Lead melting copper removal refining process for industrial frequency coreless-type electric induction furnace
An induction furnace, copper refining technology, applied in the direction of photography technology, photography auxiliary technology, process efficiency improvement, etc., can solve problems such as difficulty in manufacturing lead pots, poor temperature control accuracy, and flue gas pollution to the environment. The effect of good operation, fast lead melting speed and low energy consumption index
- Summary
- Abstract
- Description
- Claims
- Application Information
AI Technical Summary
Problems solved by technology
Method used
Examples
Embodiment 1
[0016] 1. Send 50 tons of by-product coarse lead raw materials produced after the electric zinc smelting process into the heat-resistant steel (Cr-Mn-N) lead-melting crucible made by the automatic submerged arc welding process of beveling, and use A 600kw50t power frequency centerless induction furnace is used for heating and melting, the melting temperature is 460°C, and the melting time is 4 hours, then continue heating to heat the melt to 530°C. reduce the temperature from 530°C to 330°C), use the principle that the solubility of copper in lead decreases sharply with the decrease of temperature, so that copper is smelted out from crude lead, and 50 kg of sawdust is mixed into the metal liquid to make The copper is better separated from the lead liquid, the copper dross is removed by scooping, the copper dross is sent to the converter for reduction smelting, and the crude lead after reduction smelting is sent to the lead melting crucible.
[0017] 2. Adjust the temperature o...
Embodiment 2
[0021] 1. Send 50 tons of by-product coarse lead raw materials produced after the electric zinc smelting process into the heat-resistant steel (Cr-Mn-N) lead-melting crucible made by the automatic submerged arc welding process of beveling, and use A 600kw50t power frequency centerless induction furnace is used for heating and melting, the melting temperature is 460°C, and the melting time is 4 hours, then continue heating to heat the melt to 530°C. reduce the temperature from 530°C to 330°C), use the principle that the solubility of copper in lead decreases sharply with the decrease of temperature, so that copper is smelted out from crude lead, and 50 kg of sawdust is mixed into the metal liquid to make The copper is better separated from the lead liquid, and the copper dross is removed by scooping. The copper dross is sent to the converter for reduction smelting, and the crude lead after reduction smelting is sent to the lead melting crucible.
[0022] 2. Adjust the temperatu...
Embodiment 3
[0026] 1. Feed the purchased 50 tons of crude lead into the lead-melting crucible made of heat-resistant steel (Cr-Mn-N) welded by the groove automatic submerged arc welding process, and use a 600kw50t power frequency centerless induction Heat and melt in an electric furnace, the melting temperature is 480°C, and the melting time is 4 hours, then continue heating to heat the melt to 530°C, and then use the residual lead to continue the pot and spray water to cool down (in half an hour, the temperature is reduced from 530°C to 530°C). ℃ to 330-340 ℃), using the principle that the solubility of copper in lead decreases sharply with the decrease of temperature, the copper is smelted out from the crude lead, and 50 (kg) sawdust is mixed in the smelted metal liquid, The copper is separated from the smelt, the copper scum is removed, the copper scum is sent to the converter for reduction smelting, and the crude lead after reduction smelting is sent to the lead melting crucible to ent...
PUM
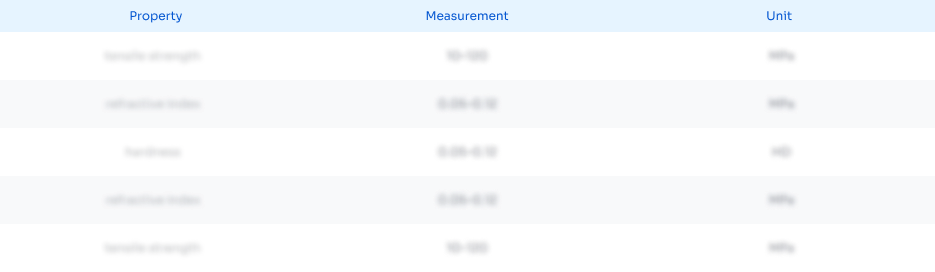
Abstract
Description
Claims
Application Information

- R&D
- Intellectual Property
- Life Sciences
- Materials
- Tech Scout
- Unparalleled Data Quality
- Higher Quality Content
- 60% Fewer Hallucinations
Browse by: Latest US Patents, China's latest patents, Technical Efficacy Thesaurus, Application Domain, Technology Topic, Popular Technical Reports.
© 2025 PatSnap. All rights reserved.Legal|Privacy policy|Modern Slavery Act Transparency Statement|Sitemap|About US| Contact US: help@patsnap.com