Self-grinding diamond tool matrix material
A diamond tool and matrix material technology, which is applied in the field of diamond tool matrix materials, can solve the problems that the advantages of pre-alloyed powder cannot be brought into play, and the formability is not good, so as to achieve good fluidity and shrinkage, short sintering time, The effect of high edge
- Summary
- Abstract
- Description
- Claims
- Application Information
AI Technical Summary
Problems solved by technology
Method used
Examples
Embodiment 1
[0026] Self-grinding diamond tool matrix material, its weight percentage composition is: FAM generation cobalt pre-alloy powder 95% and silicon carbide (200#) 5%; Wherein, the weight percentage composition of FAM generation cobalt pre-alloy powder is: Nano-sized honeycomb structure electrolytic iron-nickel-cobalt alloy powder 50%; copper-iron alloy powder 40%; copper-tin alloy powder 10%. Using this matrix material to make diamond tools—ceramic dry grinding wheels, solves the problem of easy edge loss with bronze-based matrix materials in the past, prolongs the grinding life by more than 30%, and reduces production costs by more than 25%.
Embodiment 2
[0028] Self-grinding diamond tool matrix material, its weight percentage composition is: FAM generation cobalt pre-alloy powder 97% and cooked mica (200#) 3%; Wherein, the weight percentage composition of FAM generation cobalt pre-alloy powder is: Electrolytic iron-nickel-cobalt alloy powder with nano-sized honeycomb structure 25%; copper-iron alloy powder 60%; copper-tin alloy powder 15%. Using the matrix material to make a diamond tool—marble medium-diameter saw blade, compared with the previous brass-based matrix material, can reduce the amount of diamond used.
Embodiment 3
[0030] Self-grinding diamond tool matrix material, its weight percentage composition is: FAM generation cobalt pre-alloy powder 99% and silicon carbide (200#) 1%; Wherein, the weight percentage composition of FAM generation cobalt pre-alloy powder is: Nano-sized honeycomb structure electrolytic iron-nickel-cobalt alloy powder 30%; copper-iron alloy powder 50%; copper-tin alloy powder 20%. Using this carcass material to make diamond tools - small stone cutting discs can improve processing efficiency by more than 20%, reduce production costs by more than 15%, and the yield of automatic cold pressing can reach more than 98%. The shrinkage and product retention of the pressureless sintering process It has good performance of no deformation and no cracking, which greatly improves the yield of products and ensures the stability of product performance.
PUM
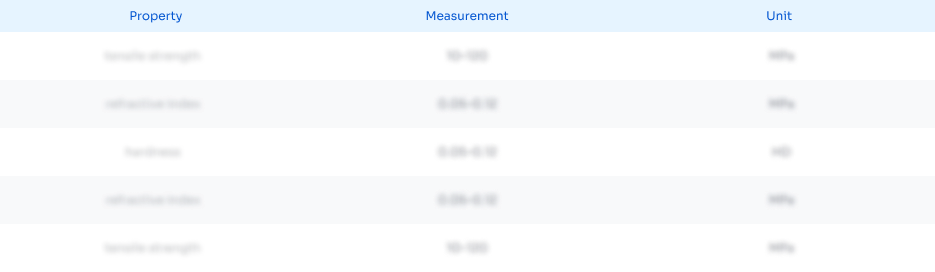
Abstract
Description
Claims
Application Information

- Generate Ideas
- Intellectual Property
- Life Sciences
- Materials
- Tech Scout
- Unparalleled Data Quality
- Higher Quality Content
- 60% Fewer Hallucinations
Browse by: Latest US Patents, China's latest patents, Technical Efficacy Thesaurus, Application Domain, Technology Topic, Popular Technical Reports.
© 2025 PatSnap. All rights reserved.Legal|Privacy policy|Modern Slavery Act Transparency Statement|Sitemap|About US| Contact US: help@patsnap.com