Method for preparing micron-grade stannic oxide powder
A tin dioxide, micron-level technology, applied in tin oxide and other directions, can solve the problems of incomplete reaction, high production cost, long process route, etc., and achieve the effect of simple production equipment, prevention of agglomeration polymerization, and easy agglomeration polymerization.
- Summary
- Abstract
- Description
- Claims
- Application Information
AI Technical Summary
Problems solved by technology
Method used
Image
Examples
Embodiment 1
[0021] Take a certain amount of reagent grade sodium stannate, use pure water to prepare a sodium stannate solution with a concentration of 50g / L, heat it in a water bath to 60°C, start stirring, add dropwise an ammonium bicarbonate solution with a concentration of 100g / L, and react to The pH value of the reaction solution is 9.0, stop the dripping, and filter to obtain the hydrated tin hydroxide solid; use pure water to beat the hydrated tin hydroxide solid with a liquid-solid ratio of 4:1, and adjust the pH value of the hydrated tin hydroxide slurry with nitric acid To 2, at this time, the hydrated tin hydroxide has been converted into metastannic acid, and the residual sodium carbonate has been completely decomposed into nitrates with stronger water solubility, washed 5 times with pure water, and the liquid-solid ratio is 3:1. Then wash once with ethanol with a mass ratio of 95%, the liquid-solid ratio is 2:1, and carry out solid-liquid separation. The solid is metastannic a...
Embodiment 2
[0023] Take a certain amount of industrial-grade sodium stannate, use pure water to prepare a sodium stannate solution with a concentration of 100g / L, add 10g of sodium stannate solution per liter of sodium stannate solution, add a 5% sodium sulfide solution by mass, and stir to react 30 minutes, then filter, heat the filtrate to 70°C, then add 20g of hydrogen peroxide with a mass ratio of 30%-50% per liter of sodium stannate solution, stir and react for 30 minutes, and then raise the temperature to 80 Stir and react at -90°C for 20 minutes, remove excess hydrogen peroxide, cool the reaction solution to room temperature, filter, add reagent grade hydrated tin hydroxide to the filtrate at a rate of 5 g per liter of filtrate, stir and adsorb for 1 hour, filter to obtain purified sodium stannate solution; add sodium dodecyl sulfate at a rate of 0.5 g per liter of sodium stannate solution, heat up to 80°C, start stirring, add dropwise ammonium bicarbonate solution with a concentrat...
example 3
[0025]Take a certain amount of reagent grade sodium stannate, configure it with pure water to form a sodium stannate solution with a concentration of 200g / L, add sodium dodecylbenzenesulfonate at a rate of 0.1g per liter of sodium stannate solution, and heat up to 90°C, start stirring, dropwise add ammonium carbonate solution with a concentration of 100g / L, react until the pH value of the reaction solution is 9.5, stop dropping, filter to obtain hydrated tin hydroxide solid; use pure water to dissolve the obtained hydrated tin hydroxide The solid is beaten with a liquid-solid ratio of 4:1, and the pH value of the hydrated tin hydroxide slurry is adjusted to 4 with oxalic acid. At this time, the hydrated tin hydroxide has been converted into metastannic acid, and the residual carbonate has been completely decomposed into water-soluble Stronger oxalate, wash 3 times with pure water, the liquid-solid ratio is 6:1, then wash 2 times with absolute ethanol, the liquid-solid ratio is ...
PUM
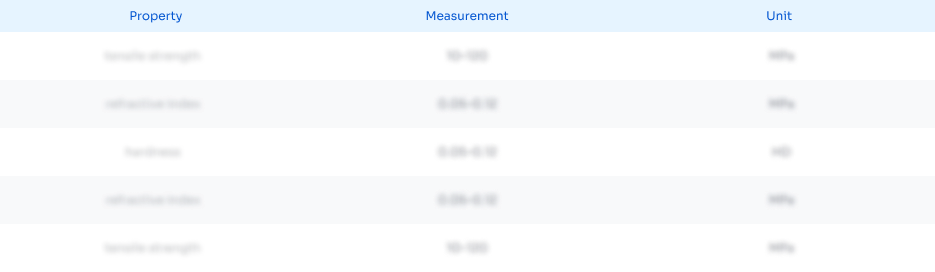
Abstract
Description
Claims
Application Information

- R&D
- Intellectual Property
- Life Sciences
- Materials
- Tech Scout
- Unparalleled Data Quality
- Higher Quality Content
- 60% Fewer Hallucinations
Browse by: Latest US Patents, China's latest patents, Technical Efficacy Thesaurus, Application Domain, Technology Topic, Popular Technical Reports.
© 2025 PatSnap. All rights reserved.Legal|Privacy policy|Modern Slavery Act Transparency Statement|Sitemap|About US| Contact US: help@patsnap.com