 10, yttrium oxide 1.5, aluminum p-tert-butylbenzoate 4.5, resorcinol monobenzoate 3. Di(2-ethylhexyl) phosphate 7; b. Take superfine ice skating powder, triisopropyl silyl acrylate, and hexamethylphos...
PUM
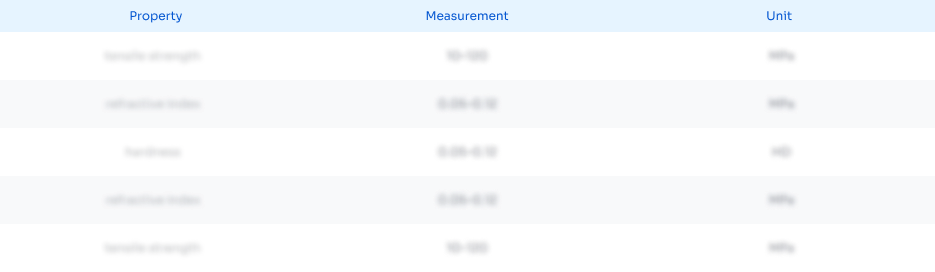
Abstract
Description
Claims
Application Information

- R&D
- Intellectual Property
- Life Sciences
- Materials
- Tech Scout
- Unparalleled Data Quality
- Higher Quality Content
- 60% Fewer Hallucinations
Browse by: Latest US Patents, China's latest patents, Technical Efficacy Thesaurus, Application Domain, Technology Topic, Popular Technical Reports.
© 2025 PatSnap. All rights reserved.Legal|Privacy policy|Modern Slavery Act Transparency Statement|Sitemap|About US| Contact US: help@patsnap.com