Boron-containing titanium carbide nitride based metal ceramic cutter material and preparation technique thereof
A titanium carbonitride and ceramic tool technology, applied in the field of material science, can solve the problems of unsatisfactory tool durability and service life, high cutting temperature, large cutting force, etc., and achieve improved performance indicators, improved surface quality, and improved cutting The effect of speed increase
- Summary
- Abstract
- Description
- Claims
- Application Information
AI Technical Summary
Problems solved by technology
Method used
Examples
Embodiment 1
[0026] The mass fractions were 0.005% elemental boron, 5.5% WC, 3% TaC, 9% NbC, 10% Mo 2 C, 50% of Ti (CN), 10% of TiC, 6% of Co, 6% of Ni and 0.495% of C are mixed, and all kinds of raw materials are micron powders. Water ethanol is used as the grinding medium, hard metal is used as the grinding body, polyethylene glycol (PEG) and 1.5% polyvinylpyrrolidone (PVP) are added to the total weight of the mixed raw material powder, the ball-to-material ratio is 1: 8, and ball milling The dispersion time is 55 hours, and the slurry dispersed by the ball mill is spray-dried, and the outlet temperature of the nozzle is 90°C; then it is precisely pressed and formed, and the relative density of the green compact is 53%; ℃, the time is 3 hours; vacuum sintering is carried out at 1480 ℃, and the temperature is kept for 70 minutes. After cooling down, the obtained cermet product is ground into a tool of corresponding specification.
[0027] Cutting experiments show that the boron-containin...
Embodiment 2
[0029] The mass fractions were 0.3% titanium diboride, 16.2% WC, 6% TaC, 6% NbC, 5% Mo 2 C, 48% of Ti (CN), 3% of TiC, 8% of Co, 7% of Ni and 0.5% of C are mixed, and all kinds of raw materials are micron powders. Water ethanol is used as the grinding medium, hard metal is used as the grinding body, polyethylene glycol (PEG) and 1.5% polyvinylpyrrolidone (PVP) are added to the total weight of the mixed raw material powder, the ball-to-material ratio is 1: 8, and ball milling The dispersion time is 48 hours. The slurry dispersed by ball milling is spray-dried, and the outlet temperature of the nozzle is 90°C; then it is precisely pressed and formed, and the relative density of the green compact is 54%; The time is 3 hours; at 1480°C in H 2 Sintering under Ar and Ar atmosphere, heat preservation for 70 minutes, after cooling down, grind the obtained cermet product into cutters of corresponding specifications.
[0030] Cutting experiments show that the boron-containing Ti(CN)-b...
Embodiment 3
[0032] Mix the mass fractions of 2.3% molybdenum boride, 15% WC, 2% NbC, 61.7% Ti(CN), 3.8% TiC, 7% Co, 8% Ni and 0.2% C, all raw materials are micron powder , put the mixed raw material powder into a ball mill, use absolute ethanol as the grinding medium, use cemented carbide as the grinding body, add 3% polyethylene glycol (PEG) and 1.5% polyvinylpyrrolidone by the total weight of the mixed raw material powder (PVP), the ball-to-material ratio is 1:9, the ball mill dispersion time is 50 hours, the slurry after the ball mill dispersion is spray-dried, and the nozzle outlet temperature is 90°C; then it is precisely pressed and formed, and the relative density of the green compact is 53%; Pre-burning, the pre-burning temperature is 200-500°C, and the pre-burning time is 3 hours; at 1480°C H 2 Sintering under Ar and Ar atmosphere, heat preservation for 70 minutes, after cooling down, grind the obtained cermet product into cutters of corresponding specifications.
[0033] Cuttin...
PUM
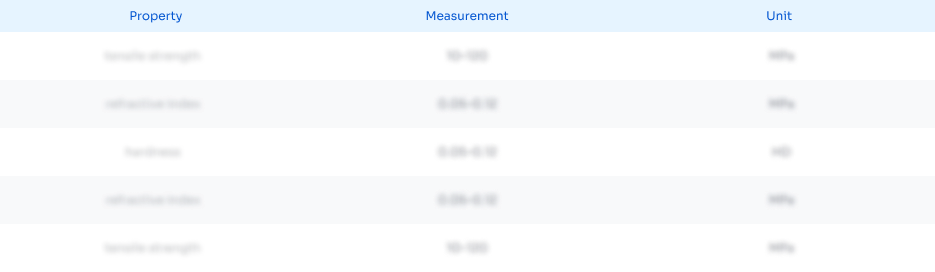
Abstract
Description
Claims
Application Information

- R&D
- Intellectual Property
- Life Sciences
- Materials
- Tech Scout
- Unparalleled Data Quality
- Higher Quality Content
- 60% Fewer Hallucinations
Browse by: Latest US Patents, China's latest patents, Technical Efficacy Thesaurus, Application Domain, Technology Topic, Popular Technical Reports.
© 2025 PatSnap. All rights reserved.Legal|Privacy policy|Modern Slavery Act Transparency Statement|Sitemap|About US| Contact US: help@patsnap.com