Method for extracting tungsten and molybdenum in high molybdenum scheelite
A scheelite and extraction technology, which is applied in the field of extracting tungsten and molybdenum, can solve the problems of circuitous and lengthy treatment process, complex tungsten and molybdenum separation process, and large amount of leaching agent, so as to reduce the processing burden, low cost and high leaching rate. Effect
- Summary
- Abstract
- Description
- Claims
- Application Information
AI Technical Summary
Problems solved by technology
Method used
Image
Examples
Embodiment 1
[0022] Scheelite (containing WO 3 53%, Mo 2.1%) use sulfur-phosphorus mixed acid for two-stage cyclic leaching, and the leaching conditions are controlled at H 2 SO 4 200g / L, H 3 PO 4 300g / L, leaching temperature 60℃, leaching time 3h, liquid-solid ratio 4:1. The total tungsten leaching rate is 99.2%, and the total molybdenum leaching rate is 99.1%. Cool the leaching solution to 30°C, the crystallization rate of tungsten is 93.5%, and the WO of the obtained primary phosphotungstic acid 3 / Mo=196, its XRD is as follows figure 2 shown. Dissolve primary phosphotungstic acid in 2mol / L H at 65°C 2 SO 4 and 2mol / L H 3 PO 4 in the mixed acid solution until the WO in the solution 3 The concentration is 150g / L, and then the solution is cooled to 30°C, the crystallization rate of tungsten is 93.2%, and the obtained secondary phosphotungstic acid WO 3 / Mo=579. After the phosphotungstic acid crystal is treated by the classic ammonia solution-magnesium salt removal-molybdenum ...
Embodiment 2
[0024] Scheelite (containing WO 3 42%, Mo 6.7%) use sulfur-phosphorus mixed acid for three-stage cyclic leaching, and the leaching conditions are controlled at H 2 SO 4 300g / L, H 3 PO 4 150g / L, leaching temperature 75℃, leaching time 4h, liquid-solid ratio 5:1. The total tungsten leaching rate was 98.7%, and the total molybdenum leaching rate was 99.3%. Cool the leaching solution to 25°C, the crystallization rate of tungsten is 93.4%, and the WO of the obtained primary phosphotungstic acid crystal 3 / Mo=113. Dissolve the primary crystallization product in 3.5mol / L H at 80°C 2 SO 4 in solution until WO in solution 3 The concentration is 200g / L, and then cooled to 25°C, the crystallization rate of tungsten is 94.2%, and the obtained secondary crystallization product WO 3 / Mo=423. After the phosphotungstic acid is subjected to the classic ammonia solution-magnesium salt removal-molybdenum removal-evaporation crystallization process, the APT of the national 0-level stand...
Embodiment 3
[0026] Scheelite (containing WO 3 65%, Mo 8.5%) use sulfur and phosphorus mixed acid for two-stage cyclic leaching, and the leaching conditions are controlled at H 2 SO 4 Concentration 250g / L, H 3 PO 4 250g / L, leaching temperature 90℃, leaching time 2h, liquid-solid ratio 6:1. The total tungsten leaching rate is 99.1%, and the total molybdenum leaching rate is 98.8%. Cool the leaching solution to 30°C, the crystallization rate of tungsten is 91.7%, and the WO of the obtained primary phosphotungstic acid crystal 3 / Mo=183. Dissolve the primary crystallization product in 4mol / L H at 85°C 2 SO 4 and 1mol / L H 3 PO 4 in the mixed acid solution until the WO in the solution 3 The concentration is 100g / L, then cooled to 35°C, the crystallization rate of tungsten is 93.5%, the WO of the obtained secondary phosphotungstic acid crystal 3 / Mo=626, the crystalline product can obtain the APT of the national 0-level standard after the classic ammonia solution-magnesium salt remova...
PUM
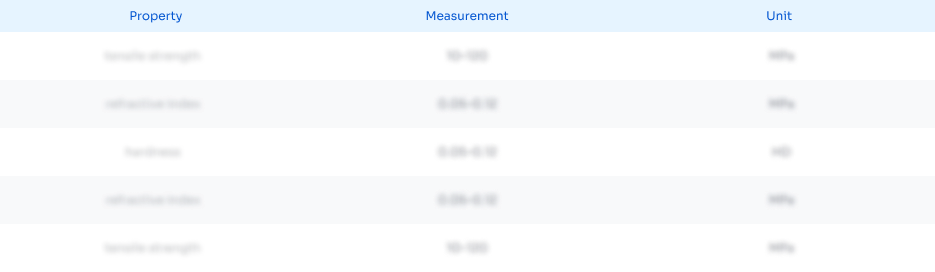
Abstract
Description
Claims
Application Information

- Generate Ideas
- Intellectual Property
- Life Sciences
- Materials
- Tech Scout
- Unparalleled Data Quality
- Higher Quality Content
- 60% Fewer Hallucinations
Browse by: Latest US Patents, China's latest patents, Technical Efficacy Thesaurus, Application Domain, Technology Topic, Popular Technical Reports.
© 2025 PatSnap. All rights reserved.Legal|Privacy policy|Modern Slavery Act Transparency Statement|Sitemap|About US| Contact US: help@patsnap.com